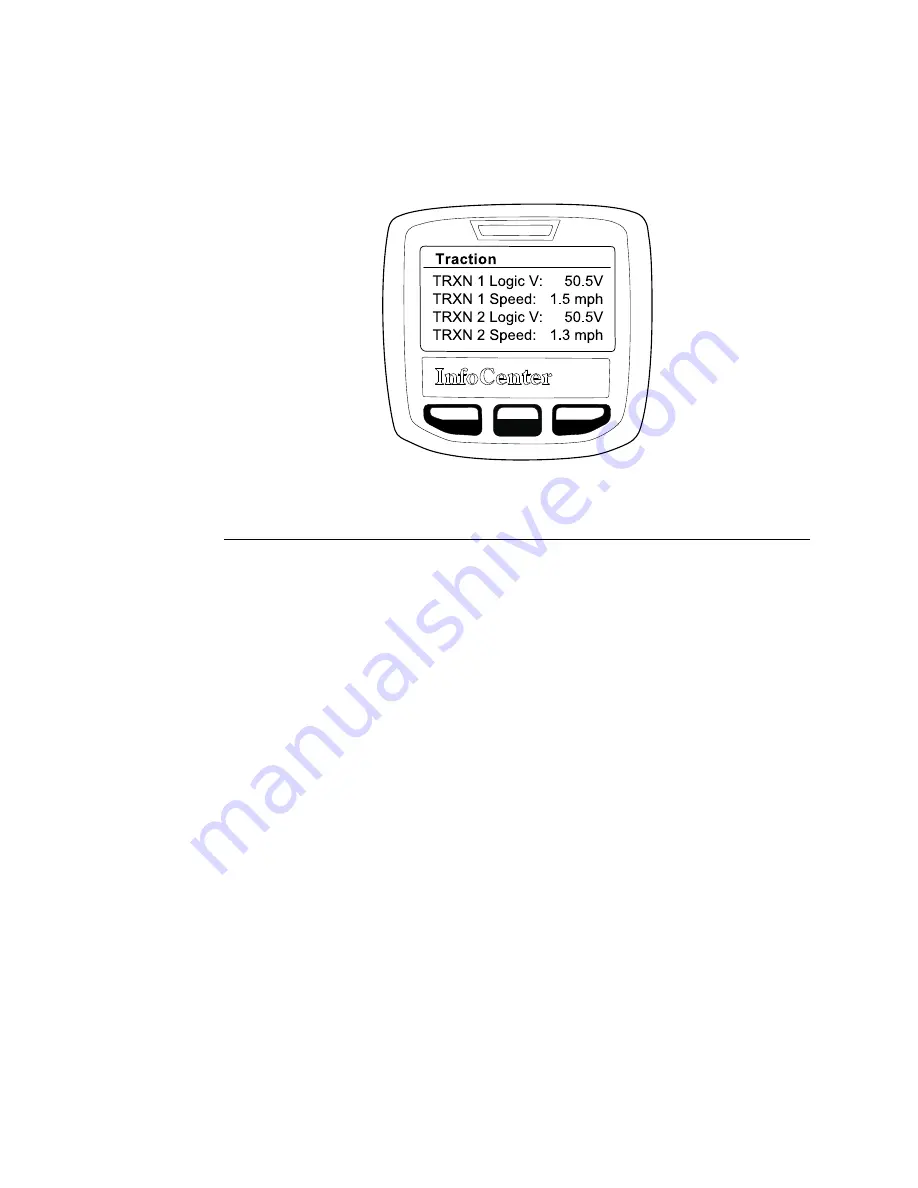
Testing the Front Traction Motor Controllers (continued)
1. Park the machine on a level surface, lower the cutting units and set the key
switch to the O
FF
position.
2. Set the function control switch to the N
EUTRAL
position.
3. Sit in the operator seat and set the key switch on the O
N
position.
4. Access the InfoCenter
Diagnostics > Traction > Inputs
screen.
g292803
Figure 56
(machine turning to the left)
5. 48V system voltage should be present at the traction motor controller logic
circuit
TRXN # Logic V
.
• If – – – appears, the controller is not communicating on the CAN bus.
Voltage must be present at the controller logic circuit before communication
can occur on the CAN bus.
If voltage is not present at the logic circuit, the logic circuit is damaged.
The circuit wiring should be checked for corrosion or damage and
cleaned or repaired as necessary.
If logic voltage is present at the controller, and CAN bus communication
is suspect, the CAN bus circuit is damaged. The CAN bus wiring
should be checked for corrosion or damage and cleaned or repaired
as necessary. The traction motor controller CAN bus transceiver can
also be tested if necessary; refer to
Testing Devices (Nodes) on the
.
• Traction motor speed should be displayed while the traction motors are
engaged
TRXN # Speed
. Individual traction motor speed is related to
the current turning radius (RDS).
6. Locate the front traction motor controller and disconnect it from the machine
wire harness. Check the controller connector and the harness connector
for damage or corrosion and clean or repair as necessary. Ensure all the
connector pins are equally seated in the connector body.
Electrical System: Testing the Electrical Components
Page 5–52
Greensmaster® eTriFlex 3360 and 3370
19239SL Rev B