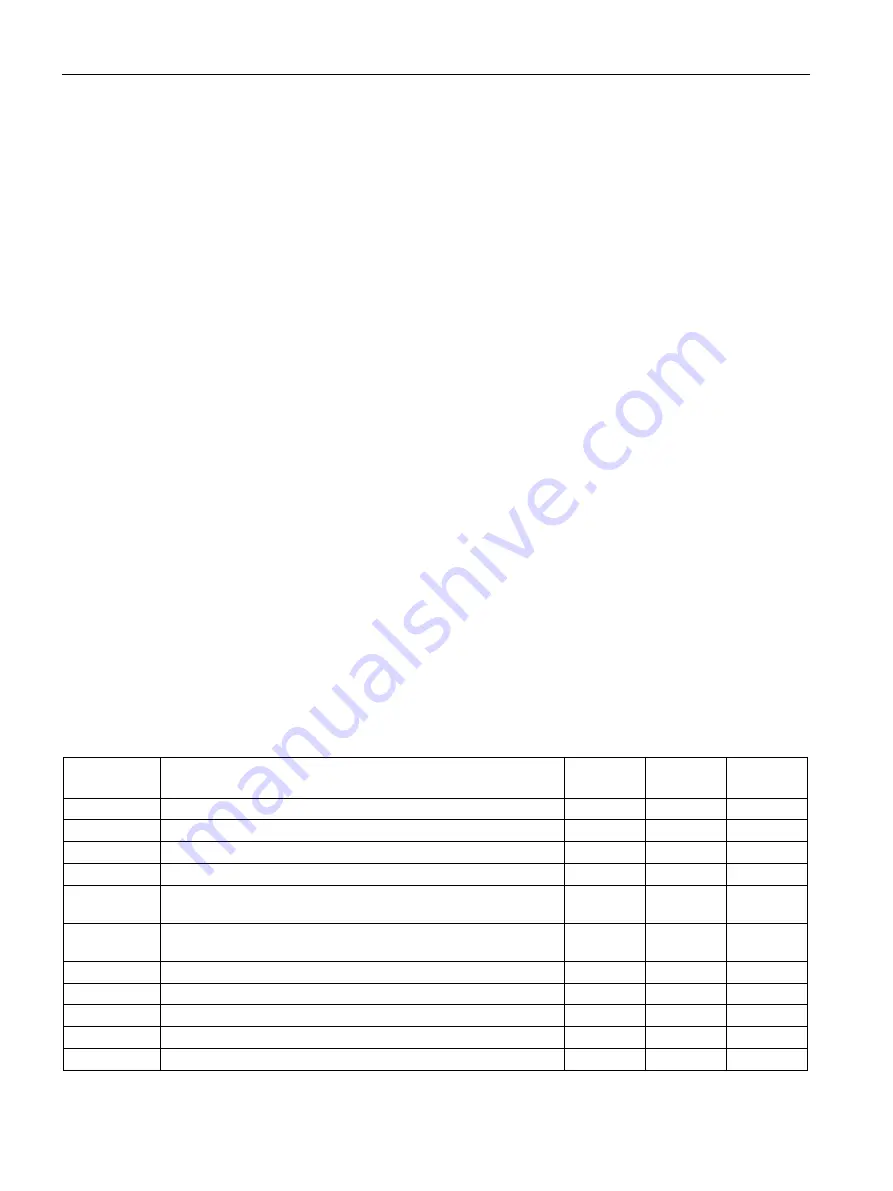
Communication
11.1 Communication according to PROFIdrive
Drive functions
736
Function Manual, 11/2017, 6SL3097-4AB00-0BP5
11.1.1
PROFIdrive application classes
There are different application classes for PROFIdrive according to the scope and type of the
application processes. PROFIdrive features a total of 6 application classes, the 3 most
important are compared here.
●
Class 1 (AK1):
The drive is controlled using a speed setpoint via PROFIBUS/PROFINET. In this case,
speed control is fully handled in the drive.
Typical application examples include simple frequency converters for controlling pumps
and fans.
●
Class 3 (AK3):
In addition to the speed control, the drive also includes a positioning control, which
means that it operates as an autonomous single-axis positioning drive while the higher-
level technological processes are performed in the control system. Positioning requests
are transferred to the drive controller via PROFINET (or PROFIBUS) and started.
●
Class 4 (AK4):
This PROFIdrive application class defines a speed setpoint interface, where the speed
control is realized in the drive and the closed-loop position control in the control system,
such as is required for robotics and machine tool applications with coordinated motion
sequences on multiple drives.
Motion control is primarily implemented using a central numerical controller (NC). The
position control loop is closed via the bus, i.e. the communication between the controller
and the drive must be isochronous.
Selection of telegrams depending on the PROFIdrive application class
The following Table provides an overview of which telegram can be used reach which
PROFIdrive application class:
Table 11- 4 Selection of telegrams depending on the PROFIdrive application class
Telegram
(p0922 = x)
Description
Class 1
Class 3
Class 4
1
Speed setpoint, 16-bit
x
-
-
2
Speed setpoint, 32-bit
x
-
-
3
Speed setpoint, 32-bit with 1 position encoder
x
-
x
4
Speed setpoint, 32-bit with 2 position encoders
x
-
x
5
Speed setpoint, 32 bit with 1 position encoder and Dynamic Ser-
vo Control
-
-
x
6
Speed setpoint, 32 bit with 2 position encoders and Dynamic
Servo Control
-
-
x
7
Basic positioner with selection of the traversing block
-
x
-
9
Basic positioner with direct setpoint input (MDI)
-
x
-
20
16-bit speed setpoint for VIK-Namur
x
-
-
81
Standard encoder
-
-
-
82
Standard encoder with speed actual value 16 bit
-
-
-
Содержание SINAMICS S120
Страница 1: ......
Страница 2: ......
Страница 24: ...Contents Drive functions 24 Function Manual 11 2017 6SL3097 4AB00 0BP5 ...
Страница 202: ...Servo control 4 21 Voltage precontrol Drive functions 202 Function Manual 11 2017 6SL3097 4AB00 0BP5 ...
Страница 296: ...Vector control 5 23 Asynchronous pulse frequency Drive functions 296 Function Manual 11 2017 6SL3097 4AB00 0BP5 ...
Страница 312: ...V f control vector control 6 5 Vdc control Drive functions 312 Function Manual 11 2017 6SL3097 4AB00 0BP5 ...
Страница 932: ......
Страница 1044: ...Appendix A 2 Documentation overview Drive functions 1044 Function Manual 11 2017 6SL3097 4AB00 0BP5 A 2 Documentation overview ...
Страница 1082: ...Appendix A 7 Functions of SINAMICS S120 Combi Drive functions 1082 Function Manual 11 2017 6SL3097 4AB00 0BP5 ...
Страница 1094: ......