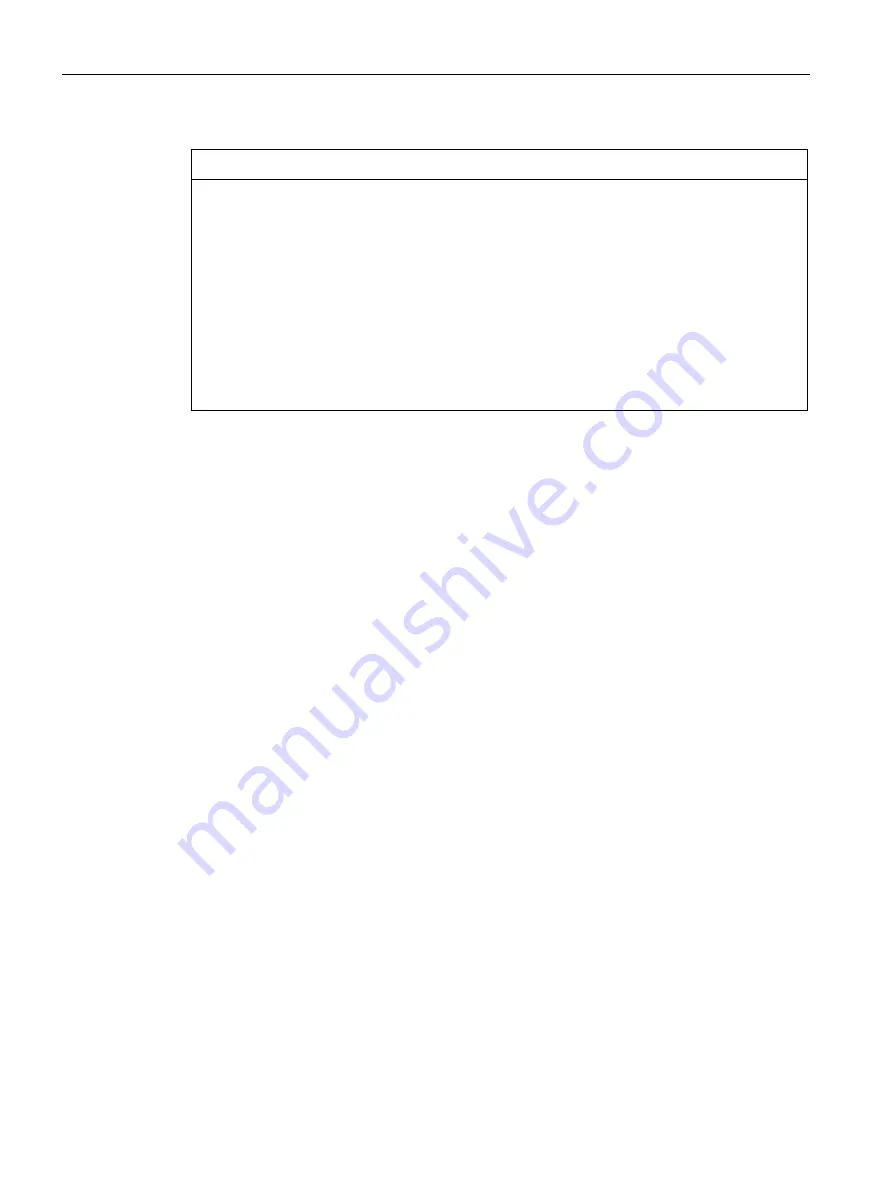
Vector control
5.22 Bypass
Drive functions
284
Function Manual, 11/2017, 6SL3097-4AB00-0BP5
NOTICE
Incorrect synchronization as a result of an incorrect phase sequence
The target frequency r3804 is specified as an absolute value. It does not contain
information about the direction of the rotating field (phase sequence)!
If the phase sequence of the line voltage, which must be synchronized with, does not match
the motor voltage phase sequence, then this results in incorrect synchronization. In the
worst-case scenario, this can mechanically damage the plant or system.
•
Ensure that the line voltage phase sequence matches that of the motor voltage. You can
correct the phase sequence as follows:
–
Interchange the two feeder cables at the converter output or at the line contactor.
–
Correct the phase sequence of the motor or converter output voltage using p1820 or
p1821.
Requirement
The bypass function is only possible for encoderless closed-loop speed control (p1300 = 20)
or V/f control (p1300 = 0...19) and when an induction motor is used.
Features
●
Available for vector control
●
Available for induction motors without encoder
Commissioning the bypass function
The bypass function is part of the function module "technology controller" that can be
activated when using the commissioning wizard. Parameter r0108.16 indicates whether it
has been activated.
5.22.2
Bypass with synchronization with overlap
Description
The "Bypass synchronized with overlap" is used for drives with low inertia. These are drives
in which the speed would decrease very quickly when contactor K1 is opened.
When "bypass with synchronization with overlap (p1260 = 1)" is activated, the motor is
transferred, synchronized to the line supply and is also retrieved again. During the
changeover, the two contactors K1 and K2 are simultaneously closed for a time (phase lock
synchronization).
A voltage sensing module VSM10 is required for this type of bypass which measures the line
supply voltage required for the drive to be synchronized.
Содержание SINAMICS S120
Страница 1: ......
Страница 2: ......
Страница 24: ...Contents Drive functions 24 Function Manual 11 2017 6SL3097 4AB00 0BP5 ...
Страница 202: ...Servo control 4 21 Voltage precontrol Drive functions 202 Function Manual 11 2017 6SL3097 4AB00 0BP5 ...
Страница 296: ...Vector control 5 23 Asynchronous pulse frequency Drive functions 296 Function Manual 11 2017 6SL3097 4AB00 0BP5 ...
Страница 312: ...V f control vector control 6 5 Vdc control Drive functions 312 Function Manual 11 2017 6SL3097 4AB00 0BP5 ...
Страница 932: ......
Страница 1044: ...Appendix A 2 Documentation overview Drive functions 1044 Function Manual 11 2017 6SL3097 4AB00 0BP5 A 2 Documentation overview ...
Страница 1082: ...Appendix A 7 Functions of SINAMICS S120 Combi Drive functions 1082 Function Manual 11 2017 6SL3097 4AB00 0BP5 ...
Страница 1094: ......