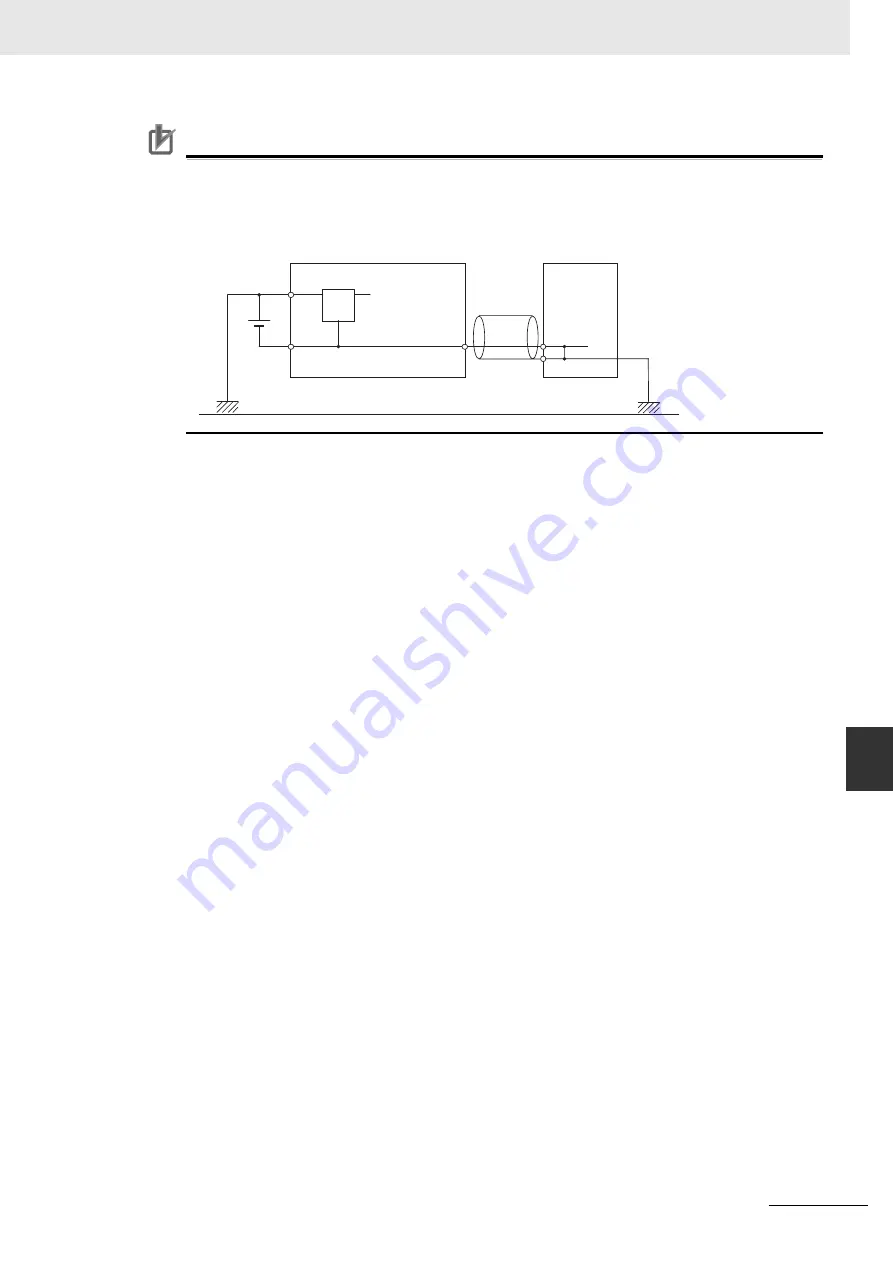
17-15
17 Analog Input/Output Option Board
CP2E CPU Unit Software User’s Manual(W614)
17-6 A
n
alo
g
Outp
ut Op
tio
n
Bo
ar
d
17
17-6-
3
Wir
ing
Precautions for Correct Use
Precautions for Correct Use
When connecting the analog option board to an outside analog device, either ground the 0 V
side of the PLC
’
s external power supply or do not ground the PLC
’
s external power supply at all.
Otherwise the PLC
’
s external power supply may be shorted depending on the connection meth-
ods of the outside analog device. DO NOT ground the 24 V side of the PLC
’
s external power
supply, as shown in the following diagram.
24 V
0 V
0 V
N
on-ins
u
lated DC po
w
er s
u
pply
0 V
Analog De
v
ice
FG
FG
T
w
isted-pair
ca
b
le
CPU Unit + Analog Option Board
Summary of Contents for SYSMAC CP Series
Page 3: ......
Page 32: ...1 Overview 1 4 CP2E CPU Unit Software User s Manual W614 ...
Page 44: ...3 CPU Unit Operation 3 8 CP2E CPU Unit Software User s Manual W614 ...
Page 116: ...6 I O Allocation 6 8 CP2E CPU Unit Software User s Manual W614 ...
Page 144: ...7 PLC Setup 7 28 CP2E CPU Unit Software User s Manual W614 ...
Page 170: ...10 Interrupts 10 14 CP2E CPU Unit Software User s Manual W614 ...
Page 200: ...11 High speed Counters 11 30 CP2E CPU Unit Software User s Manual W614 ...
Page 272: ...12 Pulse Outputs 12 72 CP2E CPU Unit Software User s Manual W614 ...
Page 278: ...13 PWM Outputs 13 6 CP2E CPU Unit Software User s Manual W614 ...
Page 460: ...18 Programming Device Operations 18 28 CP2E CPU Unit Software User s Manual W614 ...
Page 576: ...Revision 2 CP2E CPU Unit Software User s Manual W614 ...
Page 577: ......