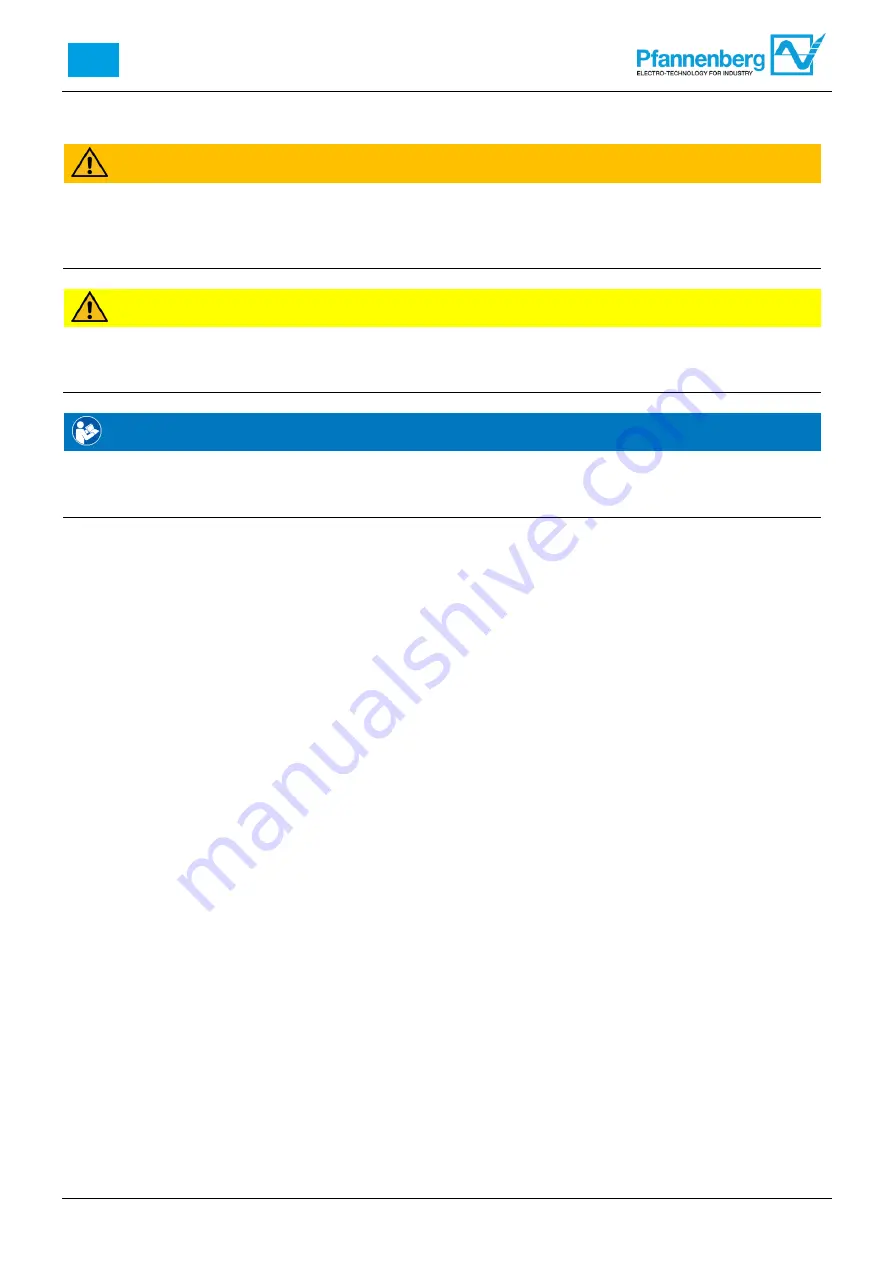
Operating and Maintenance Instructions - Chiller - Series EB 210 - EB 440
© Pfannenberg GmbH
Page 93 / 293
EN
9. Maintenance
9.1 Maintenance instructions for your safety
WARNING
Danger of accidents due to unlocked main switch
Before carrying out any maintenance work that does not require the unit to be operated, disconnect the power
supply and secure the main switch against reconnection (lock). In addition, the sign "
MAINTENANCE IN
PROGRESS
" should be affixed next to the main switch.
CAUTION
Legal problems due to improper operation of the unit
It is of utmost importance to comply with Regulation (EU) No 517/2014, regarding mandatory regular leakage-
check program, as described in chapter 2
Safety
of this document.
NOTICE
Early breakdown due to missing maintenance activities
Carrying out the tests and check program listed below will extend the lifespan of the equipment and avoid
possible breakdowns.
Check mechanical working of the compressor. Control the absence of metallic vibrations and not too high noises
and temperatures on the compressor head during running to verify its regular working.
Check the operation of the fan.
Check the electrical alarm systems and controls.
Check the filling of the tank (visual level). If the system is filled with a glycol-mix, refill only with the same mix. Only
water will reduce the concentration of glycol.
Check that pressure, flow rate and temperature values of the hydraulic circuit are in the limits indicated on the type
label or in chapter
Technical data
.
If the chiller is equipped with an air filter, the filter has to be changed/cleaned monthly, or, if required in a shorter
time interval.
Do a visual inspection of the condenser monthly on the external side, to see whether it is clean or not. The fins of
the condenser must not have any dust deposits or residual products or sludges on their surface.
The condenser must be cleaned in monthly intervals, or, if required in shorter time intervals.
