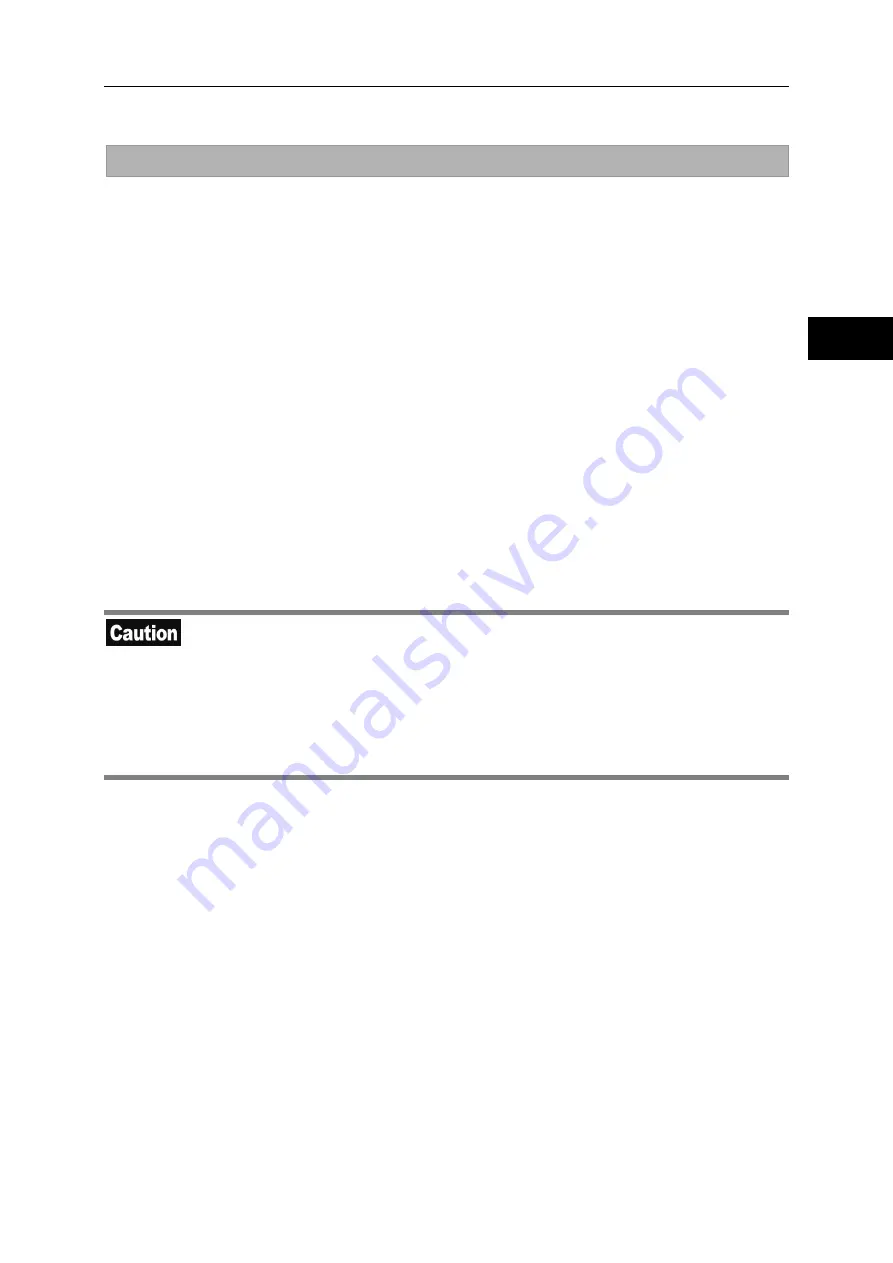
4-2 17-bit absolute encoder
4-8
11
10
9
4
7
6
5
4
3
2
1
Encoder
s
yst
em
Origin setting
Perform the following to set the origin (read the current value data at the mechanical origin position) in
order to link the actuator driver and the mechanical origin.
(1) Move the actuator to the target mechanical origin position via a JOG operation, manually, or using
the various host controller functions.
(2) Execute T08 (multi revolution clear) by operating the HA-800A panel, and reconnect the HA-800A
power supply.
(3) Perform any of the following to read the current absolute encoder value.
(a) Use the current value data output at the pins CN2-40, 41.From the pins CN2-40 and 41,
receive the absolute encoder’s current value with the host controller and check the data.For
details, refer to [Data output] (P4-9).
(b) (b) Use the HA-800 driver monitor software PSF-800.Check the PSF-800 status display
value monitor feedback pulses. For details, refer to [Chapter 10 Communication software].
(c) (c) Use the status display panel for the HA-800A driver. You can check the current encoder
value from the d05 feedback pulse (Low) and d06 feedback pulse (High) shown on the
display panel in the status display mode. For details, refer to [d05, 06: Feedback pulses
display] (P7-5).
(4) Manage the coordinates (set the origin) with the host controller with the read out current value of
the absolute encoder as the origin data.
(5) In operations after setting the origin, use the CN2-40, 41 current value data output to acquire the
current value data and manage the coordinates with the host controller. For details, refer to [Data
output] (P4-9).
*: The current HA-800A position display will not usually indicate zero at the mechanical origin.
Do not turn the actuator until the Step (2) Multi revolution clear is executed and Step
(3) Receiving/reading of the current value is completed. If the actuator moves, the
origin may become offset.
Take note that the current value of the 17-bit absolute encoder (10 digits) cannot be
fully displayed (only the last 8 digits are displayed) because only a total of 8 digits are
allocated for d05 feedback pulse (Low) and d06 feedback pulse (High) on the display
panel of the HA-800A driver.
Set the origin in the following situations even if it's not during a start-up.
The driver has been replaced
The actuator has been replaced
[AL81: System failure], [AL82: Single revolution data error] or [AL83: Multi revolution data error]
generated due to a loss of absolute position or error.
When the electronic gear (SP44/SP45, SP46/SP47) or output shaft divide function (SP67) has
been changed
Summary of Contents for H A - 800A
Page 60: ...2 6 Wiring the host device 2 21 4 2 2 1 9 8 7 6 9 8 Installation wiring...
Page 86: ...3 6 Normal operation 3 25 4 3 3 1 9 8 7 6 9 8 Startup...
Page 152: ...5 8 Connection example in control mode 5 35 1 2 3 4 5 6 7 8 9 10 11 Appe I O signals...
Page 166: ...6 1 Operating display panel 6 13 11 10 9 4 7 6 5 4 3 2 1 Panel display and operation...
Page 206: ...8 2 Function extension parameter 8 17 1 2 3 4 5 6 7 8 9 10 11 Appe System parameter mode...
Page 222: ...9 2 Details of test mode 9 15 1 2 3 4 5 6 7 8 9 Test mode...
Page 270: ...11 2 Warnings and remedial actions 11 17 1 2 3 4 5 6 7 8 9 10 11 Appe Troubleshooting...
Page 271: ...1 16 Chapter 12 Option Options you can purchase as necessary are explained 12 1 Option 12 1...
Page 276: ...12 1 Option 12 5 1 2 3 4 5 6 7 8 12 Option...