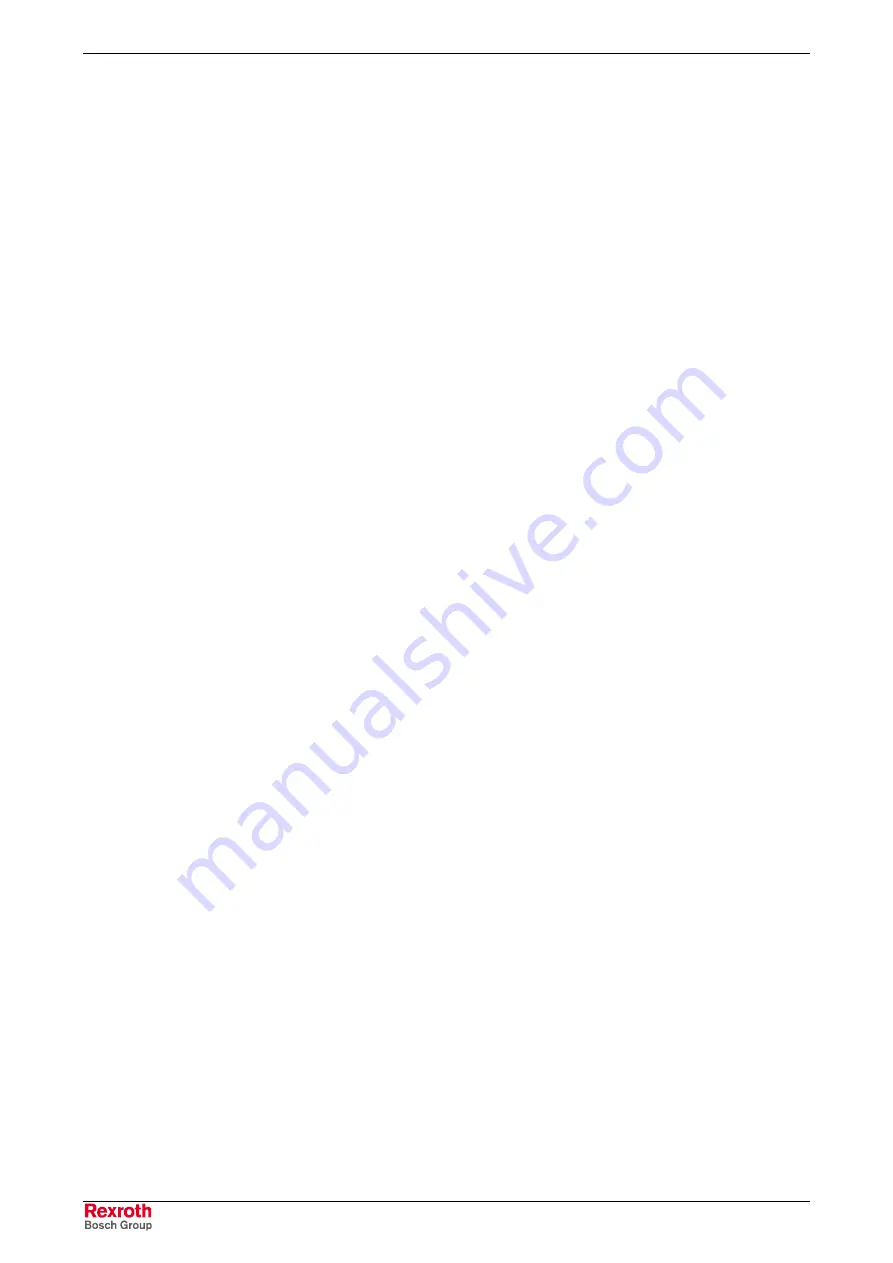
8-26
Functions
ECODRIVE03-FL*-04VRS
DOK-ECODR3-FL*-04VRS**-FK01-EN-P
Synchronization by Precise Positioning
This function is for synchronizing the slave axis for a material sequence
that is moving in one direction. The motion of the material sequence is
detected with a relative master encoder. Using the LAL and LAR
commands, the synchronization location on the material can be defined.
In the LAL command, the distance between two synchronization locations
is set. When the function is turned on using the CSY command, the
position of the slave axis is defined as the synchronization location and,
therefore, as the start position (home position) for the slave axis. Before
each synchronization operation, the slave axis must be in this home
position. In Variable V113, the actual distance between the next or actual
processing location and the home position is displayed.
Synchronization is executed with a cam function. This cam can be
selected using the CMM command. The acceleration distance is set in the
CLG command, or, if this does not occur, it is set as the default value.
Acceleration Distance > Parameter A106
2
/ (2 x Parameter A109)
•
This function can be turned on and off using the CSY command.
•
During the synchronization phase, a position offset can be set using
the POI/PSI commands. The indicated velocity is therefore limited, so
that the maximum velocity (Parameter A106) is not exceeded.
•
With the POA/PSA commands, the synchronization function is
deactivated and it is positioned to the set absolute position using the
set velocity. If a velocity of 0 is set in the POA/PSA command,
positioning is accomplished using the retrieved current master value.
•
Immediate Stop is active. The axis stops using a ramp. The function is
closed.
•
When the operating mode is switched from Automatic
Å
Manual,
decelerative synchronization, using the current deceleration value
(Parameter A109 or ACC command), and deactivation of this function
occurs.
•
The interrupt function is not activated.
•
Calling an Interrupt Vector program is possible. However, because of
the program sequence for this function, caution is advised!
•
With the system synchronized, if the master position is less than the
start position because of a reversal of the direction of the master, the
axis remains synchronized. However, the position value may be less
than the "Min. Position Limit"!
•
Behavior during an E-Stop:
The axis is no longer synchronized. The equipment is stopped using
"Best possible deceleration.“
•
Current reduction (possible using the MOM command)
Summary of Contents for Rexroth OptiFeed-FS EcoDrive 03 FLP04VRS
Page 18: ...XVI Table of Contents ECODRIVE03 FL 04VRS DOK ECODR3 FL 04VRS FK01 EN P ...
Page 348: ...11 18 Command Communications ECODRIVE03 FL 04VRS DOK ECODR3 FL 04VRS FK01 EN P Notes ...
Page 418: ...13 4 Connectors ECODRIVE03 FL 04VRS DOK ECODR3 FL 04VRS FK01 EN P Notes ...
Page 470: ...16 4 IDS Accessories ECODRIVE03 FL 04VRS DOK ECODR3 FL 04VRS FK01 EN P Notes ...
Page 489: ......