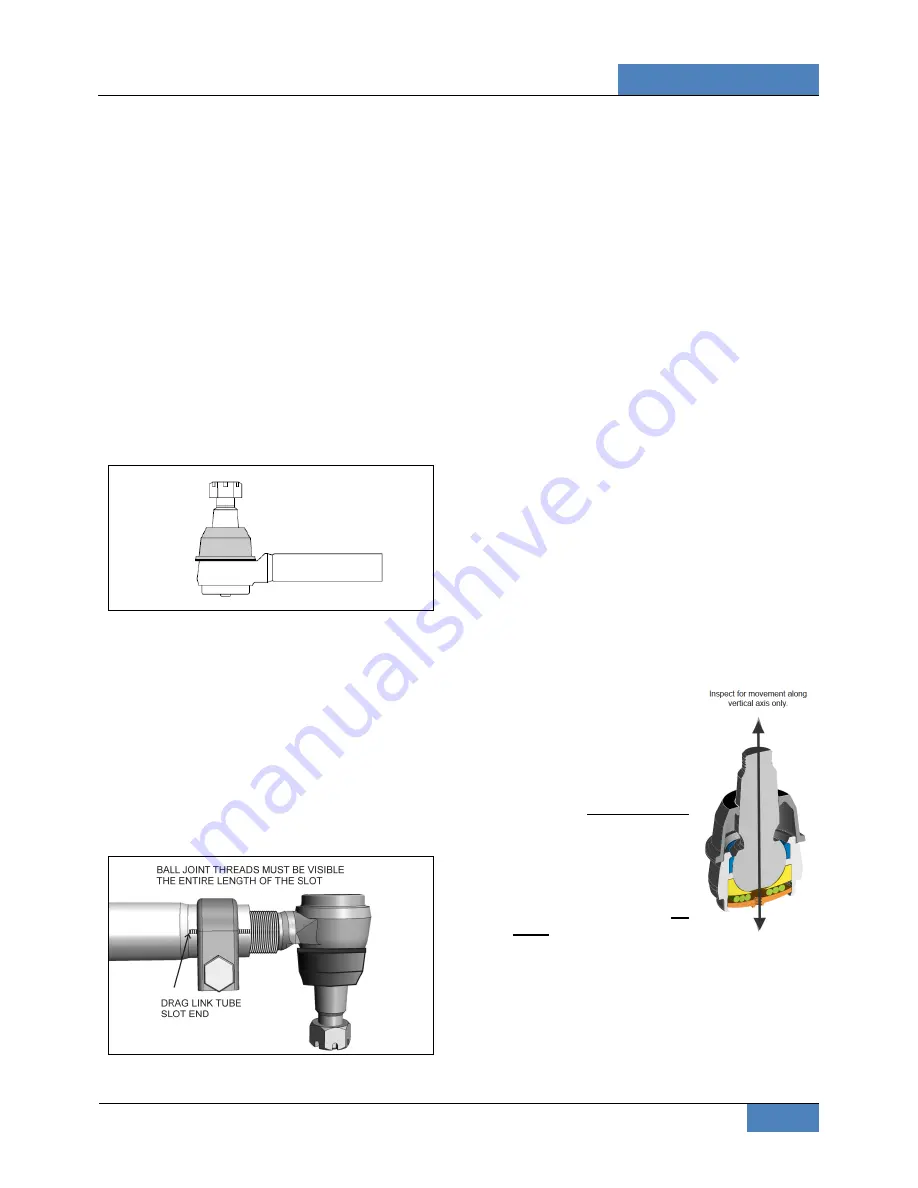
SECTION 14: STEERING
DOB 2490-2789 | X3-45 Commuter PA1605 Maintenance Manual (Section 14 revised April 2018)
17
12. Fit pin washer onto ball pin.
13. Screw pin nut onto ball pin then tighten to
175 lbf-ft (237 Nm) torque.
14. Using a 2lb hammer, tap tie rod arm to
"shock' ball pin into taper hole.
15. Re-torque pin nut to 175 lbf-ft (23 7Nm).
16. Fit split pin, if slot/hole are not in line, adjust
up to next slot.
Pin nut torque 175 lbf-ft, max pin nut torque
200 lbf-ft.
17. Re-charge ball socket with Shell “Retinax
LX” or equivalent grease through grease
fitting.
12.7 STRAIGHT BODY TYPE BALL JOINT
FIGURE 26: STRAIGHT BODY TYPE BALL JOINT
12.7.1 Visual
Inspection
Visually inspect for missing or damages
grease fittings and replace if required.
Damaged sealing boot or improper sealing
requires seal replacement.
Check ball joint connection for missing cotter
pins.
Check for looseness in the ball/socket
assembly.
FIGURE 27: ADEQUATE CLAMPING CONDITION
For adequate clamping, the ball joint threads
must be visible the entire length of the tube slot.
If not, the drag link must be adjusted or
replaced. It is either the wrong size, or improper
adjustment was used to compensate for another
problem (e.g. bent steering arm).
12.7.2
Straight Body Type Ball Joint End Play
And Looseness
What creates movement in sockets?
In each straight body type ball joints, the
compressive force of the spring creates resistive
torque by applying a constant load on the
bearing and stud.
As wear occurs on the components, the spring
creates less resistive torque. With less torque,
you no longer have the precise joint needed for
optimum steering, but you do still have a safe
linkage.
When all compression is lost, it’s
time to replace the linkage
. This wear can be
caused by impact, lack of lubrication and normal
wear.
1. With vehicle engine on, lightly rock the
steering wheel while checking for looseness
in any threaded joint. Observe any
looseness in the two mating tapers or any
movement of the ball pin nut. Any looseness
requires further inspection. If either of the
mating tapered parts shows distortion or
wear, both parts must be replaced.
2. With the engine off and
wheels straight ahead and
no force is being exerted
on the linkage by the
steering gear, push and
pull the ball joint in and
out by hand
(approximately 100 lbs.
force) in the direction of
the ball pin. If no
movement is detected,
the ball joint is safe.
Any
movement detected by
hand requires
replacement of the ball
joint.