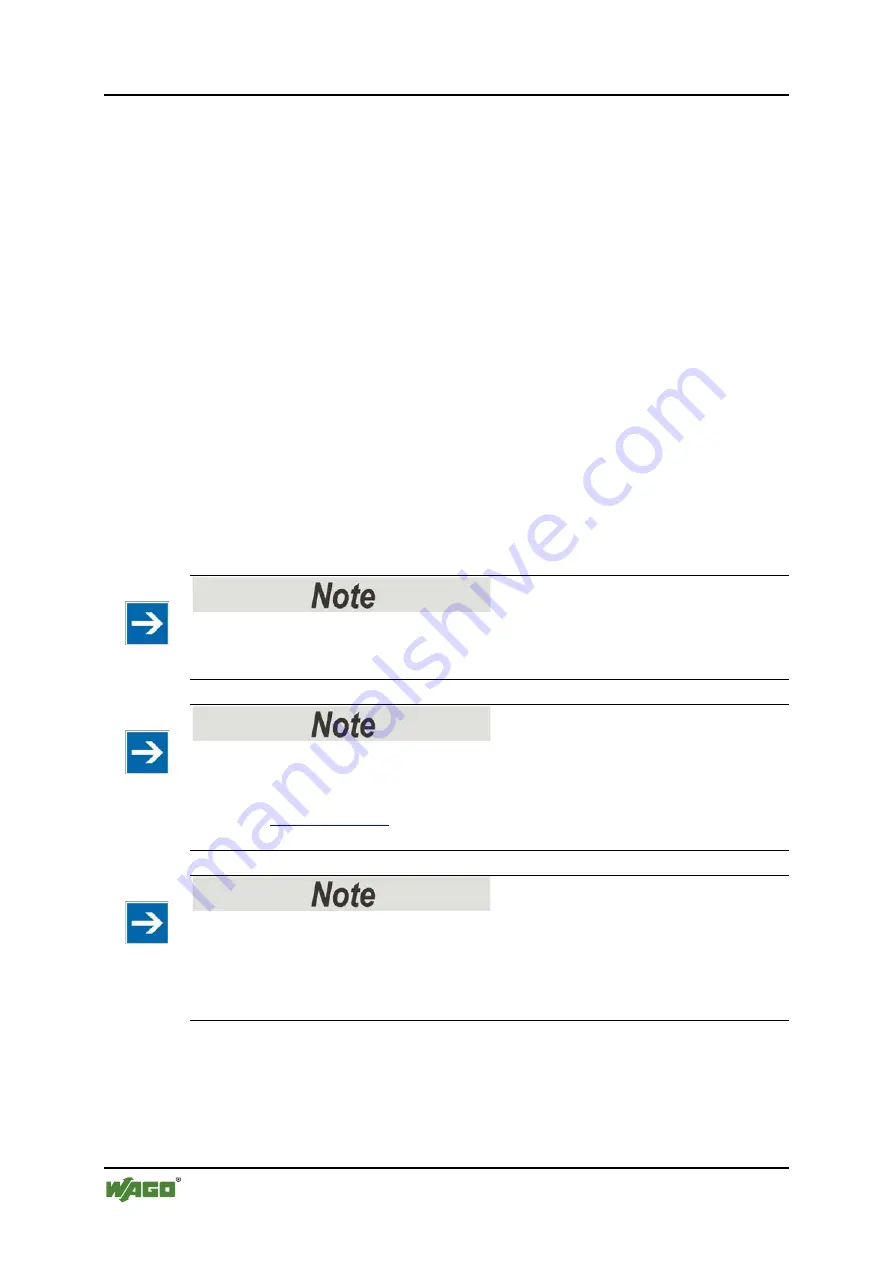
118 Commissioning
WAGO-I/O-SYSTEM 750
750-666/000-003 4FDI/2FDO 24V/10A PROFIsafe V2 iPar
Manual
Version 1.2.0, valid from HW/SW Version 01/01
7.5
Programming the Safe PLC
To configure the safe PLC using the PROFIsafe I/O module 750-666/000-003, the
following requirements must be met:
• Use of a suitable safe PLC (e.g., iPar server support)
• Use of a suitable programming and configuration environment
• Selection of a WAGO fieldbus coupler (PROFIBUS, PROFINET)
• Use of the current WAGO device description file (GSD, GSDML)
After selecting a suitable safe PLC, add the required bus system (PROFIBUS or
PROFINET) to the hardware configuration environment and configure it
accordingly (fieldbus parameters, addresses, names, etc.).
Then select the PROFIBUS or PROFINET fieldbus coupler from the device
catalog and connect it to the respective bus system.
The PROFIsafe I/O module can be operated with or without iPar server
functionality.
Observe the manufacturer documentation off the safe PLC!
The exact programming procedure is available in the manufacturer documentation
of the safe PLC.
Use the application notes from WAGO!
An overview for using PROFIsafe I/O modules in combination with a safe PLC is
summarized in an application note. This application note is available on the
Internet at
in the area "Service > Documentation > Application
Notes..."
Observe dependencies!
When creating safety programs, take into account the dependencies between PLC
cycle time, call interval of the safety program, expected response times of the
safety program and adjustable monitoring times. Details are available in the
respective manufacturer documentation.
7.5.1
PROFIsafe I/O Module without iPar Functionality
To use the PROFIsafe I/O module without iPar server functional, select the
PROFIsafe I/O module “75x-666 4FDI/2FDO 24V/10A DC” from the device