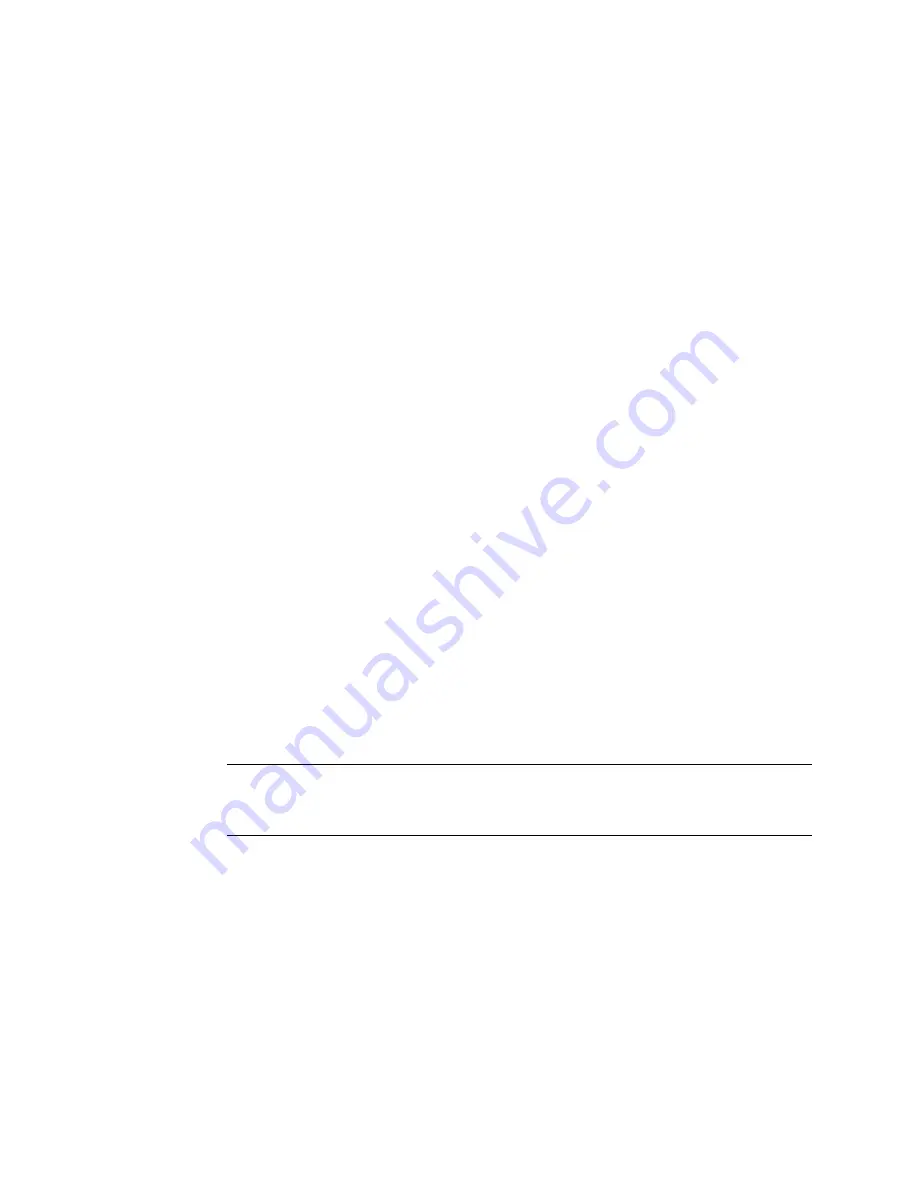
User Manual
Appendix D
GFK-1742F
Jan 2020
Tuning Digital and Analog Servo Systems
423
2.
Connect an oscilloscope to the analog outputs for Motor Velocity feedback and
Torque Command. See Section 4.25 of Chapter 5 for analog output configuration
instructions.
3.
Set the Velocity Loop Gain to zero. This is a conservative approach. If the application
is known to not have resonant frequencies from zero to approximately 250 Hz, you
can start with a higher value, but do not exceed the value calculated in equation 1 at
this point.
4.
Generate a velocity command step change. At this point the step change should be
relatively small compared to the full speed of the machine. Ten to 20 % of the rated
machine speed is a good start.
5.
Observe the Motor Velocity and Torque Command on the oscilloscope. The
objective is to obtain a critically damped velocity loop response. Pay particular
attention to any oscillations that are occurring in the velocity feedback signal.
6.
Increase the Velocity Loop Gain in small steps and repeat 4 and 5 until instability in
the Motor Velocity feedback signal is observed. Once this point is reached, decrease
the Velocity Loop Gain by at least 15 %. As a general rule, the lower the Velocity Loop
Gain value that meets the system requirements the more robust the control. You
should carefully observe the velocity feedback signal. In some applications, running
the Velocity Loop Gain high enough to create instability can cause machine damage.
If in doubt, adjust the Velocity Loop Gain to be no greater than the value calculated
in equation 1. If oscillations are observed in the Motor Velocity feedback signal prior
to this point, decrease the Velocity Loop Gain and continue with step 7 below.
7.
The velocity loop is tuned at this point. However, the robustness of the loop must
be checked. To perform this test, introduce velocity command steps in increments
of 20% Rated Machine Speed, 40% Rated Machine Speed, 60% Rated Machine Speed,
80% Machine Rated Speed, and 100% Rated Machine Speed. Observe the Motor
Velocity and Torque Command signals for any instability. If an instability or
resonance is observed, reduce the Velocity Loop Gain and repeat the test.
Note:
For Digital servos, the %AQ Force Analog Output command can provide Torque Command or
Commanded Motor Velocity. (Velocity = 750 rpm/volt and %TqCmd = (100/1.111111 Volt)*X Volt
or Torque Cmd = 100% Torque Command = 1.111 Volts, 100%TqCmd = MaxCur Amplifier. For
instance: Beta 0.5 MaxCurAmp = 12 amps => 1.111111 volt = 12 amps.