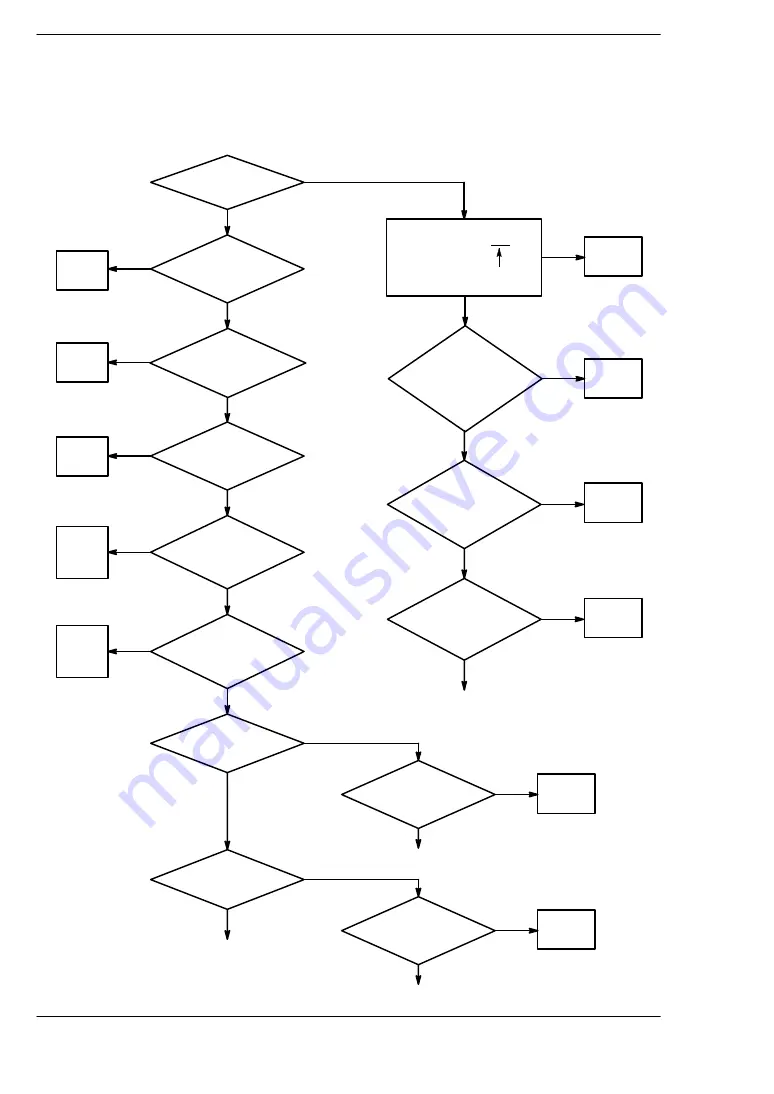
High
−
speed Counter/Pulse Output/ PWM Output
FP0
9
−
32
9.4
Pulse Output Function
Troubleshooting flowchart if a pulse is not output when instruction F168
(SPD1) executed
No
Yes
No
Yes
Remedy
problem
No
Yes
Remedy
problem
No
Yes
Remedy
problem
No
Yes
Modify
elapsed
value.
No
Yes
No
Yes
No
Remedy
problem
No
Yes
Remedy
problem
No
Yes
Remedy
problem
Yes
No
Remedy
problem
Yes
No
Remedy
problem
Yes
Error occurs
Special internal
relay R903A or R903B
is already on.
Not set to K0 or K1.
[F168 SPD1,
ϕ
, K
ϕ
]
Control clear
flag for special data regis-
ter DT9052/DT90052
is on.
First word
of data table is not set
to incremental (0), absolute
(1), or home
return (2).
HSC CH0 or CH1
is set to system
register 400.
Second word of
data table is set to 40 <
or = initial speed < or =
maximum
speed.
Modify
elapsed
value.
Elapsed value
tried to output pulse in
forward direction at
H7FFFFF.
Fifth word of data
table is set to HFF8000 < or =
target value < or =
H7FFFFF.
Elapsed value
tried to output pulse in
reverse direction at
HFF8000.
Please contact your dealer.
Set to home
return mode
Home input is
already used by
interrupt or HSC.
Set to absolute
mode
Please contact your dealer.
Please contact your dealer.
Yes
Remedy
problem
No
Yes
Please contact your dealer.
Absolute mode
setting is target value
= elapsed
value.
No
Summary of Contents for FP0 Series
Page 14: ...Table of Contents FP0 xii ...
Page 16: ...Overview FP0 1 2 ...
Page 82: ...S LINK Control Unit FP0 4 2 ...
Page 95: ...Chapter 5 I O Allocation 5 1 I O Number 5 3 5 2 Control Unit 5 4 5 3 Expansion I O Unit 5 5 ...
Page 96: ...I O Allocation FP0 5 2 ...
Page 100: ...I O Allocation FP0 5 6 5 3 Expansion I O Unit ...
Page 102: ...Installation FP0 6 2 ...
Page 112: ...Installation FP0 6 12 6 5 Installation Using FP0 Flat Type Mounting Plate ...
Page 114: ...Wiring FP0 7 2 ...
Page 198: ...High speed Counter Pulse Output PWM Output FP0 9 34 9 5 PWM Output Function ...
Page 200: ...General use Serial Communications FP0 10 2 ...
Page 210: ...Self Diagnostic and Troubleshooting FP0 11 2 ...
Page 220: ...Specifications FP0 12 2 ...
Page 234: ...Dimensions FP0 13 2 ...
Page 243: ...Chapter 14 Appendix ...
Page 380: ...14 138 14 7 ASCII Codes ...