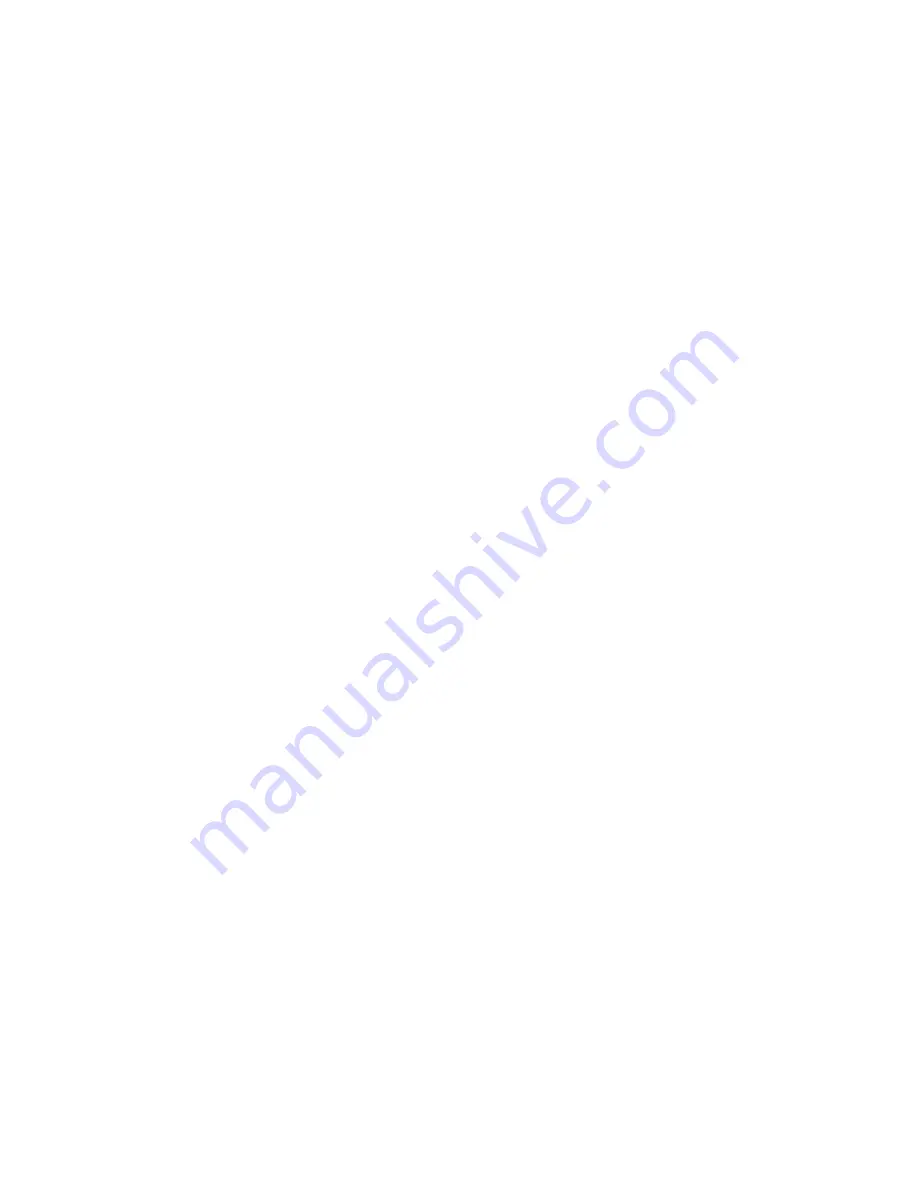
Steering Subsystem
The steering subsystem components work together to coordinate the position
of the steering wheel with the position of the rear caster fork. The Radius
Dependant Speed System (RDS) uses steering position information from the
steering subsystem to control the traction and cutting unit drive subsystems. The
steering subsystem and traction subsystem work together to steer the machine.
The rear wheel (steering) sets the direction while the two front wheels turn the
machine using the RDS; refer to
Traction Subsystem (page 5–4)
for additional
information.
The steering subsystem consists of the following components:
•
Steering Input Device: Connected to the steering wheel, the device converts
steering wheel direction and speed of rotation information inot reciprocal
signals. Both signals are sent to the SC7: Steering motor controller. The
two signals are part of a redundant steering safety circuit in the case that
one signal fails. Tactile feedback (controlled by a PWM signal from the T1:
primary controller) determines the amount of feed back the operator feels
while turning the steering wheel. This feature of the steering input device
produces a more natural power steering feel for the operator.
•
•
SC7: Steering Motor: The SC7: Steering motor is attached to a reduction
gear box and includes an integrated steering motor controller. The Steering
motor receives all of its operation commands from the steering motor
controller. The steering motor controller interprets steering position sensor
data and broadcasts the information via the CAN bus to SC5: Traction 1
controller to manage front wheel speed, and to the steering input device
to determine operator tactile feedback. The steering motor controller is
responsible for reporting steering subsystem faults from the steering input
device, steering motor, and steering position sensor.
•
Steering Position Sensor: A dual hall effect sensor attached to the rear wheel
caster fork sends reciprocal signals to the SC7: Steering motor controller.
The two signals are part of a redundant steering safety circuit in the case that
one signal fails. For the subsystems to function properly, the steering position
sensor must be calibrated for center position, and for range of motion by
using the InfoCenter Service>Calibration screen.
Greensmaster® eTriFlex 3360 and 3370
Page 5–5
Electrical System: Electrical System Operation
19239SL Rev B