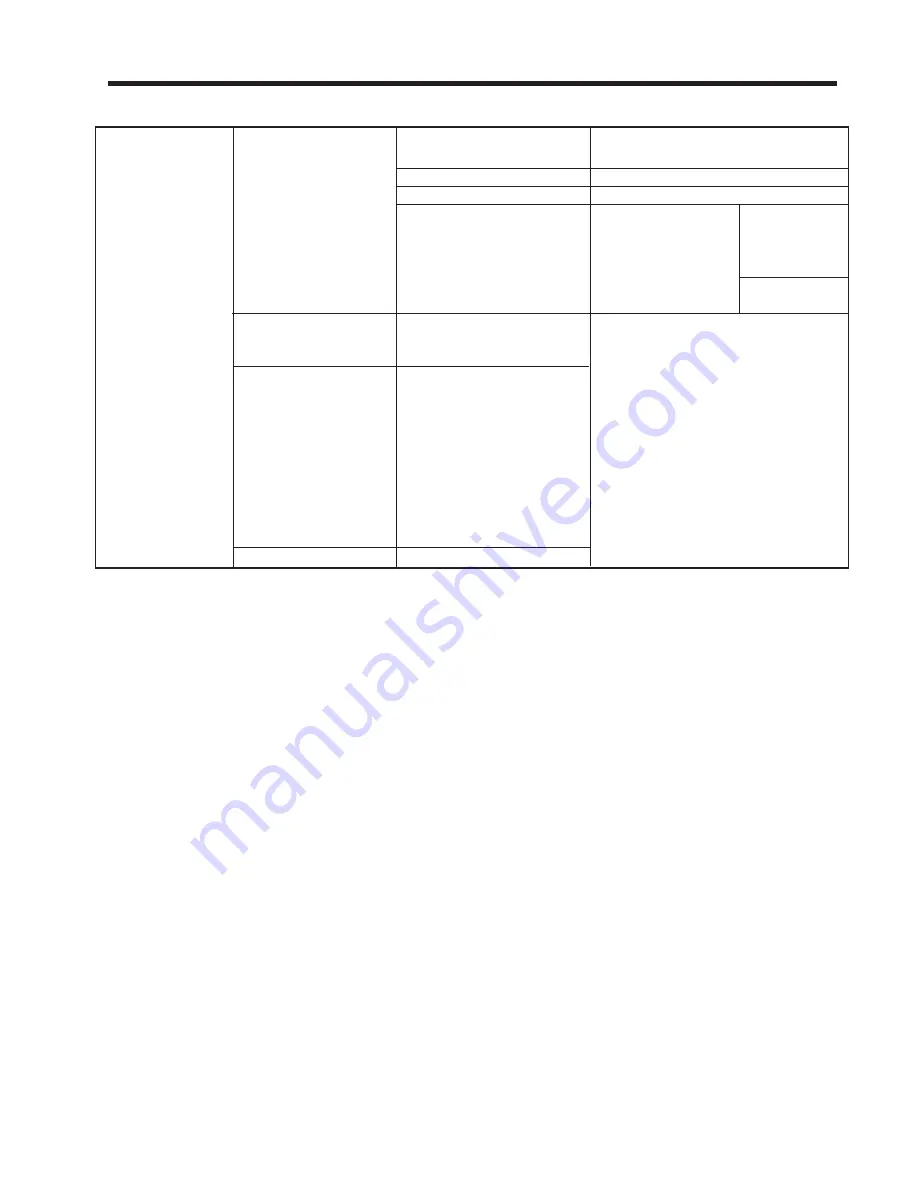
5-13
CQO:1010PVXFM-3
Section 5
Liquid Table
Table Active
No
Yes
LiquIdent Slope
x.xxx
(numeric entry)
Pressure Slope
x.xxx
(numeric entry)
LiquIdent Index
Add Index
Index Value
(numeric entry)
Viscosity @ 400
(numeric entry)
Visc Slope @ 400
(numeric entry)
Kill Index @ 400
No
Yes
Temp. Range
-40F to 450F
-40F to 250F
-40F to 375F
Pipe Config
Full Developed (default)
(Change to Upstream
1 Elbow
Piping)
Dbl Elbow +
Dbl Elbow -
Valve
Expander
Reducer
Norm Entry
Header Inlet
Intrusions
Anomaly Diams
xxxx (numeric entry)
APPLICATION DATA MENU STRUCTURE
(continued)
Application Data
Summary of Contents for SITRANS FUH1010PVDX
Page 2: ......
Page 4: ......
Page 8: ......
Page 12: ......
Page 20: ......
Page 24: ......
Page 32: ......
Page 184: ......
Page 204: ......
Page 206: ......
Page 208: ......
Page 216: ......
Page 219: ...21614 C 1010X 7 CAUTION ...
Page 222: ...STANDARD UPRIGHT INSTALLATION 21614 C 1010X 8 ...
Page 223: ...21614 C 1010DX 7 CAUTION ...
Page 227: ...21614 C 1010DX 8 STANDARD UPRIGHT INSTALLATION ...
Page 228: ......
Page 229: ......
Page 230: ......
Page 231: ......
Page 232: ......
Page 233: ......
Page 234: ...1011HNFS 7 21614 C ...
Page 235: ...1011HNFS 7 C 21614 ...
Page 237: ......
Page 241: ...1011NFPS 7 C 21614 REFLECT MODE OPERATION DIRECT MODE OPERATION AUXILIARY VIEW ...
Page 242: ...1011NFPS 8 21614 C ...
Page 243: ......
Page 249: ......
Page 250: ......
Page 251: ...1012TB 8 INSTALLATION OUTLINE 1011 SERIES TEST BLOCK 21614 C ...
Page 254: ...1012TN 8 OUTLINE DIMENSIONS REFLECT MODE DIRECT MODE 1012TN SERIES 21614 C MOUNTING TRACK ...
Page 257: ...1012TNH 8 OUTLINE DIMENSIONS REFLECT MODE DIRECT MODE 1012TNH SERIES 21614 C MOUNTING TRACK ...
Page 258: ...1012F DB 7 21614 C ...
Page 259: ......
Page 260: ......
Page 261: ......
Page 262: ...21614 C OUTLINE DIMENSIONS WELD SEAL TYPE 1013WS 8 ENCLOSURES ...
Page 263: ......
Page 264: ......
Page 265: ......
Page 266: ......
Page 267: ......
Page 269: ...21614 C TEMPERATURE SENSOR DEDICATED NEMA 4 OUTLINE DIMENSIONS 991TN 8 5 4 3 2 1 ...
Page 270: ......
Page 271: ......
Page 273: ......
Page 274: ......
Page 275: ......
Page 276: ......
Page 286: ......
Page 304: ......
Page 307: ......