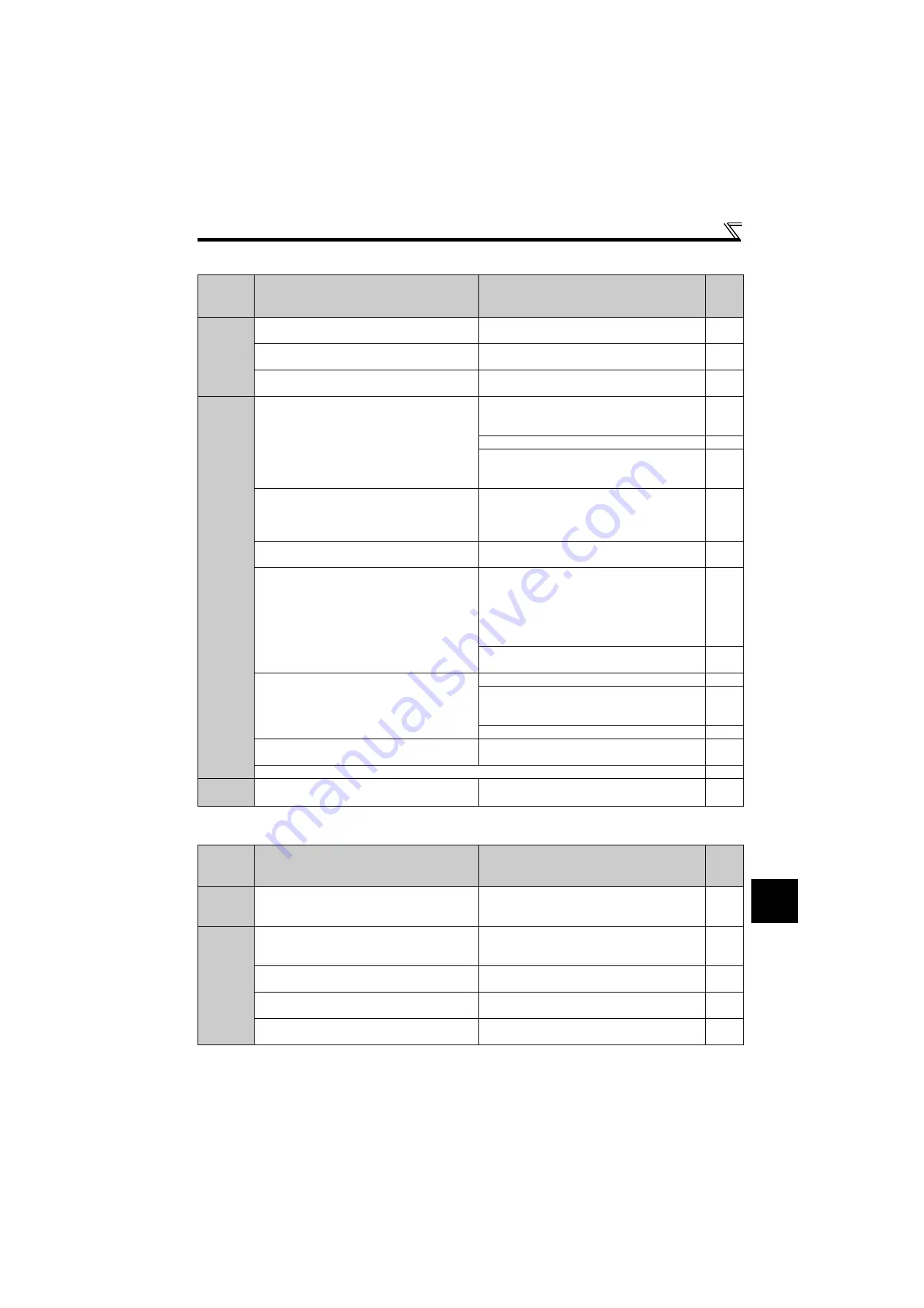
315
Check first when you have a trouble
5.5.12 Speed does not accelerate
5.5.13 Unable to write parameter setting
Check
points
Possible Cause
Countermeasures
Refer
to
page
Input
signal
Start command and frequency command are chattering.
