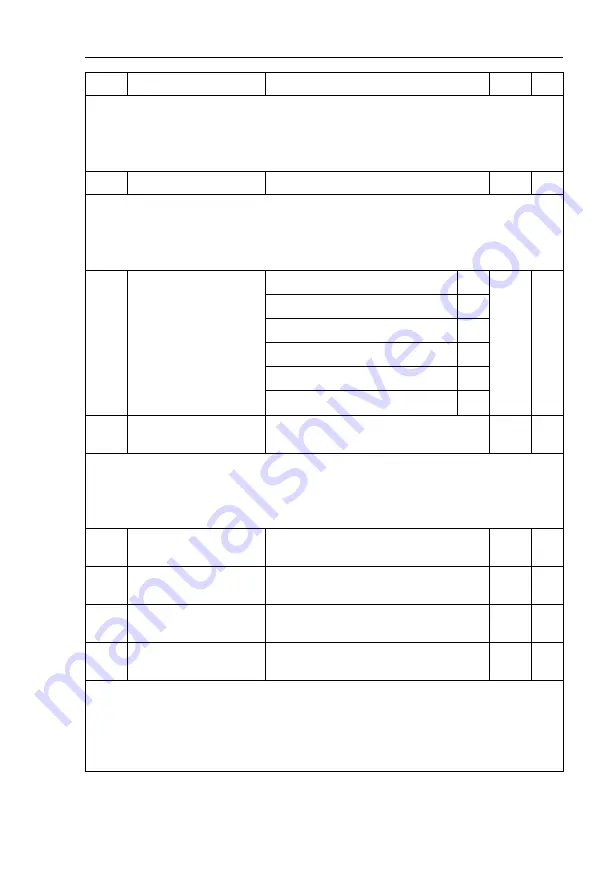
Section V. Parameter Function Table
45
F2.06
Vector control slip gain
50%~200%
100%
☆
This parameter is used to adjust motor steady speed precision for zero-speed sensor vector control
mode. Please turn up the parameter value when with load motor running in low speed. On the contrary,
when the with load motor running in high speed, please turn down the parameter value.
This parameter is also used to adjust the output current value with the same load for speed sensor
vector control.
F2.07
Speed-loop filter time
0.000s~0.100s
0.000s
☆
In vector control mode, speed-loop regulator outputs torque current command. F2.07 is used to filter
the torque command.
Generally speaking, the parameter needs not to be modified. Users could properly increase the
filtering time when speed fluctuation is relatively big, and decrease the value when motor oscillation occurs.
If filtering time is small, inverter output torque might fluctuate greatly, but response speed will be fast.
F2.09
Torque upper limit source in
speed control mode
F2.10
0
0
☆
AI1
1
AI2
2
AI3
3
PULSE setup
4
Communication setup
5
F2.10
Torque upper limit digital setup
in speed control mode
0.0%~200.0%
150.0%
☆
In speed control mode, inverter maximum torque output is controlled by torque upper limit.
Range for 1-5 selections of F2.09 are corresponding to the setting range of F2.10.
F2.09 is used to select torque upper limit source. When F2.09 is set through analog, PULSE setup,
communication setup, which 100% corresponding to F2.10. 100% of F2.10 is the rated torque of the
inverter.
F2.13
Excitation regulation
proportional gain
0~20000
2000
☆
F2.14
Excitation regulation
integration gain
0~20000
1300
☆
F2.15
Torque regulation
proportional gain
0~20000
2000
☆
F2.16 Torque requlation integration
gain
0~20000
1300
☆
Vector control current-loop PI regulation, which is automatically obtained after asynchronous motor
complete tuning or synchronous motor complete tuning. It generally needs not to be modified.
Caution
:
Integration regulator of current loop directly set integration gain without taking integration
time as the dimension. Excessive current loop PI gain may lead oscillation to the entire control loop circuit.
If current oscillation or torque fluctuation is relatively big, users could manually turn down the PI
proportional gain or integration gain.
Содержание HV610C Series
Страница 1: ...HV610C Series Frequency Inverter User Manual HNC Electric Limited ...
Страница 25: ...Section II Installation Wiring 12 2 3 2 Typical wiring of HV610C in Crane applications ...
Страница 29: ...Section II Installation Wiring 16 Control board terminal layout ...
Страница 167: ......
Страница 175: ......