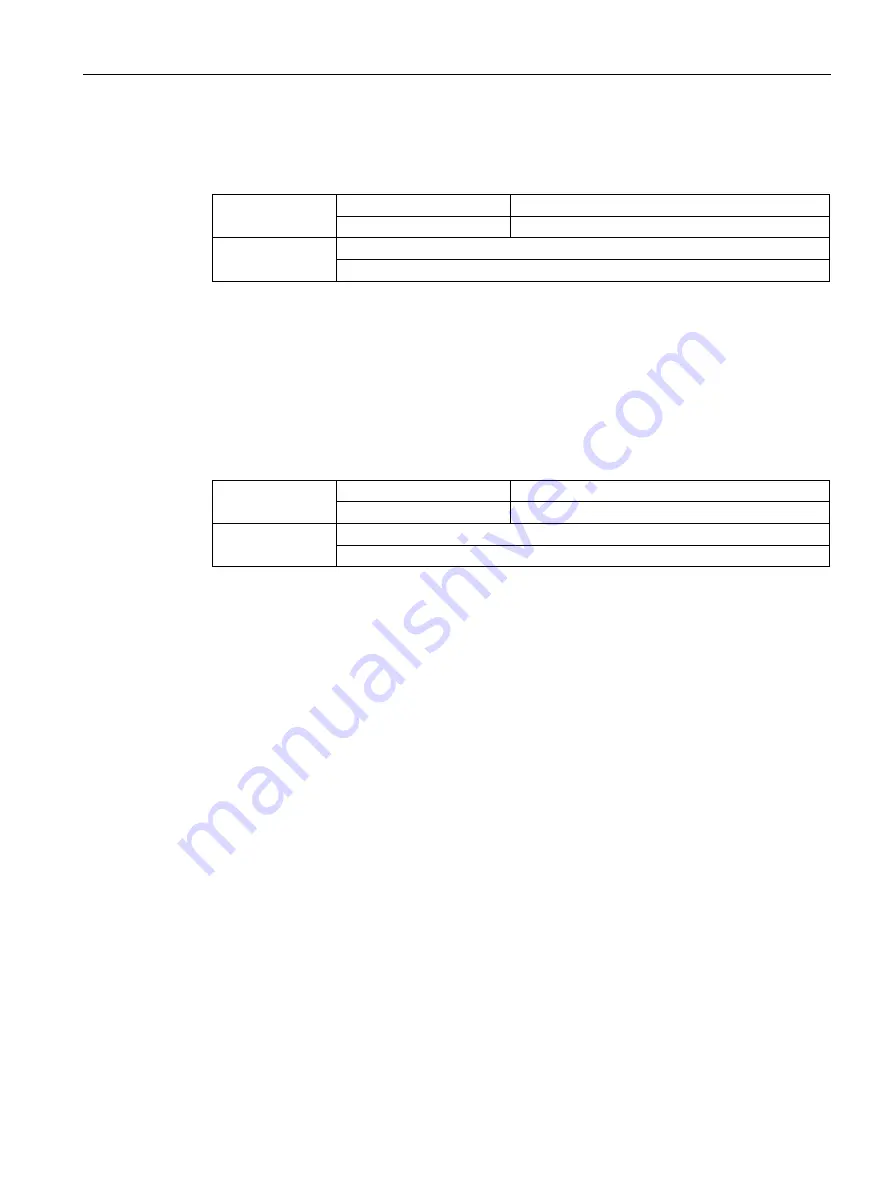
Commissioning
6.5 Quick Start Wizards
HydroRanger 200 HMI
Operating Instructions, 06/2018, A5E36281317-AC
79
Maximum head
The level value associated with Maximum Flow, in Units (2.1.1.) (Page 162).
Index
Single-point model
Dual-point model
Global
Transducer
Values
Range: -999 ... 999999
Preset: Span value (2.2.2.) (Page 169)
This represents the highest head level supported by the PMD and works in conjunction with
Maximum flow (2.13.4.3.) (Page 243) to define the highest point in the exponential curve.
Use it when the PMD requires a maximum head and flow reference point. This would include
Exponential, Palmer-Bowlus Flume, H-Flume, and Universal breakpoints.
Zero head
The distance above Empty (2.2.4.) (Page 170), in Units (2.1.1.) (Page 162) representing
zero head (and zero flow).
Index
Single-point model
Dual-point model
Global
Transducer
Values
Range: -999 ... 9999
Preset: 0.000
This feature can be used for most weirs and some flumes (e.g. Palmer-Bowlus) where the
zero reference is at a higher elevation than the channel bottom.
Summary of Contents for HydroRanger 200 HMI
Page 2: ......
Page 24: ...Safety notes HydroRanger 200 HMI 22 Operating Instructions 06 2018 A5E36281317 AC ...
Page 354: ...Updating software HydroRanger 200 HMI 352 Operating Instructions 06 2018 A5E36281317 AC ...
Page 362: ......
Page 403: ......