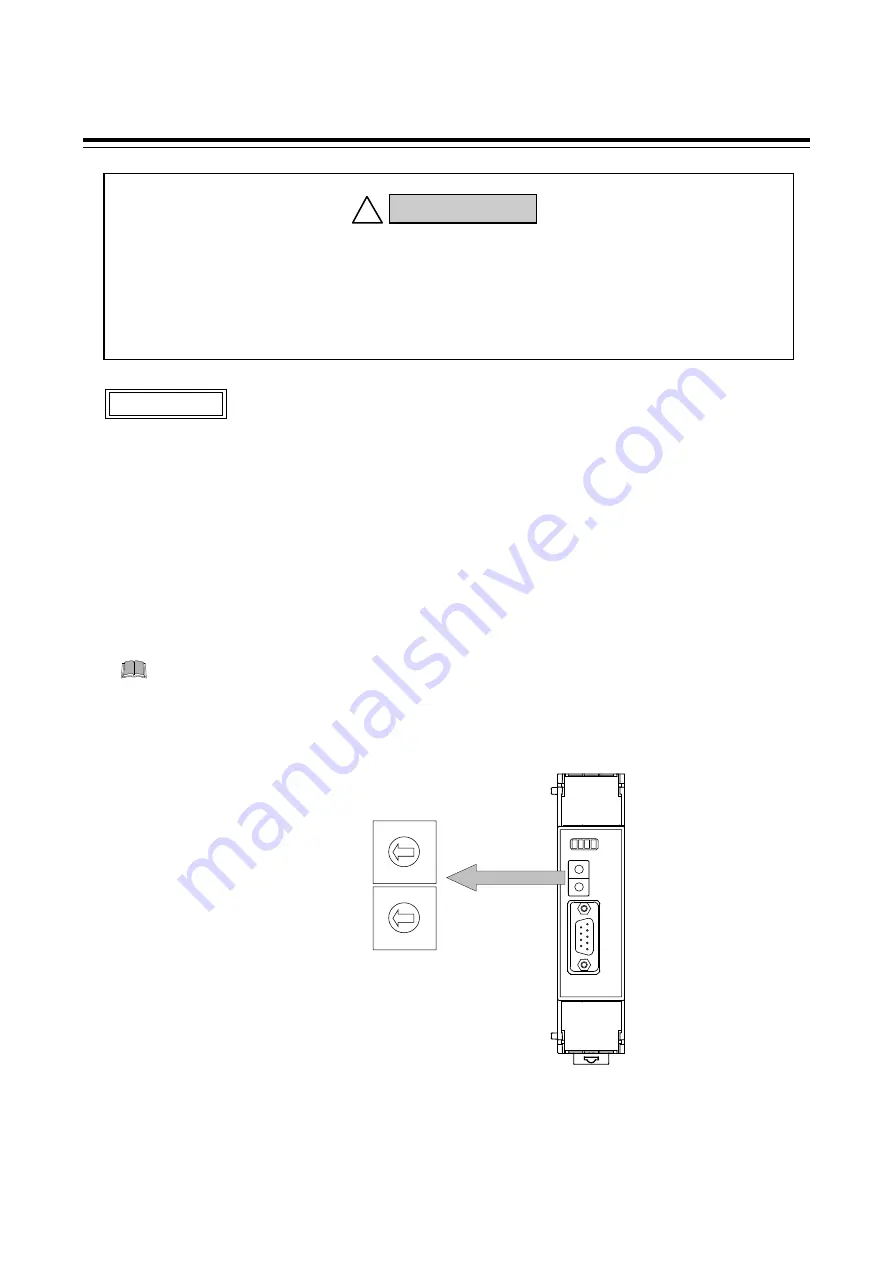
IMR01Y35-E3
15
5. SETTING
Do not separate the mainframe from the terminal base with the power turned on.
If so, instrument failure may result.
5.1 PROFIBUS Address Setting
The master communicates with the selected slave by specifying that slave’s address number. Each
slave must have a unique address number for this data transmission. Set the slave address with the
address setting switch prior to operation.
With the tow rotary switch in the front of the COM-JG, set an address number on the PROFIBUS. For
this setting, use a small slotted screwdriver.
No communication with PROFIBUS can be conducted with each factory set value (00h)
left as it is. Set it to the same value as the PROFIBUS address set when system
configured.
Setting range:
1 to 125 [01h to 7Dh: hexadecimal]
(Factory set value: 00h)
Address setting switch
9
8
7
C
B A
6
5
4
3
2
1
0
F E D
9
8
7
C
B A
6
5
4
3
2
1
0
F E D
High-order digit
setting
(Set value
×
10h)
Low-order digit
setting
(Set value
×
1h)
COM-JG
CAUTION
To prevent electric shock or instrument failure, always turn off the power
before setting the switch.
To prevent electric shock or instrument failure, never touch any section other
than those instructed in this manual.
WARNING
!
Содержание COM-JG
Страница 1: ...IMR01Y35 E3 COM JG For SRZ RKC INSTRUMENT INC PROFIBUS Communication Converter Instruction Manual ...
Страница 81: ...8 USAGE EXAMPLE IMR01Y35 E3 75 5 If the PLC is registered the display becomes as follows ...
Страница 125: ...The first edition AUG 2006 IMQ00 The third edition JUL 2010 IMQ00 ...