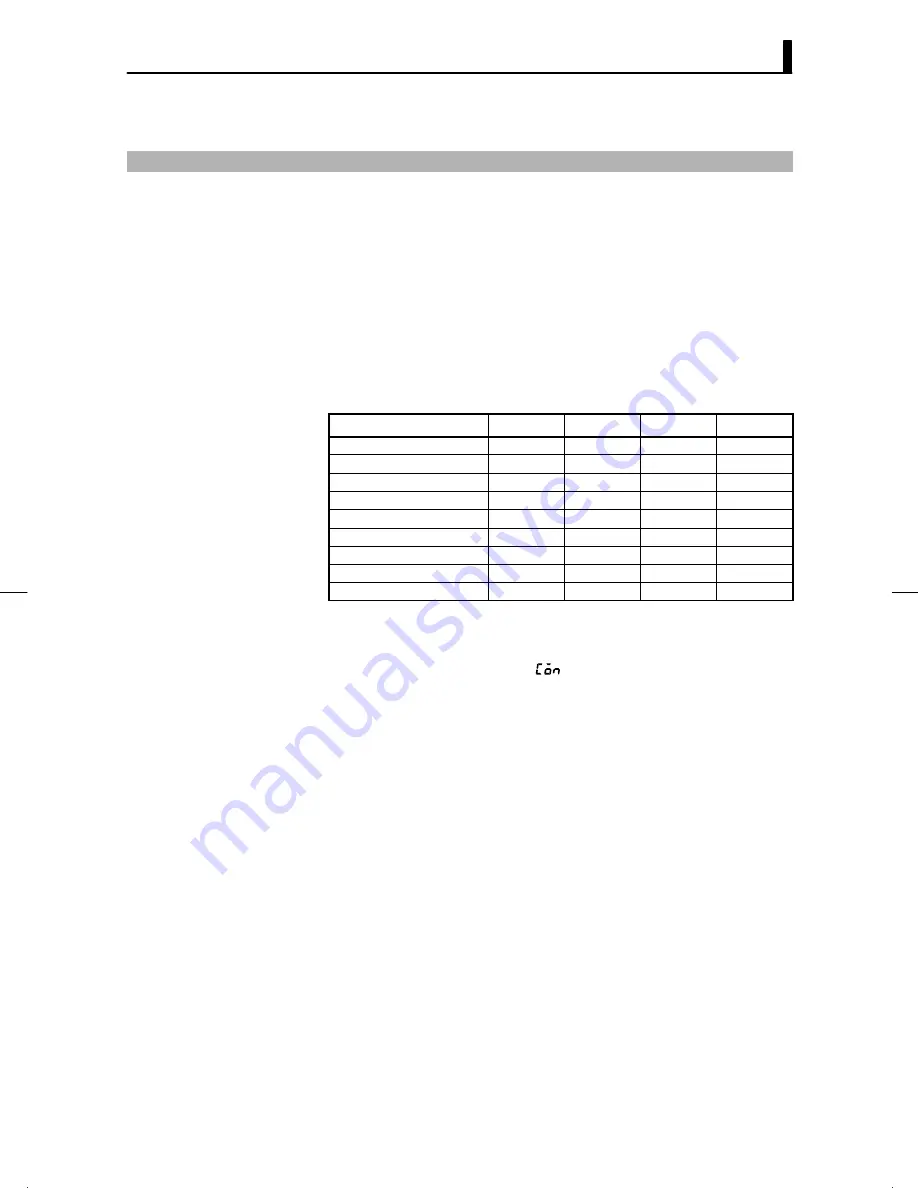
4.7 Setting Running Conditions
E5EK
4--19
4.7 Setting Running Conditions
•
You can select from one of the following operations at power ON:
Continue, Reset, Run, Manual
•
If you select “Continue,” operation is started from the state that was
active when power was interrupted.
•
If you select “Reset,” the controller is reset.
•
If you select “Run,” normal program operation is started.
•
If you select “Manual,” the controller enters the manual mode.
•
The following table shows the relationship between operation at pow-
er ON and the operation details that are stored to memory when a
power interruption occurs.
Continue
Reset
Run
Manual
Pattern No.
f
f
f
f
Step No.
f
-
-
f
Pattern elapsing time
f
-
-
f
Pattern execution count
f
-
-
f
Hold status
f
-
-
f
Auto/Manual
f
f
f
-
Run/Reset
f
-
-
f
MV at reset *1
f
-
-
f
Manual MV *2
f
f
f
f
*1 During auto mode at power interruption on a standard type controller
*2 During manual mode at power interruption on a standard type controller
•
Set the desired operation in the “operation at power ON” parameter
(expansion mode). Default is [
: Continue].
J
Operation at
power ON
Summary of Contents for E5EK
Page 1: ...User s Manual Cat No H089 E1 02 Digital Controller Programmable Type...
Page 24: ...CHAPTER 1 INTRODUCTION 1 14...
Page 36: ...CHAPTER 2 PREPARATIONS 2 12...
Page 162: ...CHAPTER 6 USING THE COMMUNICATIONS FUNCTION 6 20...
Page 176: ...CHAPTER 7 CALIBRATION 7 14...
Page 193: ...SETTING LIST A 11...