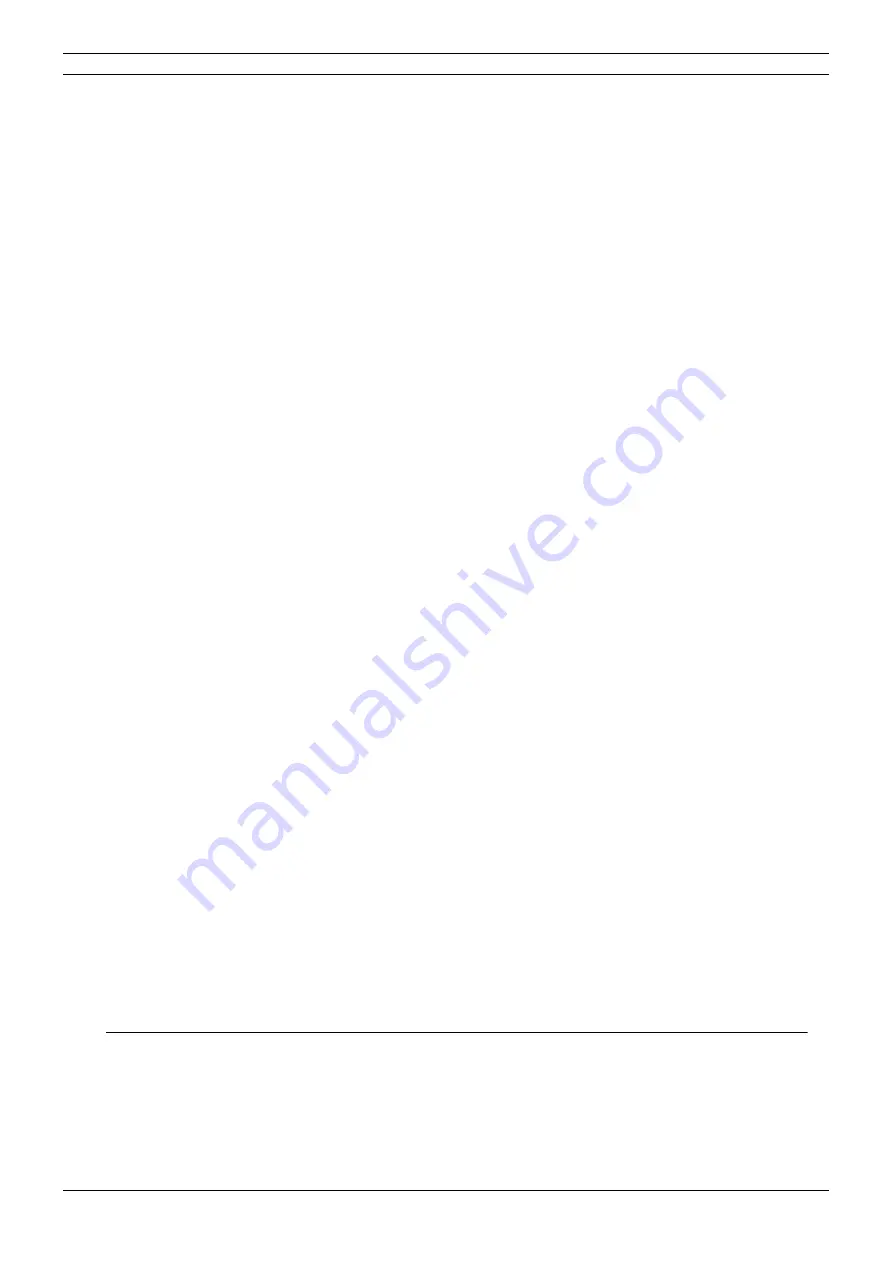
Chapter I - FUNCTIONAL DESCRIPTION
I-12 Planmeca Proline CC panoramic x-ray
Technical Manual
The rotation start sensor defines the starting point (home position) of the rotating arm. When
pressed READY the system will continuously seek for the sensor and rotate the arm to it if it was
pushed aside. Note that if the arm was pushed over to wrong side of the sensor (not towards
center) the system tries to find the sensor by rotating the arm but in wrong direction. In this case
the arm must be pushed over the sensor to the actual operating range and thus enable the sys-
tem to find the sensor.
The rotation end sensor is polled in the end of the rotation. The rotation must stop on the sensor,
otherwise an error is generated. If the sensor was reached and gone over the rotation is stopped
immediately with an error.
Cassette motor
The cassette motor is located on the top of the cassette holder in the cassette end of the rotating
part. It drives the cassette holder (and the film cassette) linearly across the X-ray beam during
the exposure and back during return. In cephalostatic models it also takes care of opening the
secondary slot wide enough and of moving the soft tissue wedge. It is a stepper motor and it gets
it’s drive from the generator processor.
The operating range of this motor is controlled by four sensors on the CASSETTE LIMITS circuit
board. Two of them control the position of the secondary aperture (cassette holder carriage) and
two the end limits of the cassette holder movements.
When driven to READY position the motor is operated till both the cassette holder and the cas-
sette holder carriage start sensors are active. If the cassette is pushed aside the system will seek
back for the sensors. When driven to the end direction normally a certain length is driven and no
sensors are used. The exception is when the equipment is powered on with the cassette not on
the start sensors. Then the cassette is driven all the way till it finds the end sensor of the cassette
holder.
In panoramic models the end sensor of the cassette holder carriage is never used. It is used
together with the end sensor of the cassette holder to detect the right position of the secondary
aperture when in cephalostatic mode.
Primary aperture motor
This motor is at the inner side of the tube head fixed to the collimator. It changes the primary
aperture to the selected one. The drive to this stepper motor is delivered by the generator proc-
essor.
The positioning of the primary apertures must be very accurate and is done with an accuracy of
1/100mm. To achieve this the final adjustment in the alignment procedure must be performed in
the same direction than they are driven when the apertures are changed (+). To avoid the inac-
curacies caused by clearances the apertures are always changed in this one direction and when
it is necessary to move into the other direction a calibration sequence is performed. Also when
the equipment is powered on the calibration sequence automatically takes place.
For calibration the system uses the PRIMARY POSITION DETECTOR circuit board with an infra-
red slot detector. The motor is first driven towards the sensor till it activates, after which the
speed is slowed down. The movement is continued a certain length to allow the clearances and
the sensor hysteresis. The motor is reversed with slow speed till it comes off the sensor, which is
the calibration position. The motor is driven to the desired aperture (always 0 after power on).
When driving from one position to another the system calculates the distances in between and
uses a certain speed profile to minimize the time but still reach the final position at minimum
speed for maximal accuracy. The aperture number display is blinking while the motor is running.
When not in use (not calibration sequence) the slot detector is powered off to prevent it from
aging that might affect the performance. In service mode it is though always on to make it easier
to make measurements.
2.4
Lamps
To make it as easy as possible to position the patient rightly, three positioning lights are provided.
All the lights are similar in construction and each of them has an individual fuse on the LOW
VOLTAGE POWER SUPPLY circuit board. The lamps are 6 VAC 10 W halogen bulbs with spe-
cial filament form. The light beam adjustment is done by bending the mirror rather than moving
the bulb and therefore the bulb replacement does not necessarily need the adjustment proce-
dure. It is good practice though to check the adjustments.
Summary of Contents for Proline CC
Page 2: ......
Page 42: ...Chapter C HELP ERROR MESSAGES C 12 Planmeca Proline CC panoramic x ray Technical Manual...
Page 186: ...Chapter H PARTS REPLACEMENT REPAIR H 8 Planmeca Proline CC panoramic x ray Technical Manual...
Page 202: ...Chapter I FUNCTIONAL DESCRIPTION I 16 Planmeca Proline CC panoramic x ray Technical Manual...
Page 203: ...Planmeca Proline CC panoramic x ray J 1 Chapter Technical Manual J SCHEMATICS DIAGRAMS...
Page 204: ...Chapter J SCHEMATICS DIAGRAMS J 2 Planmeca Proline CC panoramic x ray Technical Manual...
Page 206: ......