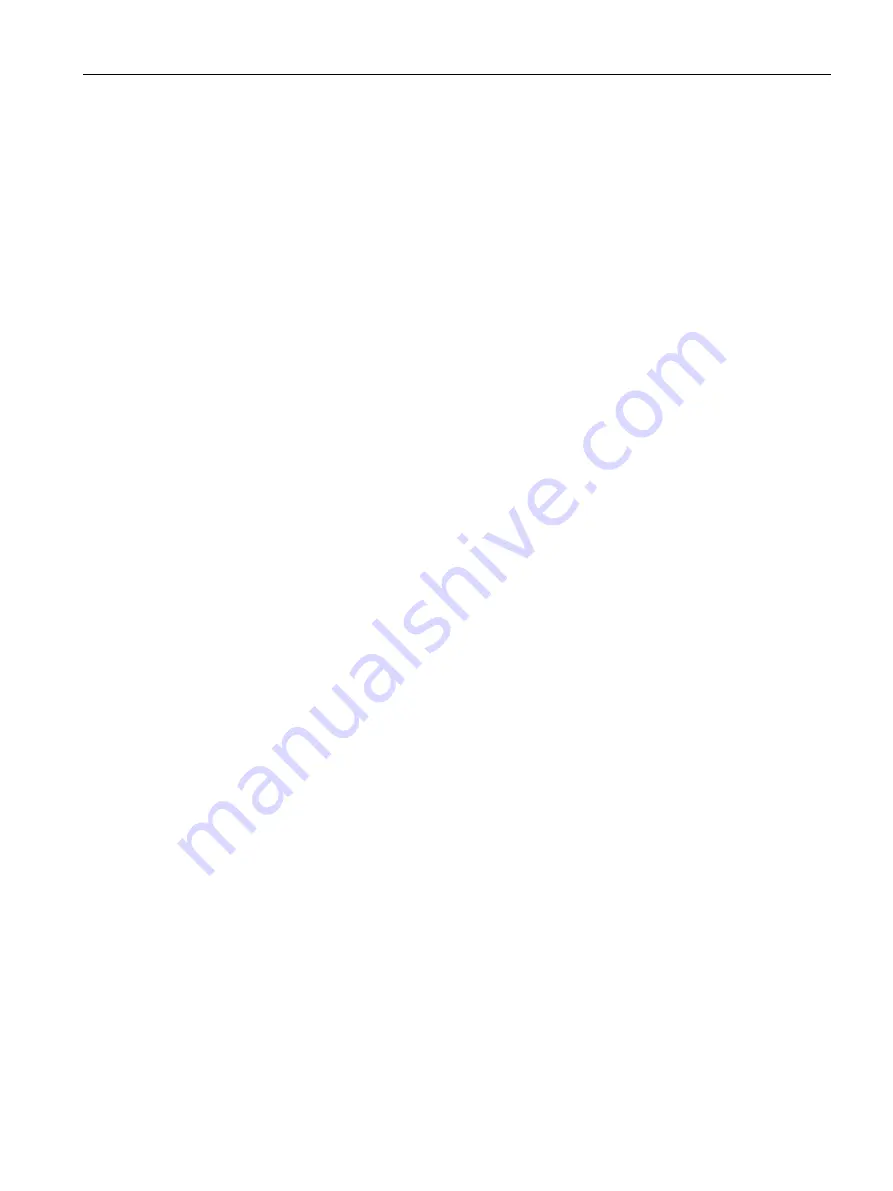
Basic information about the drive system
13.12 System rules, sampling times and DRIVE-CLiQ wiring
Drive functions
Function Manual, 11/2017, 6SL3097-4AB00-0BP5
1017
13.12.4.2
Recommended interconnection rules
The following recommended rules should be observed for the DRIVE-CLiQ wiring:
General
●
The following applies to all DRIVE-CLiQ components with the exception of the Control
Unit: The DRIVE-CLiQ sockets Xx00 are DRIVE-CLiQ inputs (Uplink), the other DRIVE-
CLiQ sockets are outputs (Downlink).
–
The DRIVE-CLiQ cable from the Control Unit should be connected to DRIVE-CLiQ
socket X200 on the first booksize power unit or X400 on the first chassis power unit.
–
The DRIVE-CLiQ connections between the power units should each be connected
from the DRIVE-CLiQ sockets X201 to X200 and/or X401 to X400 on the follow-on
component.
Line Modules
●
A single Line Module should be connected directly to the Control Unit (recommended
DRIVE-CLiQ socket: X100).
–
Several Line Modules should be connected in series.
Motor Modules
●
No more than 6 Motor Modules should be connected to a DRIVE-CLiQ line on the Control
Unit (including with vector, V/f control).
●
Motor Modules should be connected directly to the Control Unit in vector control.
–
If DRIVE-CLiQ socket X100 is already assigned to a Line Module, DRIVE-CLiQ socket
X101 should be used.
–
Several Motor Modules should be connected in a line.
●
In servo control, Motor Modules should be connected to a DRIVE-CLiQ line together with
the Line Module.
–
Several Motor Modules should be connected in a line.
–
If there is already a Line Module present, the first Motor Module should be connected
in line to socket X201 of the Line Module.
–
If there is no Line Module present, the first Motor Module should be connected directly
to the Control Unit (recommended DRIVE-CLiQ socket: X100).
●
If the Motor Modules need to be distributed across two DRIVE-CLiQ lines (e.g. on
account of the predetermined current controller sampling times), the next higher DRIVE-
CLiQ socket on the Control Unit should be used.
Example, vector control in the chassis format:
–
Active Line Module current controller sampling time 400 µs: X100
–
Motor Modules current controller sampling time 250 µs: X101
–
Motor Modules current controller sampling time 400 µs: X102
●
Only one end node should be connected to free DRIVE-CLiQ sockets within a DRIVE-
CLiQ line (e.g. Motor Modules wired in a line), for example, one Sensor Module or one
Terminal Module, without routing to additional components.
Содержание SINAMICS S120
Страница 1: ......
Страница 2: ......
Страница 24: ...Contents Drive functions 24 Function Manual 11 2017 6SL3097 4AB00 0BP5 ...
Страница 202: ...Servo control 4 21 Voltage precontrol Drive functions 202 Function Manual 11 2017 6SL3097 4AB00 0BP5 ...
Страница 296: ...Vector control 5 23 Asynchronous pulse frequency Drive functions 296 Function Manual 11 2017 6SL3097 4AB00 0BP5 ...
Страница 312: ...V f control vector control 6 5 Vdc control Drive functions 312 Function Manual 11 2017 6SL3097 4AB00 0BP5 ...
Страница 932: ......
Страница 1044: ...Appendix A 2 Documentation overview Drive functions 1044 Function Manual 11 2017 6SL3097 4AB00 0BP5 A 2 Documentation overview ...
Страница 1082: ...Appendix A 7 Functions of SINAMICS S120 Combi Drive functions 1082 Function Manual 11 2017 6SL3097 4AB00 0BP5 ...
Страница 1094: ......