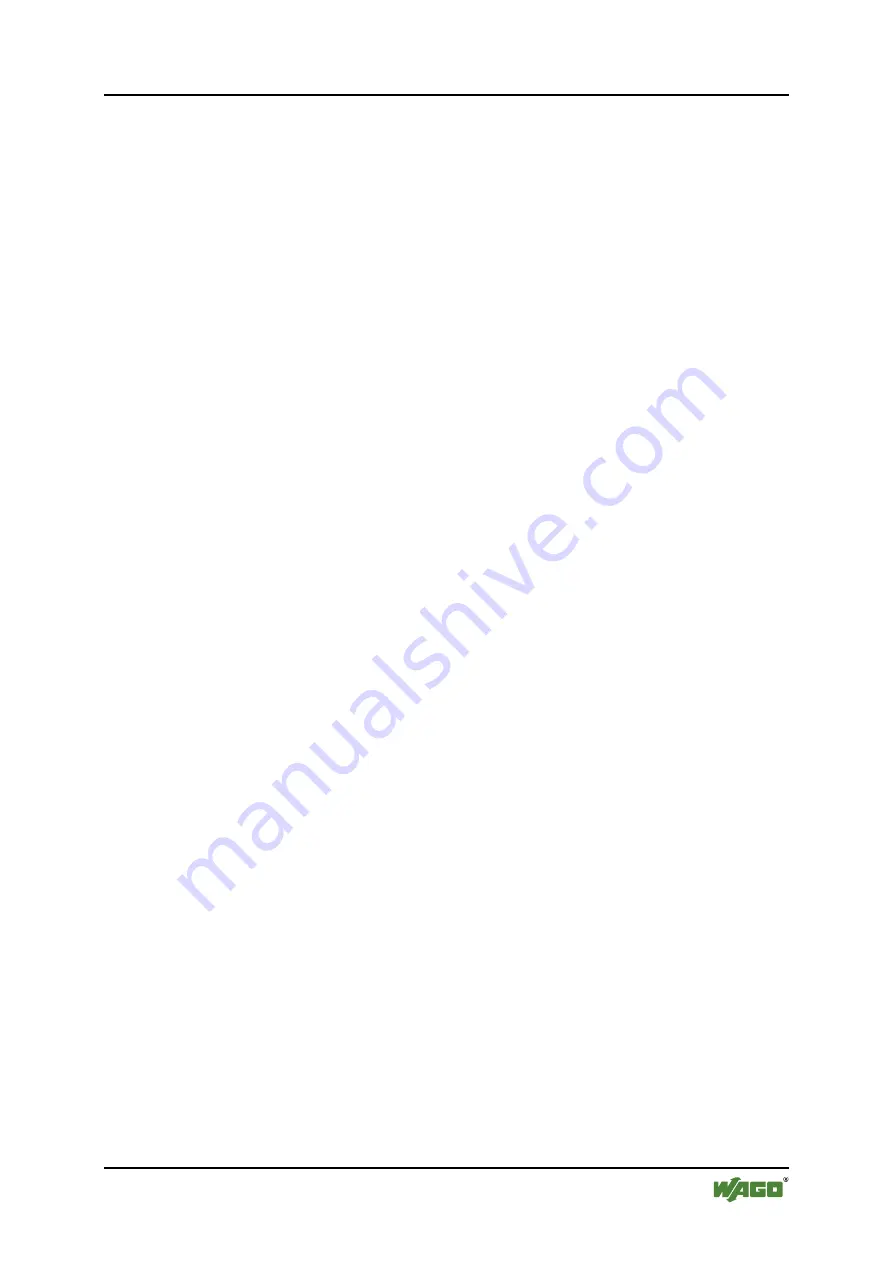
WAGO-I/O-SYSTEM 750
Commissioning 119
750-666/000-003 4FDI/2FDO 24V/10A PROFIsafe V2 iPar
Manual
Version 1.2.0, valid from HW/SW Version 01/01
catalog and add it to the fieldbus node. Then set the F parameters of the
PROFIsafe I/O module in the hardware configuration environment. Then
recompile the configuration and transfer it so the safe PLC.
Then configure the PROFIsafe I/O module using the WAGO parameterization
tool as described in the section "Parameterization of the PROFIsafe I/O Module
with the WAGO Parameterization Tool".
After you have configured the PROFIsafe I/O module, create the required call
structure for the safety program. The required system calls and system settings to
activate the safety program are added to the project.
Based on your requirements, then create the safety program that contains the basic
functions for PROFIsafe subscribers (e.g., reintegration).
After compiling the safety program, you have to check the assignment of
PROFIsafe subscribers to the respective run-time group. Then transfer the entire
project to the safe PLC.
You have to observe the listed required workflows within the respective
manufacture documentation, as well as check and document all safety functions.
7.5.2
PROFIsafe I/O Module with iPar Functionality and iPar
Server
To use the PROFIsafe I/O module with iPar server functional, select the I/O
module with the “75x-666 4FDI/2FDO iPar-Server” designation from the device
catalog and add it to the fieldbus node. You must first set the F_iPar_CRC in the
F parameters to 0 in the hardware configuration environment, so that the
PROFIsafe I/O module switches to test mode. Then recompile the configuration
and transfer it so the safe PLC.
After you have configured the PROFIsafe I/O module, create the required call
structure for the safety program. The required system calls and system settings to
activate the safety program are added to the project. It is important that the data
block for storing the iParameters (iPar server) is added for each iPar server-
capable I/O module.
After compiling the safety program, you have to check the assignment of
PROFIsafe subscribers to the respective run-time group. Then transfer the entire
project to the safe PLC.
After the safe PLC starts, the PROFIsafe I/O module switches to test mode. In this
mode, the safety-related functions of the PROFIsafe I/O module are passivated.
Then configure the PROFIsafe I/O module using the WAGO parameterization
tool. For more information, read the section "Parameterization of the PROFIsafe
I/O Module with the WAGO Parameterization Tool". The WAGO
parameterization tool displays the iPar_CRC. You have to note this for the next
step (e.g., copy to the clipboard).