If the chiller is equipped with a filter on the hydraulic side, the filter has to be checked/cleaned monthly, or if
required, in a shorter time interval.
To allow best operating conditions it’s recommended to change the coolant mixture depending on the glycol
concentration in the following intervals:
o
every year for a glycol concentration of 20 %
o
every 2 years for a glycol concentration of 30 % or 50 %
Longer standstill of the unit requires draining of the tank and the entire hydraulic circuit. Open the ball valve (or the
plug) at the end of the draining hose to drain the circuit. When the drain operation is finished close again.
For a new installation, it is recommended to empty the hydraulic circuit. Please, refer to chapters
Installation
and
Commissioning
for the lifting of the unit, the connection and the start up.
It is recommended to check safety discharge valve (in the refrigerant circuit, where installed) every 24/36 months.
Leakages and/or visible scale may suggest potential malfunction.
Please familiarize with chapter
Electrical and mechanical components
to identify the main components of the
unit.
No device with internal volume greater than 25 l is installed on the refrigeration circuit, thus no further inspection
from notified bodies is required according to D.M. nr.309
– December the 1
st
2004.
The customer is obliged to comply with all additional local requirements.
Summary of Contents for EB 210
Page 97: ...DE Betriebs Wartungsanleitung Chiller Serie EB 210 EB 440 Version 1 0 Juni 2019...
Page 196: ...ES Manual de uso y mantenimiento Refrigerador Serie EB 210 EB 440 Versi n 1 0 Junio 2019...
Page 244: ...RU EB 210 EB 440 1 0 2019...
Page 245: ...Pfannenberg Pfannenberg Pfannenberg...
Page 248: ...EB 210 EB 440 Pfannenberg GmbH Page 248 293 RU 1 1 1 1 2 1 3 c...
Page 249: ...EB 210 EB 440 Pfannenberg GmbH Page 249 293 RU 1 4...
Page 251: ...EB 210 EB 440 Pfannenberg GmbH Page 251 293 RU 2 1...
Page 252: ...EB 210 EB 440 Pfannenberg GmbH Page 252 293 RU 2 2 2 2 1 2 3 2006 42 CE...
Page 253: ...EB 210 EB 440 Pfannenberg GmbH Page 253 293 RU 2014 68 UE I...
Page 254: ...EB 210 EB 440 Pfannenberg GmbH Page 254 293 RU 3 Pfannenberg 3 1 3 2 1 2 3 4 5 6 1 2 2 3 4 5...
Page 255: ...EB 210 EB 440 Pfannenberg GmbH Page 255 293 RU 3 3 3 3 1 3 3 2...
Page 256: ...EB 210 EB 440 Pfannenberg GmbH Page 256 293 RU 3 3 3 3 3 4 3 3 5 3 3 6...
Page 257: ...EB 210 EB 440 Pfannenberg GmbH Page 257 293 RU 3 4...
Page 259: ...EB 210 EB 440 Pfannenberg GmbH Page 259 293 RU...
Page 263: ...EB 210 EB 440 Pfannenberg GmbH Page 263 293 RU 4 4 3...
Page 264: ...EB 210 EB 440 Pfannenberg GmbH Page 264 293 RU 4 5 4 5 1 EB 210 4 5 2 EB 260...
Page 265: ...EB 210 EB 440 Pfannenberg GmbH Page 265 293 RU 4 5 3 EB 310 4 5 4 EB 360...
Page 266: ...EB 210 EB 440 Pfannenberg GmbH Page 266 293 RU 4 5 5 EB 410 4 5 6 EB 440...
Page 268: ...EB 210 EB 440 Pfannenberg GmbH Page 268 293 RU 4 7 4 7 1 EB 210 260...
Page 269: ...EB 210 EB 440 Pfannenberg GmbH Page 269 293 RU 4 7 2 EB 310 440...
Page 272: ...EB 210 EB 440 Pfannenberg GmbH Page 272 293 RU 5 5 1 5 2...
Page 274: ...EB 210 EB 440 Pfannenberg GmbH Page 274 293 RU 33 7 5 mm S355JR 1 0045 5 3...
Page 279: ...EB 210 EB 440 Pfannenberg GmbH Page 279 293 RU 6 30...
Page 280: ...EB 210 EB 440 Pfannenberg GmbH Page 280 293 RU Harting...
Page 282: ...EB 210 EB 440 Pfannenberg GmbH Page 282 293 RU 7 PFANNENBERG PFANNENBERG...
Page 283: ...EB 210 EB 440 Pfannenberg GmbH Page 283 293 RU 6 1 1...
Page 284: ...EB 210 EB 440 Pfannenberg GmbH Page 284 293 RU 6 2 10 Eliwell SMP 6 3 7 7 1 7 2 30 7 3...
Page 285: ...EB 210 EB 440 Pfannenberg GmbH Page 285 293 RU 8 30...
Page 286: ...EB 210 EB 440 Pfannenberg GmbH Page 286 293 RU TD TD Pfannenberg 2 1 Klixon...
Page 287: ...EB 210 EB 440 Pfannenberg GmbH Page 287 293 RU...
Page 289: ...EB 210 EB 440 Pfannenberg GmbH Page 289 293 RU 9 2 1 2 3 4 5 6 7 8 9 10 11 12 13 14 15 16 17...
Page 290: ...EB 210 EB 440 Pfannenberg GmbH Page 290 293 RU 10 10 1 10 2 Pfannenberg...