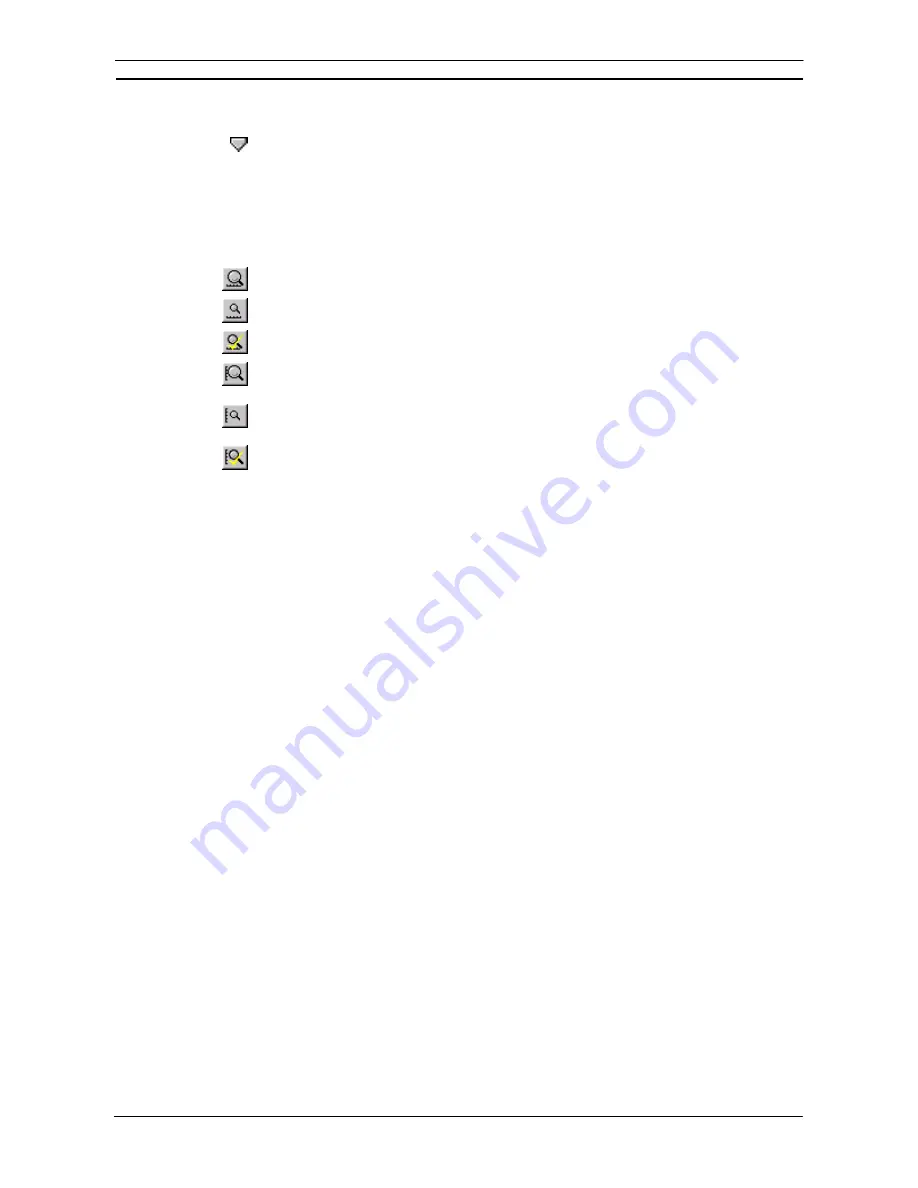
PART 2: CX-Server PLC Tools
OMRON
CHAPTER 5 – Data Trace/Time Chart Monitor Component
CX-Server PLC Tools_ Page 69
moved by placing the mouse cursor over the splitter bar and dragging it to its new position to show more or less of
the displayed numbers.
