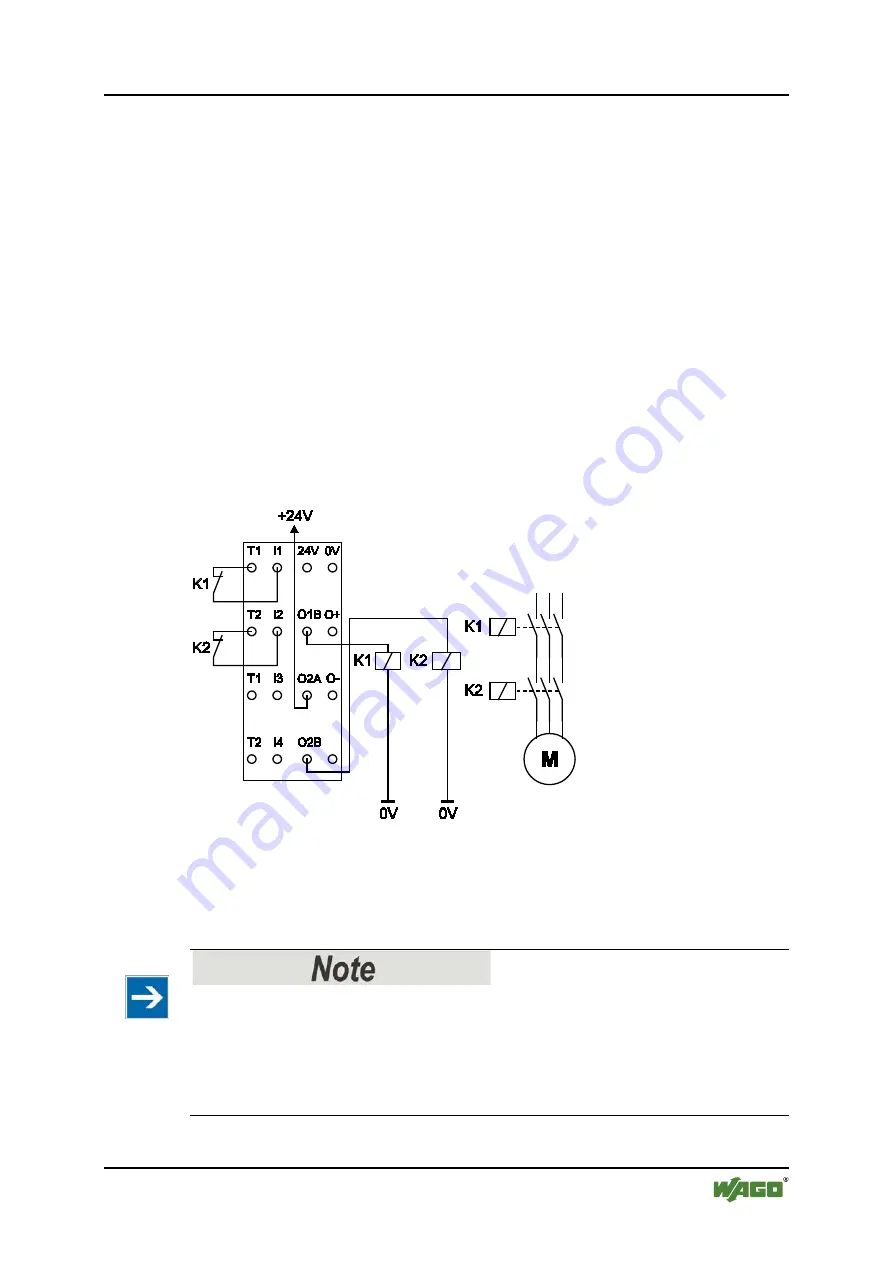
WAGO-I/O-SYSTEM 750
Connect Devices
75
750-666/000-003 4FDI/2FDO 24V/10A PROFIsafe V2 iPar
Manual
Version 1.2.0, valid from HW/SW Version 01/01
In this output configuration, the PROFIsafe I/O module switches both
semiconductor switches ON or OFF separately using the bit 0 and bit 1 of the
output process image. Bit 0 switches the load connected to connection O1B to the
0V potential. Bit 1 switches the load connected to connection O2B to the 0V
potential.
You can connect a contactor to a digital power output and connect a motor single-
channel using normally open contacts of the contactor.
With single-channel use, shutdown must be ensured by the standard control in the
event of an error. This can be achieved by integrating a 2nd disconnection faculty
(e.g., a line contactor K0) in the safety application.
You can achieve a risk reduction of SIL2/Cat.2/PL d, for example, by reading
back the switching states of the power jumper contacts from positively driven
contacts of a relay during single-channel use of digital outputs O1 - O2.
Please note that according to EN ISO 13849-1, the request rate of the safety
function must be ≤ 1/100 of the test rate during single-channel use of the digital
outputs.
Figure 35: Connection 1 x motor, output configuration H-Side/H-Side 2, two-channel
You can achieve a risk reduction of SIL3/Cat.4/PL e, for example, by reading
back the switching states of the power jumper contacts from positively driven
contacts of a relay during two-channel use of digital outputs O1 - O2.
Line break detection on the digital output
Monitoring of
line breaks
only works between connections O1B and O2A. If you
set the
Output Configuration
parameter to the value "H-Side/L-Side 2", then
you have to set the value of the
Line break detection
to the value "inactive".
Line break detection is not safety related and cannot be part of the safety function
under any circumstances.