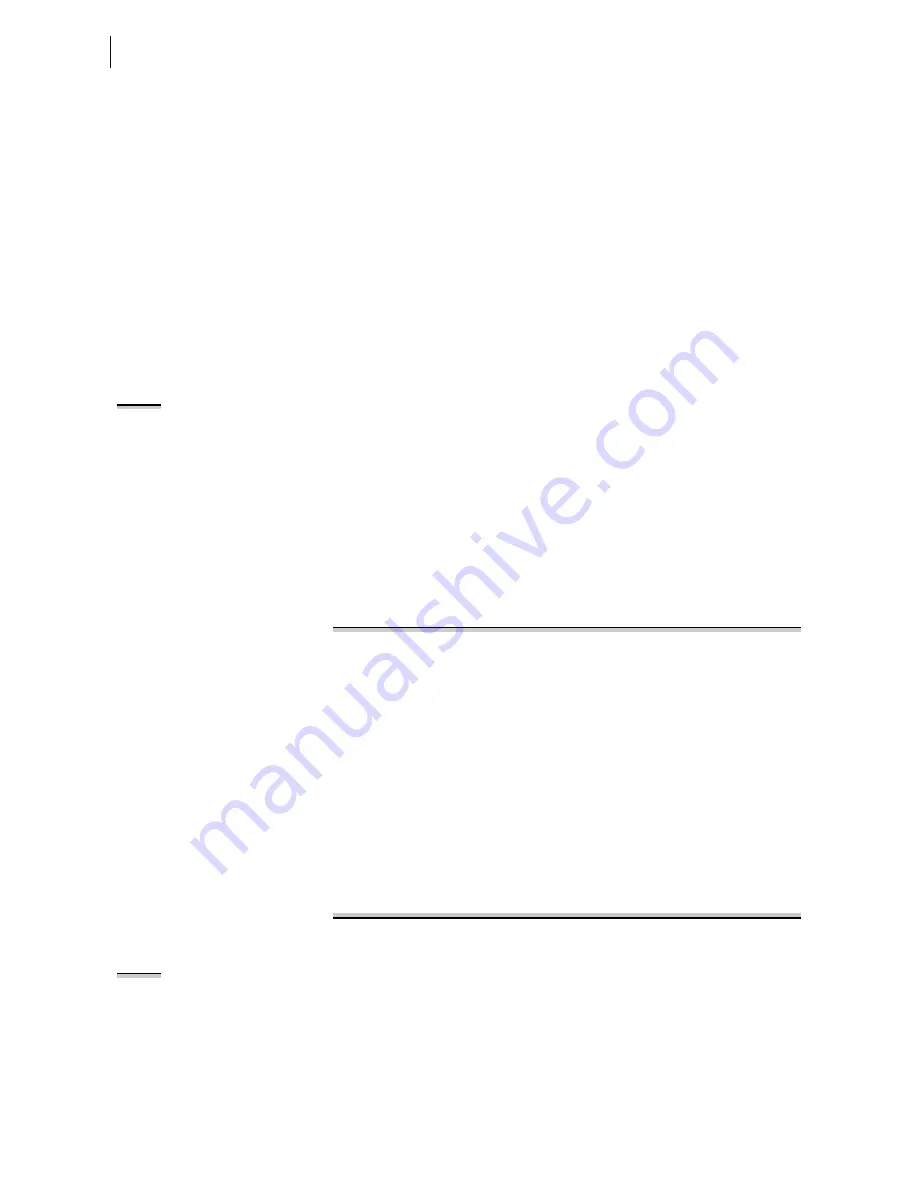
5.16
SEL-387-0, -5, -6 Relay
Instruction Manual
Date Code 20170601
Metering and Monitoring
Thermal Monitor (SEL-387-6 Relay)
Thermal Event Report
Function (THE n
Command)
Whenever a thermal alarm condition is set (load conditions are Warning 1,
Warning 2, or Warning 3), the SEL-387-6 saves a snapshot of the thermal
status of the transformer(s) in EEPROM. The five most recent thermal events
are saved. If the command for retrieving the nth saved thermal event report is
THE
n
, where
n
is a number from one to five,
THE 1
will display the most
recent event report while
THE 5
will display the oldest thermal event report.
The format and data for the
THE
n
report are the same as for the
THE
report.
Thermal Profile Data
Report Function
(THE H and THE D
Commands)
The SEL-387-6 stores two types of trend data: one set on an hourly basis for
the last 24 hours; a second set on a daily basis for the last 31 days. The format
of the retrieved data report is suitable for display in Microsoft
®
Excel.
Hourly Profile Data Report (THE H Command)
The SEL-387-6 stores the following data on an hourly basis for the last 24
hours. The data are stored at the beginning of each hour.
➤
One-hour average ambient temperature
➤
One-hour average calculated top-oil temperature
➤
One-hour average measured top-oil temperature
➤
One-hour average winding hot-spot temperature
➤
One-hour average per-unit load current
➤
One-hour average insulation aging acceleration factor (FAA)
The format for the
THE H
report is as follows:
=>>
THE H <Enter>
XFMR 1 Date: 04/24/00 Time: 13:20:03.956
STATION A
FID=SEL-387-6-X117-V0-Z001001-D20000419
Transformer 1
Ambient Calc Measured Load
Date Time Temp Top Oil Top Oil Hot Spot Current FAA
04/24/00 13:00* 15.0 32.5 -0- 32.7 0.04 0.0
04/24/00 12:00* 15.0 32.5 -0- 32.8 0.05 0.0
Transformer 2
Ambient Calc Measured Load
Date Time Temp Top Oil Top Oil Hot Spot Current FAA
04/24/00 13:00* 15.0 32.5 -0- 32.5 0.01 0.0
04/24/00 12:00* 15.0 32.5 -0- 32.5 0.02 0.0
Transformer 3
Ambient Calc Measured Load
Date Time Temp Top Oil Top Oil Hot Spot Current FAA
04/24/00 13:00* 15.0 32.5 -0- 32.7 0.05 0.0
04/24/00 12:00* 15.0 32.5 -0- 32.7 0.06 0.0
=>>
Daily Profile Data Report Function (THE D Command)
The relay stores the following on a daily basis (at midnight) for the last 30
days:
➤
Maximum ambient temperature
➤
Maximum calculated top-oil temperature
➤
Maximum measured top-oil temperature
NOTE:
When the thermal model is
applied on one three-phase
transformer (XTYPE = 3), the
SEL-387-6 displays only the values for
Transformer 1; when the thermal
model is applied on a set of three
single-phase transformers
(XTYPE = 1), the SEL-387-6 displays
the values for Transformer 1,
Transformer 2, and Transformer 3.
NOTE:
When the thermal model is
applied on one three-phase
transformer (XTYPE = 3), the
SEL-387-6 displays only the values for
Transformer 1; but when the thermal
model is applied on a set of three
single-phase transformers
(XTYPE = 1), the SEL-387-6 displays
the values for Transformer 1,
Transformer 2, and Transformer 3.
Summary of Contents for SEL-387-0
Page 6: ...This page intentionally left blank ...
Page 12: ...This page intentionally left blank ...
Page 50: ...This page intentionally left blank ...
Page 200: ...This page intentionally left blank ...
Page 248: ...This page intentionally left blank ...
Page 380: ...This page intentionally left blank ...
Page 422: ...This page intentionally left blank ...
Page 440: ...This page intentionally left blank ...
Page 458: ...This page intentionally left blank ...
Page 516: ...This page intentionally left blank ...