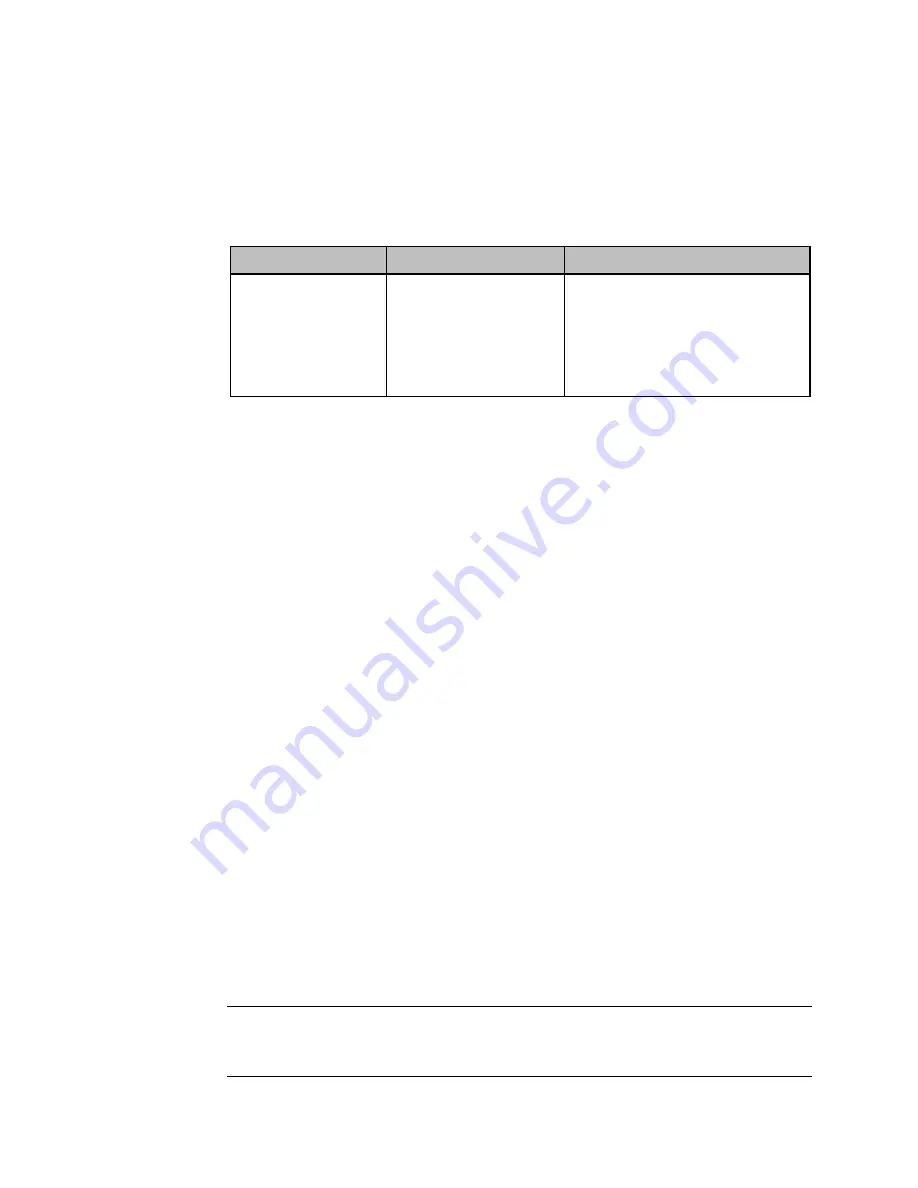
User Manual
Appendix A
GFK-1742F
Jan 2020
Error Reporting
364
Appendix A:
Error Reporting
A-1
DSM314 Error Codes
The DSM314 reports error codes in these %AI table locations:
%AI Table Location
Data Reported
Usage
00
Module Status Code
Errors not related to a specific axis
04
Axis 1 Error Code
Errors related to Axis 1
24
Axis 2 Error Code
Errors related to Axis 2
44
Axis 3 Error Code
Errors related to Axis 3
64
Axis 4 Error Code
Errors related to Axis 4
Each error code is a hexadecimal word that describes the error indicated when the Module
Error Present %I status bit is set.
A-1.1
Module Status Code Word
The Module Status Code %AI status word reports the following two categories of errors:
•
Module errors that are not related to a specific axis. Examples of such errors would
be a self-test detected hardware failure or a request to run an empty or invalid
program. A new Module Status Code will not replace a previous Module Status Code
unless the new Module Status Code has Fast Stop or System Error priority. These can
be cleared with the %Q Clear Error bit.
•
System Status Errors. These are of the format Dxxx, Exxx, and Fxxx. If one of these
codes is present, the module will not operate and the %Q Clear Error bit will not clear
the error. See the section “System Status Errors” later in this appendix for details.
A-1.2
Axis Error Code Words
All axis-specific motion related errors are reported in the proper Axis Error Code %AI status
word. Whenever the Module Error Present %I status bit is set, all error words (including
Module Status Code) should be checked for a reported error. A new Axis Error Code will
replace a previous Axis Error Code if it has equal or higher priority (Warning, Normal Stop,
Fast Stop) compared to the previous Axis Error Code.
Error codes that stop the axis will clear the Axis OK %I bit for that axis. User logic that sends
%Q or %AQ commands to an axis should normally be qualified by the applicable %I Axis OK
bit. If Axis OK is off, the axis will not respond to any %Q bit or %AQ commands other than
Clear Error or Load Parameter. The %Q Clear Error bit will always clear the Axis Error Code;
however, if the condition that caused the error still exists, the error will immediately be
reported again.
Note:
The STAT LED on the faceplate of the module flashes slow (four times/second) for Status Only
errors and fast (eight times/second) for errors that cause the servo to stop. In the case of a fatal
hardware error being detected at power-up, the STAT LED will flash an error code, which should
be reported to Emerson. See
“LED Indicators” later in this chapter for more details
.