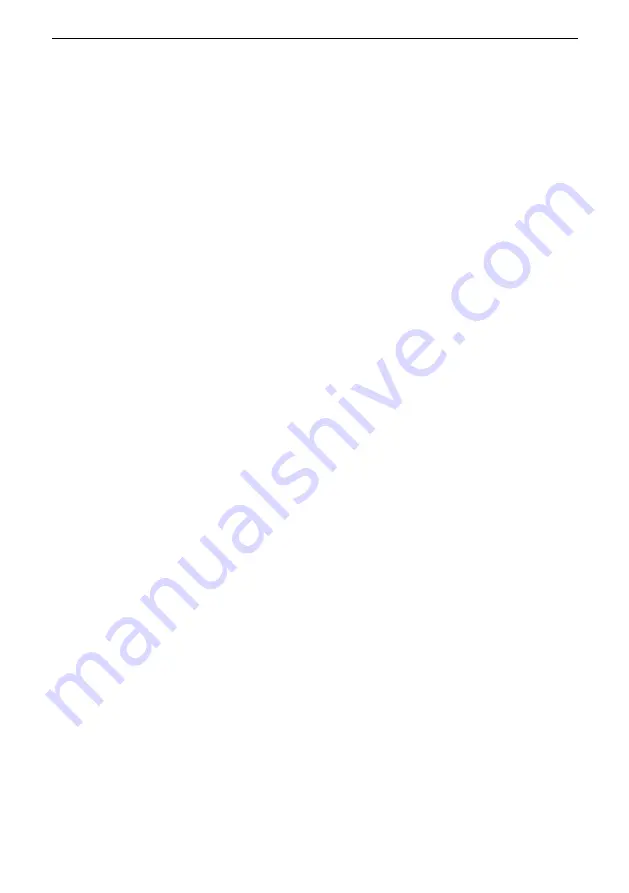
SV800/SV800A User Manual 5 Introduction of operation and running
83
5.5.2 Setting of motor rotation inertia
In the speed control of SV800 series products, a speed observer and a torque observer are added
to the control algorithm. The speed control performance can be improved by setting the motor
rotation inertia. When the inertia is not learned or the inertia of the motor and transmission
system is not determined, the general inertia value of the transmission system can be quickly
determined by manually adjusting the inertia. The specific method is as follows:
Set 20% to 100% of the sum of the motor inertia of the motor rotor and the mechanical inertia
of the load in parameter d0-02 / d0-05 (the first and second motor speed control inertia). If you
don’t know the exact inertia of the motor, you can enter low inertia value firstly, and then
gradually increase the set value. If the motor vibration or the current envelope is not smooth,
return to the set value of the previous step. In different transmission conditions, the inertia of the
belt drive system does not include the load mechanical part, only the inertia of the rotor portion
of the motor and the pulley portion connected to the motor shaft is calculated. For gear driven
system, when increasing the inertia parameter, if the gear meshing is caused by tooth backlash
due to excessive backlash, reduce the setting parameters or increase the gear meshing degree.
Because the intelligent control algorithm is used, the general inertia parameter of the operating
conditions does not need to be adjusted to ensure system stability and speed. Responsiveness is
taken into account. If the speed observer or torque observer is eliminated, the speed control is a
typical PI control mode.
Note: The setting
unit
of d0-02/ d0-05 is gm
2
. You can multiply the obtained value kgm2 by 1000 as the
setting value of this parameter. In addition, the parameter setting is inertia, not GD2, so GD2 needs to be
divided by 4.
5.5.3 Speed control proportional coefficient and integral time constant setting
When the vector control mode is used for speed control, it runs in the state connected with the
mechanical transmission system. By adjusting d0-00 / d0-03 (the first / second motor speed
control proportional gain) and d0-01 / d0-04 (the first / Second motor speed control integral
time constant) for speed control debugging.
When the speed is set to a certain speed for constant speed operation, if the speed fluctuation is
caused by the load fluctuation on the load side, increase the speed control proportional gain. If
the controlled speed of the motor also fluctuates during constant speed operation, please reduce
the speed control integration time constant to increase the adjustment strength of the integration
link. If the transmission mechanism such as belt oscillates or the gear box vibrates and roars,
please reduce the speed control proportional gain and increase the integration time constant. As
shown in
Fig. 5-11
: