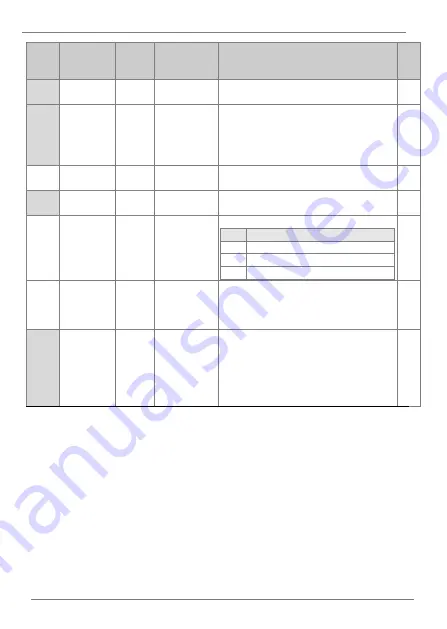
POWER ELECTRONICS
SD300
DESCRIPTION OF PROGRAMMING PARAMETERS
121
Screen Description Default
value
Range
Function
Set
on
RUN
bA.13
Motor
Current
(*)
1.0 to 1000.0A
Set the motor nominal current in accordance
with the nameplate.
NO
bA.14
No load
Current
(*)
0.5 to 200.0A
Set the measured current at rated frequency
without load. If any difficulties are found when
measuring the current without load, this setting
should be between 30% and 50% of the motor
nameplate rated current.
NO
bA.15
Motor
Voltage
0V
170 to 480V
Set the motor rated voltage according to its
nameplate.
NO
bA.16
Efficiency
(*)
64 to 100%
Set the motor efficiency according to its
nameplate.
NO
bA.17
Inertia Rate
0
0 to 8
Select load inertia based on motor inertia.
OPT. FUNCTION
0
Less than 10 times motor inertia
1
10 times motor inertia
2-8 More than 10 times motor inertia
NO
bA.18
Output power
adjustment
+100
70 to 130%
Fine adjustment of the output power
calculation, increasing its value if it is lower
than expected or reducing it to match the real
value.
YES
bA.19
Input voltage 380V
170 to 240V
320 to 480V
Set the input voltage.
Note:
The default setting value and this
parameter range will vary depending on the
drive supply voltage:
220V
➔
220
400V
➔
380
YES
(*) This value depends on the motor setting.
Summary of Contents for SD 300 Series
Page 1: ...SD300 GETTING STARTED MANUAL LOW VOLTAGE VARIABLE SPEED DRIVE ...
Page 2: ......
Page 3: ...Variable Speed Drive Getting Started Manual Edition February 2019 SD30IM01GI Rev G ...
Page 159: ...POWER ELECTRONICS SD300 DESCRIPTION OF PROGRAMMING PARAMETERS 157 Power off delay ...
Page 174: ...SD300 POWER ELECTRONICS 172 DESCRIPTION OF PROGRAMMING PARAMETERS TI configuration ...
Page 352: ......
Page 353: ......