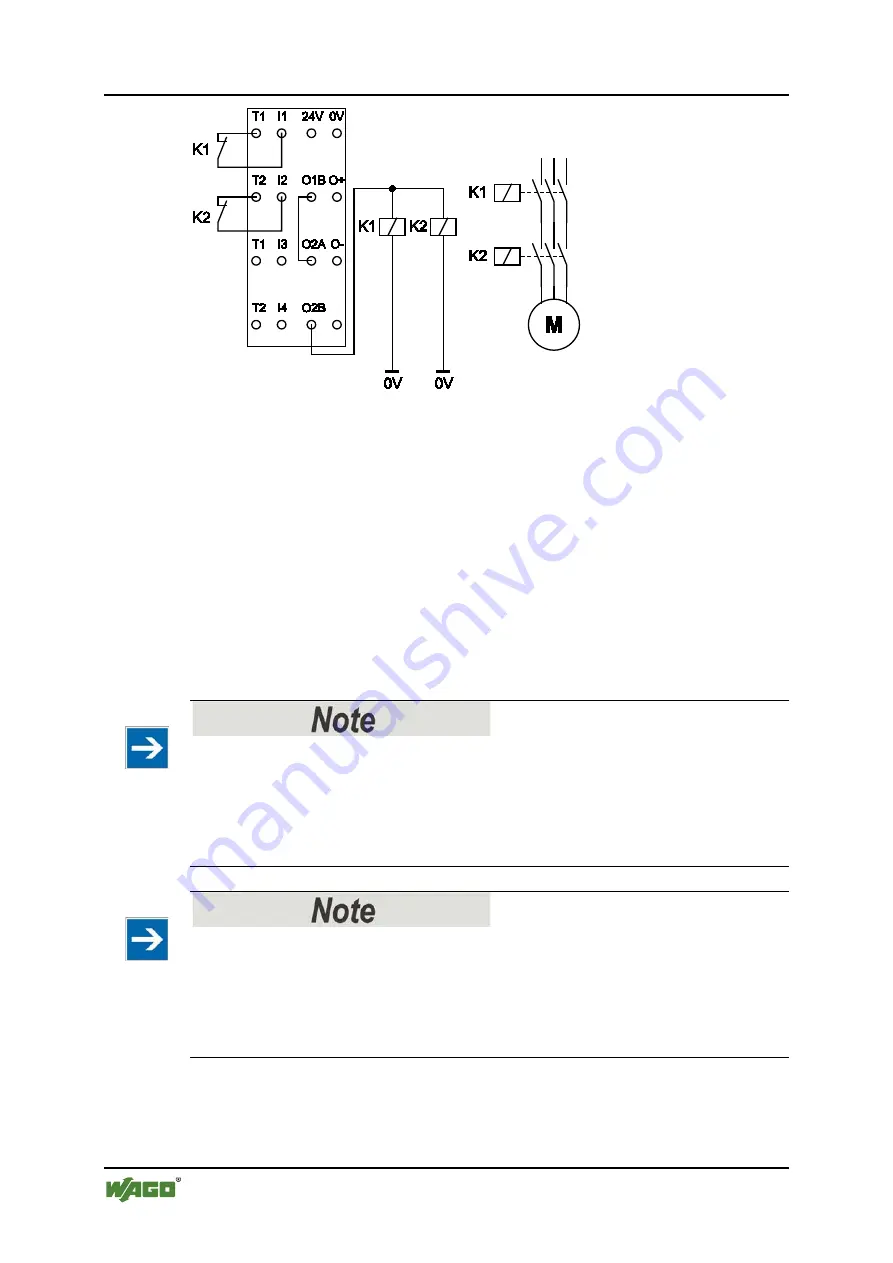
72
Connect Devices
WAGO-I/O-SYSTEM 750
750-666/000-003 4FDI/2FDO 24V/10A PROFIsafe V2 iPar
Manual
Version 1.2.0, valid from HW/SW Version 01/01
Figure 33: Connection 1 x motor, output configuration H-Side/H-Side 1, two-channel
In the output configuration "H-Side/H-Side 1", the PROFIsafe I/O module
switches both semiconductor switches ON or OFF at the same time using the bit 0
of the output process image.
You must disable line break detection by setting the
Line break detection
parameter to "inactive". For more information about configuring the PROFIsafe
I/O module, read section "Parameterization of the PROFIsafe I/O Module with the
WAGO Parameterization Tool".
You can achieve a risk reduction of SIL3/Cat.4/PL e, for example, by reading
back the switching states of the power jumper contacts from positively driven
contacts of a relay.
Line break detection on the digital output
Monitoring of
line breaks
only works between connections O1B and O2A. If you
set the
Output Configuration
parameter to the value "H-Side/L-Side 1", then
you have to set the value of the
Line break detection
to the value "inactive".
Line break detection is not safety related and cannot be part of the safety function
under any circumstances.
Use the same value for the output tolerance time of output O1 and O2!
If the
Output Configuration
parameter is set to "H-Side/L-Side 1", the values of
the
Output tolerance time
for both outputs O1 and O2 must be set to the same
value. This is checked by the PROFIsafe I/O module during the parameterization
procedure and a suggested correction is indicated by the PROFIsafe I/O module in
the WAGO parameterization tool in case of deviation.