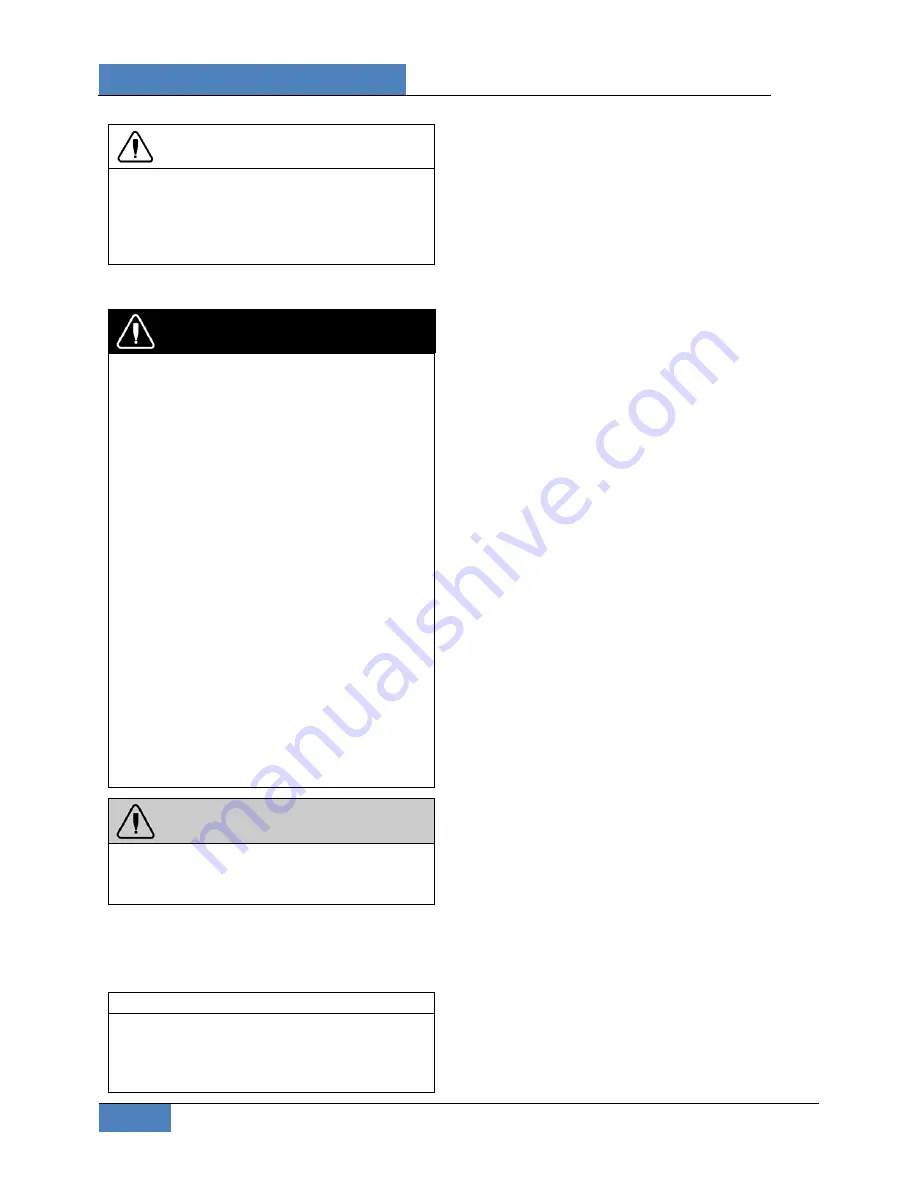
SECTION 12: BRAKE AND AIR SYSTEM
26
DOB 2490-2789 | X3-45 Commuter PA1605 Maintenance Manual (Final Version – Rev.2 April 2016)
CAUTION
Always clean air lines and fittings, and coat
pipe threads with teflon pipe sealant before
reconnecting air lines. Make sure the drain
hole of the brake chamber is in the lower
position for proper moisture evacuation.
28.4
BRAKE CHAMBER DISASSEMBLY
DANGER
Spring brake chambers, on drive and tag axles
contain an extremely high compressive force
spring, which can possibly cause serious
injury if special precautions are not taken
when working around this area.
To avoid such injury, the following recommen-
dations must be applied:
o
Prevost recommends the installation of a
new spring brake chamber if it is found to
be defective.
o
Spring brake chamber maintenance and/or
repair must be performed by trained and
qualified personnel only.
o
Before manually releasing spring brakes,
visually check spring brake for cracks
and/or corrosion.
o
On “MGM” brake chambers (drive axle),
make sure the release stud is properly
anchored in spring plate receptacle prior to
caging the spring.
o
Never stand in the axis line of the spring
brake chambers, especially when caging
the spring.
WARNING
To prevent personal injuries, brakes should be
inoperative prior to working on any of their
components.
1. Block the wheels to prevent the vehicle from
moving.
2. Safely support vehicle at the recommended
body jacking points.
NOTE
To gain access to a given brake air chamber,
the corresponding wheel can be removed
(refer to Section 13: "Wheels, Hubs and
Tires").
3. Exhaust compressed air from air system by
opening the drain valve of each reservoir.
4. For the drive axle brake chambers, manually
release spring brakes (refer to “
Emergen-
cy/Parking Brake Manual Release"
proce-
dure in this section).
5. Remove clamp ring, remove and discard the
existing diaphragm. Install the new dia-
phragm squarely on body.
6. Reverse the procedure for assembly. Tap
clamp ring to ensure proper seating. Check
for proper operation before placing vehicle in
service.
29. ANTI-LOCK BRAKING SYSTEM (ABS)
This device has been designed to ensure
stability and permit steering control of vehicle
during hard braking, and to minimize its stopping
distance whatever the road conditions are. On
slippery roads and generally in emergency
situations, over-braking frequently induces
wheel lock. The anti-lock braking system
provides maximum braking performance while
maintaining adequate steering control on
slippery roads.
The ABS continuously monitors wheel behavior
during braking. Sensors on each wheel of front
and drive axles (tag axle is slave to drive axle)
transmit data to a four channel electronic
processor which senses when any wheel is
about to lock. Modulator valves quickly adjust
the brake pressure (up to 5 times per second) to
prevent wheel locking. Each wheel is therefore
controlled according to the grip available
between its tire and the road.
With this device, the vehicle is brought to a halt
in the shortest possible time, while remaining
stable and under the driver's control.
Since the braking system has dual circuits, the
ABS is also provided with a secondary system
should a fault develop in the ABS. Anti-lock
systems are a parallel system which does not
hinder brake functioning in case of failure.
Braking system functions in normal, non
anti-lock controlled operation during ABS system
failure.
The ABS system consists of two diagonally
related circuits, only the half of the system which
has sustained damage or other fault is switched
off (i.e. wheels return to normal non-ABS
braking). The other diagonal half remains under
full ABS control.