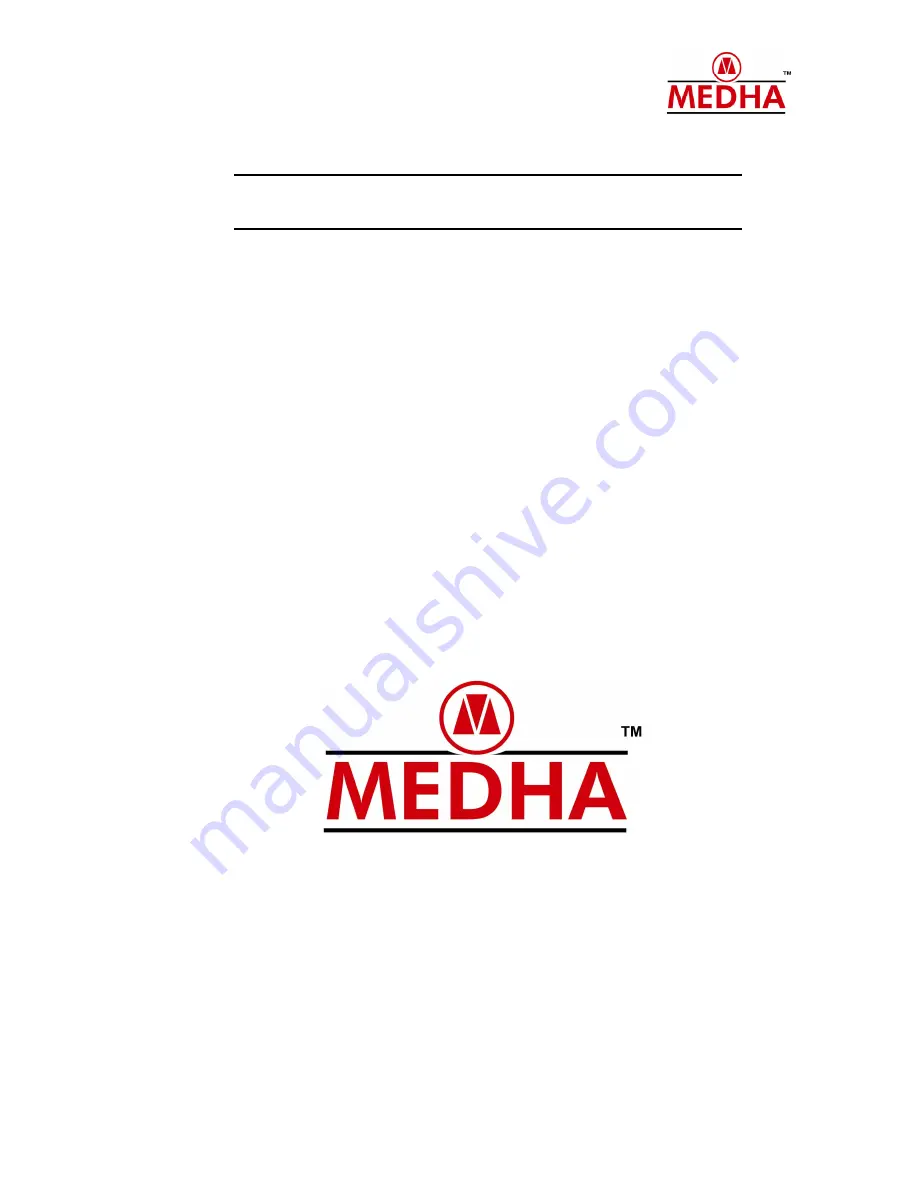
MEP 660 - Trouble shooting Manual
Doc No.: IM – 51
Rev.2.0
Print: October 2008
TROUBLE SHOOTING MANUAL
MICROPROCESSOR BASED
LOCOMOTIVE CONTROL SYSTEM
MEP 660
FOR DIESEL ELECTRIC LOCOMOTIVES
As Per
RDSO Specification No. MP.0.24.00.26 Rev. 0.3 November 2005
P- 4 / 5 B, I.D.A NACHARAM
HYDERABAD - 500 076
Ph. No. 040- 2717 3990 Fax. 040 2717 4908
Email: [email protected]
URL: www.medhaindia.com