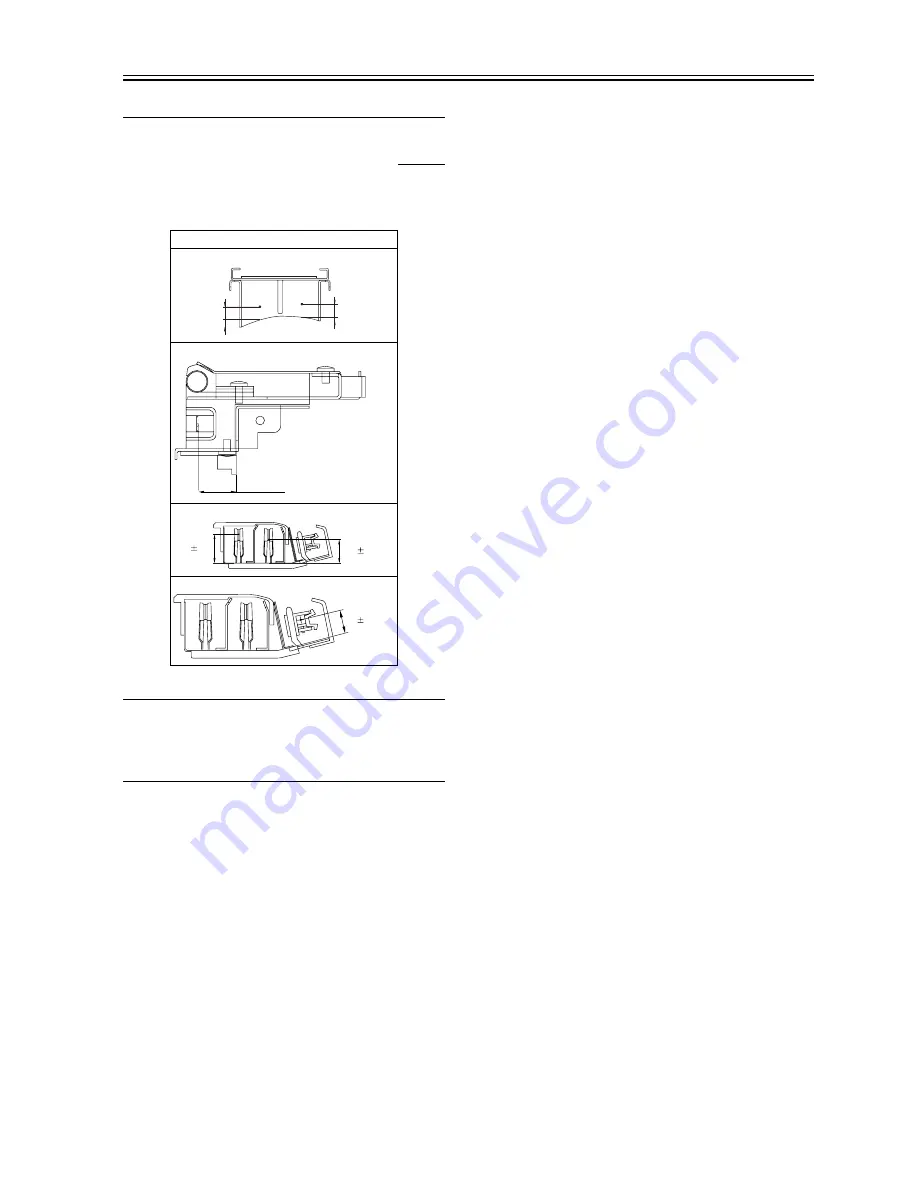
Chapter 14
14-31
14.5 Image Formation System
14.5.1 Adjusting the Height of the Charging Wire
0008-8359
iR105i/iR105+ / iR9070 / iR85+ / iR8070
T-14-3
MEMO:
The height (position) of the primary and transfer charging wires may be
adjusted by turning the screw found at the rear of the charging assembly.
A full turn of the screw changes the position of the charging wire by
about 0.7 mm.
Height of charging wire
Primary
Pre-transfer
Separation
Transfer
7.5
- 0mm
+3mm
7.5
- 0mm
+3mm
13.6 ±0.3mm
No height adjusting
mechanism
17.0
0.2mm
15.5
0.2mm
9.0
0.2mm
Summary of Contents for ImageRunner iR8500 Series
Page 1: ...Apr 5 2005 Service Manual iR8500 Series ...
Page 2: ......
Page 6: ......
Page 32: ...Contents ...
Page 33: ...Chapter 1 Introduction ...
Page 34: ......
Page 98: ......
Page 99: ...Chapter 2 Installation ...
Page 100: ......
Page 180: ...Chapter 2 2 78 F 2 272 2 1 1 3 ...
Page 181: ...Chapter 3 Basic Operation ...
Page 182: ......
Page 184: ......
Page 207: ...Chapter 4 Main Controller ...
Page 208: ......
Page 245: ...Chapter 4 4 35 F 4 72 1 2 ...
Page 246: ......
Page 247: ...Chapter 5 Original Exposure System ...
Page 248: ......
Page 252: ......
Page 306: ......
Page 307: ...Chapter 6 Image Processing System ...
Page 308: ......
Page 310: ......
Page 319: ...Chapter 7 Laser Exposure ...
Page 320: ......
Page 322: ......
Page 335: ...Chapter 8 Image Formation ...
Page 336: ......
Page 340: ......
Page 399: ...Chapter 9 Pickup Feeding System ...
Page 400: ......
Page 404: ......
Page 482: ......
Page 483: ...Chapter 10 Fixing System ...
Page 484: ......
Page 524: ......
Page 525: ...Chapter 11 External and Controls ...
Page 526: ......
Page 530: ......
Page 583: ...Chapter 12 MEAP ...
Page 584: ......
Page 586: ......
Page 589: ...Chapter 13 Maintenance and Inspection ...
Page 590: ......
Page 592: ......
Page 610: ...Chapter 13 13 18 F 13 17 1 2 3 ...
Page 648: ......
Page 649: ...Chapter 14 Standards and Adjustments ...
Page 650: ......
Page 654: ......
Page 723: ...Chapter 15 Correcting Faulty Images ...
Page 724: ......
Page 728: ......
Page 792: ......
Page 793: ...Chapter 16 Self Diagnosis ...
Page 794: ......
Page 796: ......
Page 841: ...Chapter 17 Service Mode ...
Page 842: ......
Page 1076: ......
Page 1077: ...Chapter 18 Upgrading ...
Page 1078: ......
Page 1080: ......
Page 1108: ...Chapter 18 18 28 F 18 45 3 Click Start F 18 46 4 Click Save F 18 47 5 Click OK ...
Page 1111: ...Chapter 19 Service Tools ...
Page 1112: ......
Page 1114: ......
Page 1120: ......
Page 1121: ...Apr 5 2005 ...
Page 1122: ......