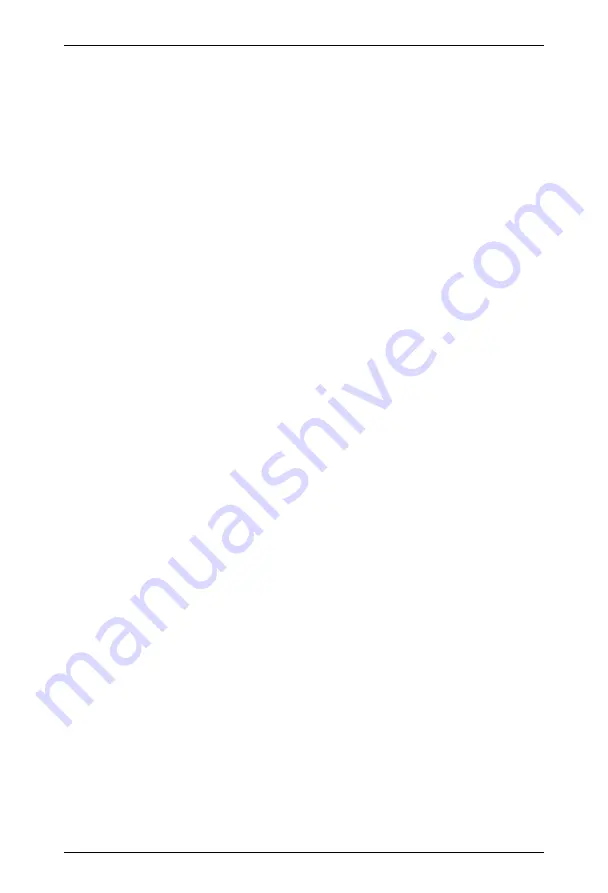
Chapter V Basic Operation Instructions
133
Proportional adjustment (Kp): When there is a deviation between the feedback and the input,
the output and the deviation are adjusted in proportion. If the deviation is constant, the adjustment
amount is also constant. Proportional adjustment can quickly respond to changes in feedback, but
just proportional adjustment cannot achieve non-differential control. The larger the proportional
gain, the faster the adjustment speed of the system, but if it is too large, oscillation will occur. The
adjustment method is to first set the integration time to be very long and the differential time to
zero. Use only proportional adjustment to make the system run, change the input quantity, and
observe the stable deviation (static difference) between the feedback signal and the input quantity.
If the static difference is in the direction of target value changes (for example, increasing the input
quantity, the feedback quantity is always less than the target value after the system is stable),
continue to increase the proportional gain, otherwise decrease the proportional gain, and repeat the
above process until the static difference is relatively small.
Integration time (Ti): When there is a deviation between the feedback and the input value, the
output adjustment accumulates continuously. If the deviation persists, the adjustment increases
constantly, until there is no deviation. The integral regulator can effectively eliminate static
difference. If the integral regulator is too strong, there will be repeated overshoot, making the
system unstable until oscillation occurs. The characteristics of the oscillation caused by excessive
integration are as follows: The feedback signal swings up and down at an input quantity, and the
swing gradually increases until it oscillates. The adjustment of the integration time parameter is
generally from large to small, gradually adjust the integration time, and observe the effect of the
system adjustment until the stable speed of the system reaches the requirements.
Differential time (Td): When the deviation between feedback and input changes, an
adjustment proportional to the deviation change rate is output. The adjustment is only related to the
direction and magnitude of the deviation change, and has nothing to do with the direction and
magnitude of the deviation itself. The function of differential adjustment is to adjust according to
the changing trend when the feedback signal changes, thus to suppress the change of the feedback
signal. Please use the differential regulator with caution, because the differential regulation is easy
to amplify the interference of the system, especially the interference with a higher change
frequency.
General steps for PID parameter setting
a. Determine the proportional gain Kp
When determining the proportional gain Kp, first remove the integral and differential items of
PID. Generally, assumed Ti = 0 and Td = 0 (for details, see the description of PID parameter
setting), so that the PID is of pure proportional adjustment. The input is set to 60%
~
70% of the
maximum value allowed by the system. The proportional gain Kp is increased from 0 gradually
until the system oscillates; in turn, the proportional gain Kp is gradually decreased from this time
until the system oscillation disappears. In this case, the proportional gain Kp is recorded, and the
proportional gain Kp of PID is set to 60%
~
70% of the current value. The proportional gain Kp
debugging is completed.
b. Determine the integration time Ti
After the proportional gain Kp is determined, set a larger initial value of the integration time
Ti, and then gradually decrease Ti until the system oscillates, and then in turn, increase Ti gradually
until the system oscillation disappears. Record the Ti at this time and set the integration time
constant Ti of PID to 150%
~
180% of the current value. The integration time constant Ti
debugging is completed.
c. Determine the differential time Td
Generally, the differential time Td needs not to be set (0). To set, the method is the same with
that of determining Kp and Ti, taking 30% without oscillation.
d. The system is debugged with or without load, and then the PID parameters are fine-tuned
until the requirements are met.