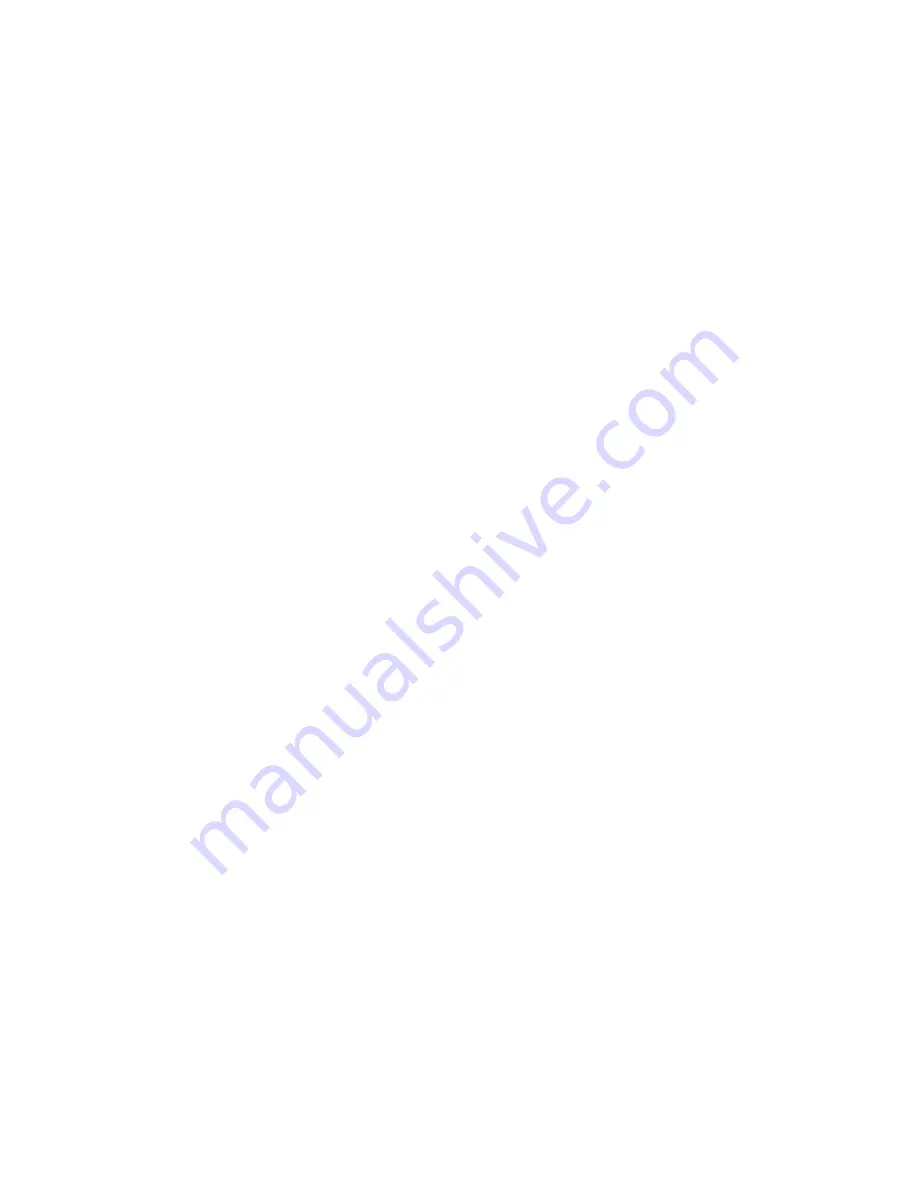
Electrical System Operation
The eTriFlex machines have 4 different functional subsystems. Each subsystem
has components that operate on 12 VDC, and components that operate on
48 VDC. Many of the machine control functions operate on a typical 12 VDC
system. The electric traction motors, electric steering motor, electric cutting
unit lift/lower actuators, and the electric cutting unit motors operate on an 48
VDC electrical system. The 12 VDC and 48 VDC systems include circuits
that support both the logic demands of the various controllers, and the power
supply (bus) required for component operation. Refer to
Components (page 5–23)
for detailed information and testing procedures for all
of the subsystem components.
Traction Subsystem
The traction subsystem and steering subsystem work together to steer the
machine. The rear wheel (steering) sets the direction while the two front wheels
turn the machine using the Radius Dependant Speed System (RDS). Each
front traction motor speed is controlled independently by the RDS. The RDS
also helps prevent the front wheels from scrubbing the turf in turns. For the
subsystems to function properly, the front traction motors must be calibrated to
each other by using the InfoCenter Service>Calibration screen.
The traction subsystem consists of the following components:
•
Function Control Switch: A three position switch on the operator’s console
that allows the operator to select between Neutral and Transport or Mow
speed ranges.
•
Traction Pedal Position Sensor: A dual hall effect sensor attached to the
traction pedal that sends reciprocal signals to the SC5: Traction 1 controller
for direction and speed. The two signals are part of a redundant traction
safety circuit in the case that one signal fails. For the subsystem to function
properly, the traction pedal position sensor must be calibrated for range of
motion by using the InfoCenter Service>Calibration screen.
•
Front Traction Motor Controllers (2): Each traction motor controller operates
and its respective traction motor via a separate interconnect harness.
SC5: Traction 1 (right side): Is considered the primary traction controller
as it controls the precharge function for the traction subsystem, provides
the ground path to energize the traction motor contactor, and receives
traction pedal sensor signals for traction direction and speed, and reports
any traction pedal sensor faults.
SC6: Traction 2 (left side): Is considered the secondary traction controller
as it receives traction pedal sensor signals for traction direction and
speed from the SC5: Traction 1 controller.
•
Front Traction Motors (2): Are 3 phase 48 VDC electric motors located
behind each front wheel and include a separate reduction gear box and disc
brake mechanism. The front traction motors receive all of their operation
commands from their respective traction motor controller.
•
Optional 3WD Traction Motor: Is designed to assist with traction demands in
the forward direction only. The 3WD traction motor is attached to the rear
wheel caster fork and includes an integrated controller and reduction gear
box.
Electrical System: Electrical System Operation
Page 5–4
Greensmaster® eTriFlex 3360 and 3370
19239SL Rev B