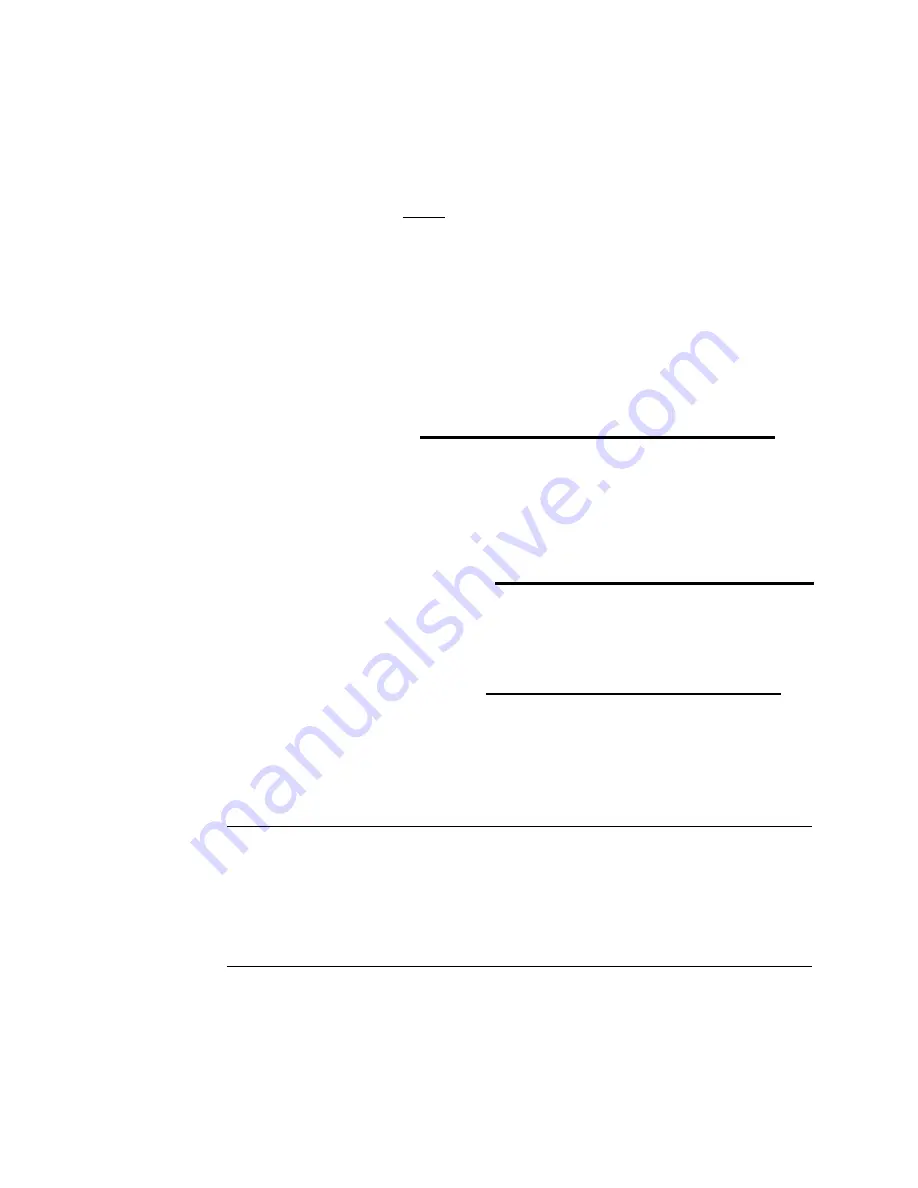
User Manual
Chapter 4
GFK-1742F
Jan 2020
Configuration
125
6.03 Position Error Limit. Position Error Limit (User Units). The Position Error Limit is the
maximum Position Error (Commanded Position - Actual Position) allowed when the
DSM314 is controlling a servo. Position Error Limit should normally be set to a value
10% to 20% higher than the highest Position Error encountered under normal servo
operation. Default: 60000.
The Position Error Limit range formula is:
256 x (user units/counts) Position Error Limit 60,000 x (user units/counts)
If Velocity Feedforward is not used, Position Error Limit can be set to a value
approximately 20% higher than the Position Error required to produce a 4000-rpm
command. The Position Error (User Units) required to produce a 4000-rpm
command with 0% Velocity Feed forward is:
Position Error (user units) = Position Loop Time Constant (ms) x Servo Velocity @ 4000 rpm
(user units/sec)
1000
Example
The user units counts ratio is 2:1 and the Position Loop Time Constant is 50 ms.
Step 1:
Calculate servo velocity at 4000 rpm =
(2 user units/count) x (8192 counts/rev) x (4000 revs/minute)
(60 seconds/minute)
= 1,092,266 user units/second
Step 2:
Calculate Position Error at 4000 rpm = (50 milliseconds) x (1,092,266 user units/second)
1000 milliseconds/second
= 54613 user units
If Velocity Feedforward is used to reduce the following error, a smaller error limit
value can be used, but in general, the error limit value should be 10% - 20% higher
than the largest expected following error.
Note:
An Out of Sync error will occur and cause a fast stop if the Position Error Limit Value is exceeded
by more than 1000 counts. The DSM314 attempts to prevent an Out of Sync error by temporarily
halting the internal command generator whenever position error exceeds the Position Error Limit.
Halting the command generator allows the position feedback to catch up and reduce position
error below the error limit value.
If the feedback does not catch up and the position error continues to grow, the Out of Sync
condition will occur. Possible causes are:
1.
Erroneous feedback wiring
2.
Feedback device coupling slippage
3.
Servo drives failure.
4.
Mechanically forcing the motor/encoder shaft past the servo torque
capability.