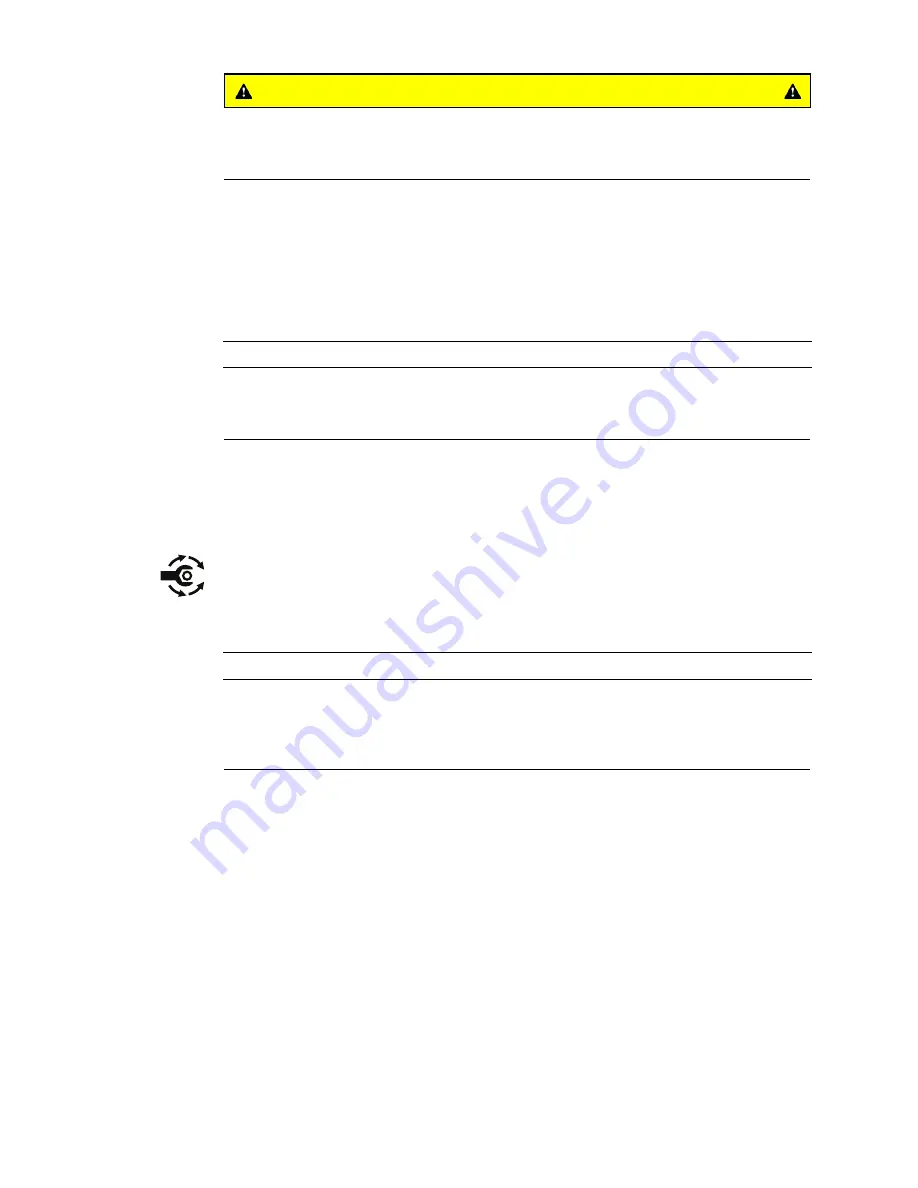
Installing the Bedbar (continued)
CAUTION
Contact with the reel, bedknife or other cutting unit parts can result
in personal injury. Use heavy gloves when handling the bedbar.
Note:
If a new bedknife is attached to the bedbar, there may be interference
between the bedknife and the reel when installing the bedbar. Turn the
bedbar adjusting screws counterclockwise to increase bedknife clearance
if necessary.
4. Position the bedbar into the cutting unit. Make sure that the top of each
bedbar arm is between the washer and adjuster screw flange.
IMPORTANT
When installing the washers, make sure that the plastic washers are
positioned against the side plate.
5. Slide one metal washer and then one plastic washer onto each bedbar pivot
bolt.
6. Position one plastic washer between the bedbar and the inside of each side
plate.
7. Install the bedbar pivot bolt assemblies. Make sure the washers are not
caught on the threads of the pivot bolts. Tighten each bedbar pivot bolt from
22 to 27 N∙m (190 to 240 in-lb)
.
IMPORTANT
Do not over tighten the lock nuts as this can distort the side plates
and affect reel bearing alignment. When the lock nut is correctly
tightened, the inside washers may be loose.
8. Tighten both lock nuts (item 8 in
) until outside washers do not
have any end play and can still can be rotated.
9. Tighten the lock nut (item 4 in
) on each bedbar adjuster assembly
until the adjuster spring is fully compressed, then loosen the lock nut 1/2 turn.
10. Adjust the bedknife to reel contact; refer to the
Cutting Unit Operator’s
Manual
.
DPA Cutting Units: Service and Repairs
Page 7–8
Greensmaster® eTriFlex 3360 and 3370
19239SL Rev B