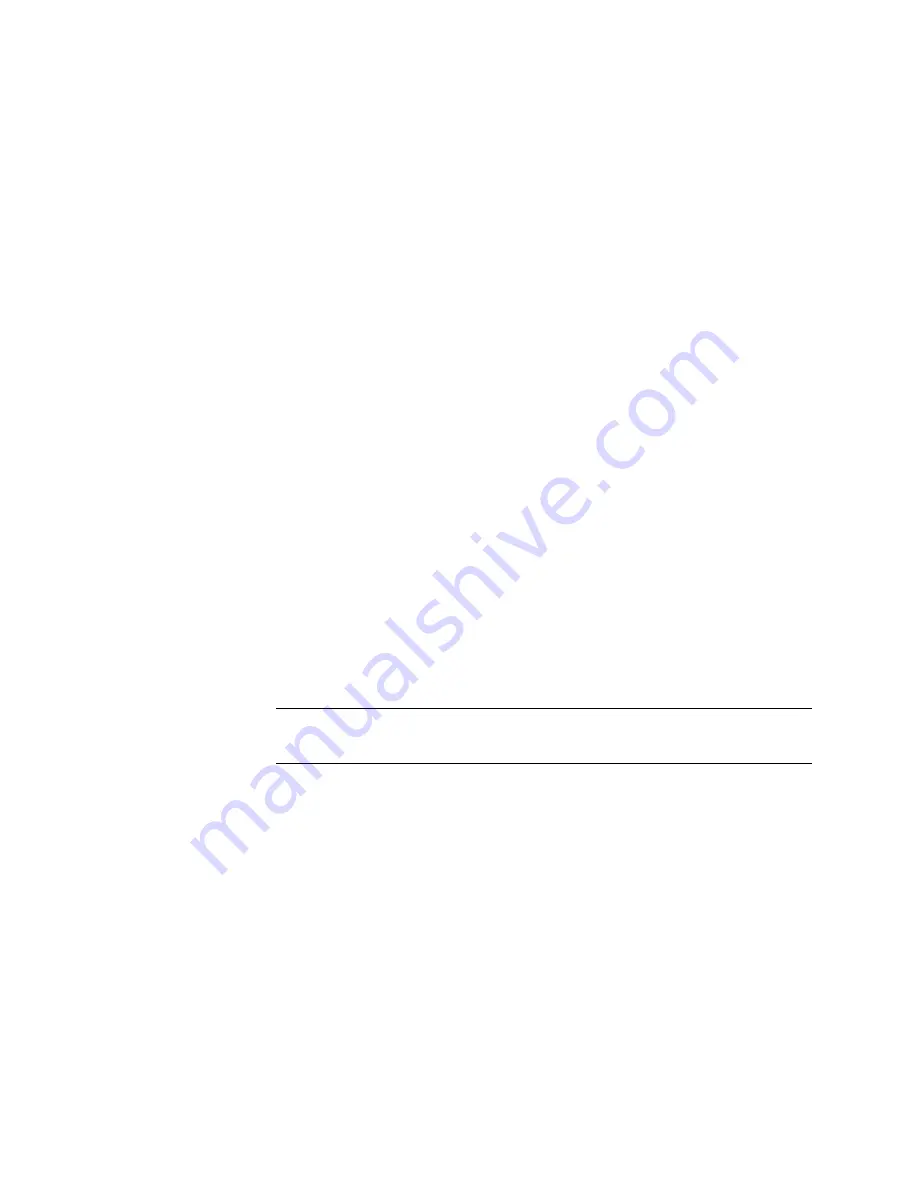
User Manual
Appendix D
GFK-1742F
Jan 2020
Tuning Digital and Analog Servo Systems
434
Advanced Tuning Parameters: The advanced tuning parameter section contains
many parameters that are used to configure torque mode to operate correctly. The
advanced tuning parameters are discussed in detail in Chapter 4. For a complete
reference consult this chapter. The tuning parameters of interest are as follows:
Tuning Parameter 6: Sets the encoder resolution parameter. The parameter is only
used in torque mode. For correct torque mode operation, this value must be set to
the number of quadrature encoder counts generated by the motor feedback device
per revolution. The user can determine the value from the feedback device
specification. As a double check, the user may wish to connect the feedback device
to the DSM and manual rotate the motor shaft one revolution. The reading on the
DSM %AI data for actual position should closely match (variations are caused by the
accuracy of manual turning shaft one revolution) the value placed in this parameter.
The allowed range is 100-32767 counts/revolution. The default value is 4096 counts
per revolution
Tuning Parameter 7: Sets the velocity regulator proportional gain. The parameter is
only used in torque mode. The proportional gain is multiplied by velocity error
(velocity command - velocity feedback) to generate the portion of the torque
command due to the proportional term. Correctly setting this value will determine
how well the velocity regulator performs in the control system. The following
sections will discuss how to set this value.
Tuning Parameter 8: Sets the velocity regulator integral gain. The parameter is only
used in torque mode The integral gain is the term multiplied by the area of the
velocity error (velocity command - velocity feedback) to generate the portion of the
torque command due to the integral term. Correctly setting this value will
determine how well the velocity regulator performs in the control system. The
following sections will discuss how to set this value.
Note:
For proper servo operation, the Configuration entry for Encoder Resolution MUST be set
to the correct value for the servo amplifier/motor set. If this value is not set correctly
instabilities can result.
5.
Turn on the %Q Enable Drive bit and place the command code for Force Servo
Velocity equal to 0 in the %AQ table. Confirm that the servo amplifier is enabled (the
motor should exhibit holding torque). If the motor moves, adjust the amplifier until
the motor stops moving.
6.
Make sure that the motor shaft is not connected to the load when first performing
the following operation. The user needs to now verify basic control functionality.
Send the command code for Force Servo Velocity equal to 10 RPM. Confirm that the
motor moves in the desired POSITIVE direction (based on the Axis Direction
configuration parameter setting) and the Actual Velocity reported in the DSM314
%AI table is POSITIVE. If the motor moves in the wrong direction, consult the servo
amplifier manufacturer's instructions for corrective action. The Axis Direction
parameter in the Configuration Software can also be used to swap the positive and
negative axis directions. If the motor moves in the POSITIVE direction but the
DSM314 reports that Actual Velocity is NEGATIVE, then the encoder channel A and
channel B inputs must be swapped.