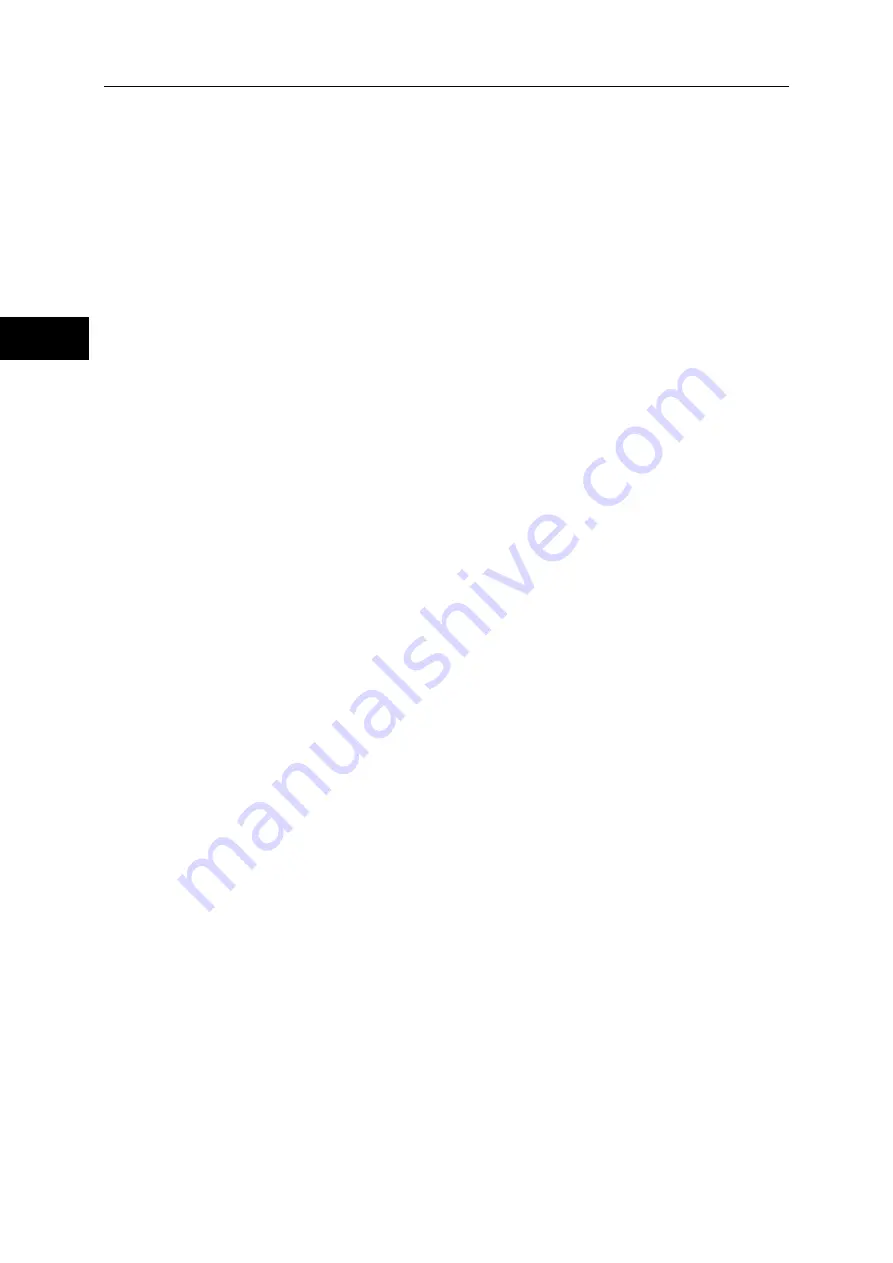
4-2 17-bit absolute encoder
4-7
11
10
9
4
7
6
5
4
3
2
1
Encoder
s
yst
em
3
Setting the parameters
Set [SP61: Encoder monitor output pulses] and [SP67: Output shaft divide function setting*]
according to the method used, then turn the power OFF, then ON again to put the parameter
into effect. For details, refer to [SP61: Encoder monitor output pulses] (P8-11), [SP67: Output
shaft divide function setting] (P8-13), and [Output signal pulses] (P4-11).
*: If you change the setting, the origin needs to be set again. Be sure to change the value
before setting the origin.
4
Origin setting
Set the origin in order to link the actuator driver and the mechanical origin.
1. Using as an absolute encoder (SP66=0)
For the origin setting method, refer to [Origin setting] (P4-8).
2. Using as an incremental encoder (SP66=1)
In order to establish the relationship between the actuator driver and the machine origin, use the
return-to-origin function on the host controller to execute a return to origin and manage the
coordinates with the host controller.
When the control power supply is turned ON
When the driver has been replaced
When the actuator has been replaced
Summary of Contents for H A - 800A
Page 60: ...2 6 Wiring the host device 2 21 4 2 2 1 9 8 7 6 9 8 Installation wiring...
Page 86: ...3 6 Normal operation 3 25 4 3 3 1 9 8 7 6 9 8 Startup...
Page 152: ...5 8 Connection example in control mode 5 35 1 2 3 4 5 6 7 8 9 10 11 Appe I O signals...
Page 166: ...6 1 Operating display panel 6 13 11 10 9 4 7 6 5 4 3 2 1 Panel display and operation...
Page 206: ...8 2 Function extension parameter 8 17 1 2 3 4 5 6 7 8 9 10 11 Appe System parameter mode...
Page 222: ...9 2 Details of test mode 9 15 1 2 3 4 5 6 7 8 9 Test mode...
Page 270: ...11 2 Warnings and remedial actions 11 17 1 2 3 4 5 6 7 8 9 10 11 Appe Troubleshooting...
Page 271: ...1 16 Chapter 12 Option Options you can purchase as necessary are explained 12 1 Option 12 1...
Page 276: ...12 1 Option 12 5 1 2 3 4 5 6 7 8 12 Option...