Check if the start command and the frequency
command are correct.
—
The wiring length used for analog frequency command
is too long, and it is causing a voltage (current) drop.
Perform analog input bias/gain calibration.
Input signal lines are affected by external EMI.
Take countermeasures against EMI, such as using
shielded wires for input signal lines.
Parameter
Setting
Pr. 1, Pr. 2, Pr. 18, calibration parameter C2 to C7
settings
are improper.
Check the settings of
Pr. 1 Maximum frequency and Pr. 2
Minimum frequency
. If you want to run the motor at 120Hz
or higher, set
Pr. 18 High speed maximum frequency
.
Check the
calibration parameter C2 to C7
settings.
During IPM motor control, maximum frequency is limited
to the maximum motor speed (frequency) of the IPM
motor.
The maximum voltage (current) input value is not set
during the External operation.
(Pr.125, Pr.126, Pr.18)
Check the
Pr.125 Terminal 2 frequency setting gain
frequency
and
Pr.126 Terminal 4 frequency setting gain
frequency
settings. To operate at 120Hz or higher, set
Pr.18 High speed maximum frequency
.
Torque boost
(Pr. 0, Pr. 46)
setting is improper under V/F
control, so the stall prevention function is activated.
Increase/decrease
Pr. 0 Torque boost
setting value by
0.5% increments so that stall prevention does not occur.
V/F pattern is improper when V/F control or General-
purpose magnetic flux vector control is performed.
(Pr. 3, Pr. 14, Pr. 19)
Set rated frequency of the motor to
Pr. 3 Base frequency
.
(V/F control, General-purpose magnetic flux vector
control)
Use
Pr. 19 Base frequency voltage
to set the base voltage
(e.g. rated motor voltage). (V/F control, General-purpose
magnetic flux vector control)
Change
Pr. 14 Load pattern selection
according to the load
characteristic. (V/F control)
Stall prevention function is activated due to a heavy
load.
Reduce the load weight.
—
Set
Pr. 22 Stall prevention operation level
higher according
to the load. (Setting
Pr. 22
too large may result in
frequent overcurrent trip (E.OC
).)
Check the capacities of the inverter and the motor.
—
Auto tuning is not performed under General-purpose
magnetic flux vector control.
Perform offline auto tuning.
During PID control, output frequency is automatically controlled to make measured value = set point.
Main
Circuit
Brake resistor is connected between terminal P/+ and
P1 by mistake.
Connect an optional brake transistor (MRS type, MYS
type, FR-ABR) between terminal P/+ and PR.
Check
points
Possible Cause
Countermeasures
Refer
to
page
Input
signal
Operation is being performed (signal STF or STR is
ON).
Stop the operation.
When
Pr. 77
= "0" (initial value), write is enabled only
during a stop.
Parameter
Setting
You are attempting to set the parameter in the External
operation mode.
Choose the PU operation mode.
Or, set
Pr. 77
= "2" to enable parameter write regardless
of the operation mode.
Parameter is disabled by the
Pr. 77 Parameter write
selection
setting.
Check
Pr. 77 Parameter write selection
setting.
Key lock is activated by the
Pr. 161 Frequency setting/key
lock operation selection
setting.
Check
Pr. 161 Frequency setting/key lock operation selection
setting.
Operation mode and a writing device do not
correspond.
Check
Pr. 79, Pr. 338, Pr. 339, Pr. 551,
and select an
operation mode suitable for the purpose.
Содержание FR-F700PJ Series
Страница 13: ...IX MEMO ...
Страница 29: ...16 MEMO ...
Страница 76: ...63 MEMO ...
Страница 299: ...294 MEMO ...
Страница 321: ...316 MEMO ...
Страница 346: ...341 APPENDIX This chapter provides the APPENDIX of this product Always read the instructions before using the equipment ...