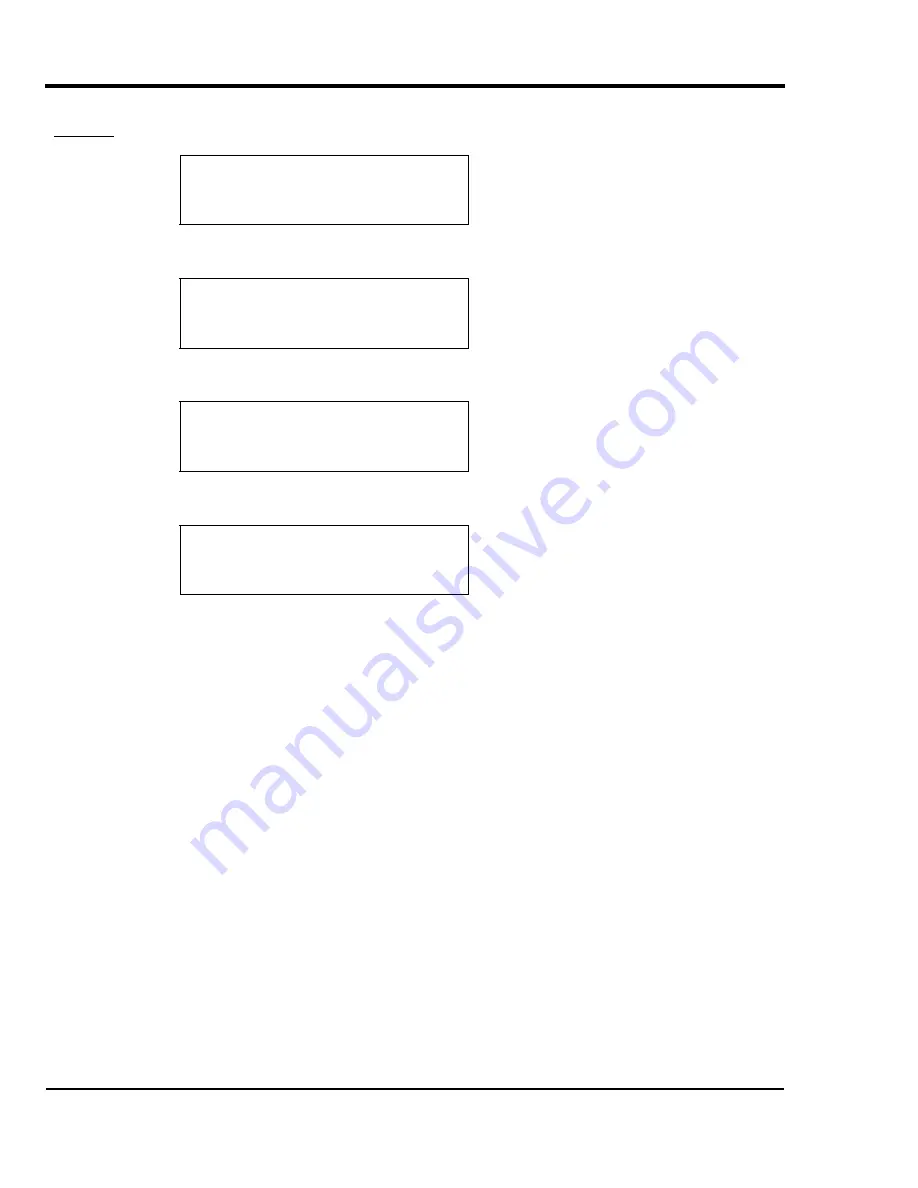
Falcon II Outdoor series printers – Maintenance Manual
180
AP-74065, Rev. 1.0, 21/11/03
Step 4 :
Input the measurement as the parameter of the P_REAR sensor position.
* Rear Sensor *
Set Cutting Paper
↓
Set media
* Rear Sensor *
Paper Initial
If media is not set
↓
End media initialization
* Rear Sensor *
Paper Width
297.0 mm Check media width
↓
ENTER
* Rear Sensor *
Rear Sensor
7.0 – 27.0 +
17.0 mm -