The slider position, used to analyze the data returned by the data trace, can be moved by placing
the mouse cursor over the graph slider and dragging it to its new position. Both sliders can be
moved together by selecting
Synchronise Cursors
from the
View
menu. When moving the
slider, it snaps to the sampled intervals. Moving and holding the slider left and right scrolls the
view window left and right.
The Data Trace/Time Chart Monitor component permits the zooming and scaling of the Data Trace/Time Chart
view. Use the following procedure to zoom and scale the Data Trace/Time Chart view.
Select the
Zoom In
button from the toolbar to zoom in on the word graph.
Select the
Zoom Out
button from the toolbar to zoom out from the word graph.
Select the
Restore Zoom
button from the toolbar to return the graph to the original view.
Select the
Scale In
button from the toolbar to zoom in on a particular graph against the vertical
axis.
Select the
Scale Out
button from the toolbar to zoom out from a particular graph against the
vertical axis.
Select the
Restore Scale
button from the toolbar to return the graph to the original scale.
This can be modified to switch between Histogram and Trend Graph when in Word Display Mode or to switch
between Outline and Block when in Bit Display Mode. Use the following procedure to switch display modes.
1, 2, 3…
1. Select
the
Word Display Mode
option or the
Bit Display Mode
option from the
Options
menu.
2. For Word Display Mode, select either
Histogram
or
Trend Graph.
3. For Bit Display Mode, select either
Block
or
Outline.
The Word values shown on the screen can be displayed in one of four formats:
♦
Binary;
♦
Decimal;
♦
Signed Decimal;
♦
Hexadecimal.
Use the following procedure to select a Bit value format.
1, 2, 3…
1. Select Word Value Format from the Options menu.
2. Select either Binary, Decimal, Signed Decimal or Hexadecimal.
The Bit values shown on the screen can be displayed in one of two formats:
♦
Boolean (1 or 0);
♦
Text (On or Off).
Use the following procedure to select a Bit value format.
1, 2, 3…
1. Select
Bit Value Format
from the
Options
menu.
2. Select
either
Boolean
or
Text
.
The Data Trace/Time Chart view can be toggled to display either PLC addresses or symbol names. Select the
Options
menu and then
Show Symbol Names
. If a symbol name is not available then the PLC address is shown.
The colours associated with the Data Trace/Time Chart view can be customised. Use the following procedure to
change the colours on the Data Trace/Time Chart view.
1, 2, 3…
1. Select
Colours
from the
Options
menu. The Trace Colour Selection dialog is displayed.
2. Select
a
Change
pushbutton associated with a colour to be applied to a Word or Bit
address. A standard Microsoft Windows Colour dialog is displayed.
3. Select a colour from the Colour dialog and click the
OK
pushbutton. Select the
Cancel
pushbutton from the Colour dialog to abort the operation.
4. If required, Select a
Change
pushbutton for another colour and repeat step 3.
Summary of Contents for CX-PROGRAMMER V9
Page 1: ...Cat No W446 E1 12 CX Programmer Ver 9 CXONE AL_C V4 AL_D V4 SYSMAC OPERATION MANUAL...
Page 2: ......
Page 3: ...SYSMAC CX Programmer Ver 9 CXONE AL C V4 AL D V4 Operation Manual Revised July 2010...
Page 4: ......
Page 6: ......
Page 32: ......
Page 33: ...PART 1 CX Programmer...
Page 34: ......
Page 91: ......
Page 111: ......
Page 191: ...PART 1 CX Programmer CHAPTER 4 Reference OMRON CX Programmer _Page 108...
Page 217: ......
Page 233: ......
Page 234: ...PART 2 CX Server PLC Tools...
Page 235: ......
Page 243: ......
Page 249: ......
Page 261: ...PART 2 CX Server PLC Tools CHAPTER 2 PLC Memory Component OMRON CX Server PLC Tools_Page 18...
Page 280: ......
Page 333: ......
Page 377: ......
Page 409: ......
Page 430: ......
Page 431: ...PART 3 CX Server Runtime...
Page 432: ......
Page 476: ......
Page 482: ......
Page 498: ......
Page 524: ......
Page 534: ......
Page 535: ......
Page 536: ......