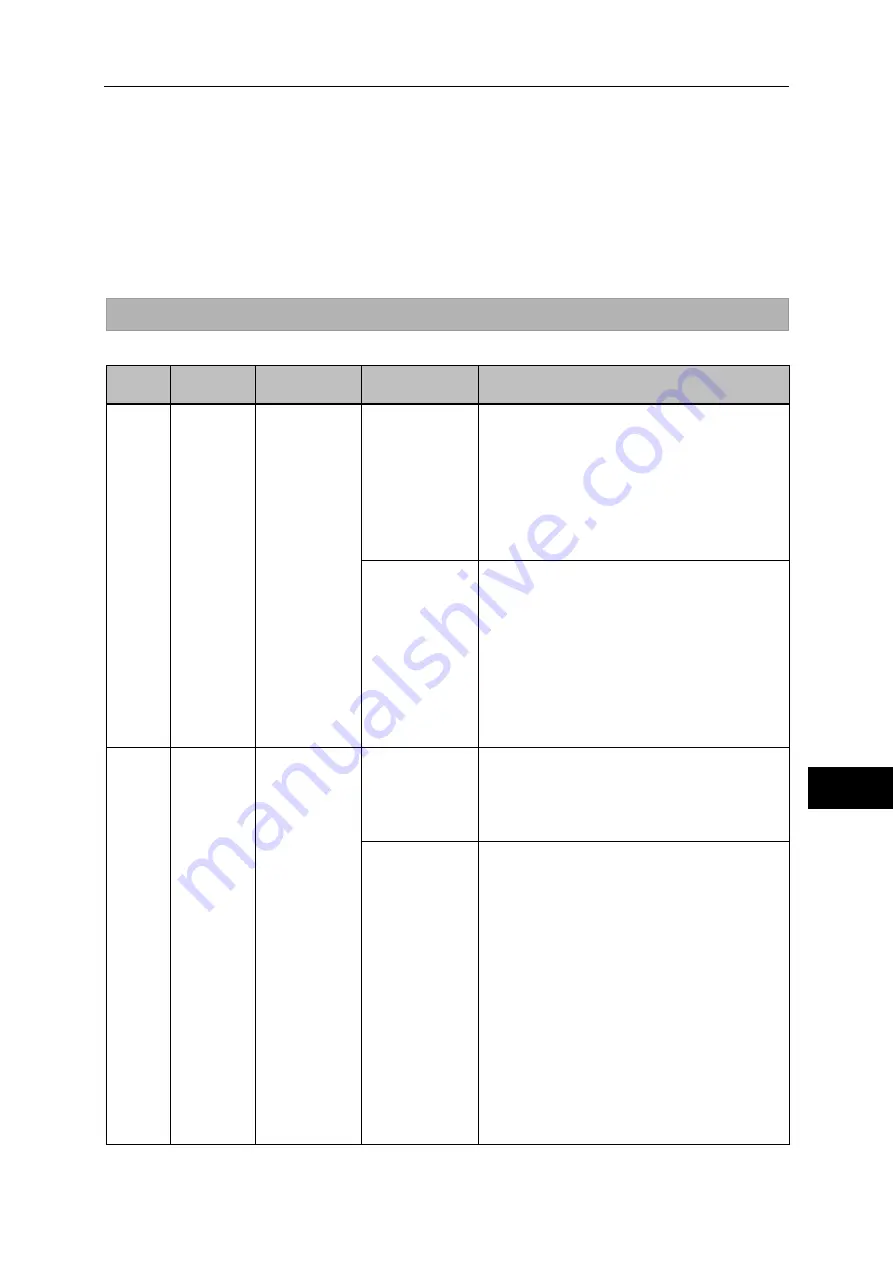
11-1 Alarms and remedial actions
11-2
2
3
4
5
6
7
8
9
10
11
Appe
Troubl
esh
oot
ing
incremental model).
*5: Once alarms are reset using the alarm clear input, the servo will not turn ON even if [CN2-2: S-ON input] is
ON. After the reset, turn OFF [CN2-2: S-ON] and then turn it ON again.
During position-controlled operation, alarms can be reset using the alarm reset signal, but the deviation will
not be cleared. If an alarm generates, clear the deviation using the clear signal and then reset the alarm using
the alarm reset signal. (If [SP48: Deviation clear upon servo-ON] is set to 1, deviation is automatically cleared
to 0 when the servo turns ON.)
*6: This alarm may generate in HA-800A-24.
*7: This alarm is not stored in the alarm history.
*8: The alarm code (3-bit code) may become indeterminable depending on the occurrence condition of alarm.
Remedial action for alarm
Remedial actions are explained for respective alarms.
Alarm
code
Alarm
name
Description
Condition at
occurrence
Action
AL01
Emergency
stop
An emergency
stop signal
was input.
The alarm
occurs when the
control circuit
power is turned
ON:
The emergency stop input is assigned to
CN2:
→ Check wiring and connector of emergency
stop input signal.
→ Check the logic and status of the emergency
stop signal.
The emergency stop input is not assigned to
CN2:
→ Set the signal logic to normally open.
The alarm
occurs during
operation:
Cancel the emergency stop signal and
reconnect the control power supply or input a
reset signal.
Wrong emergency stop signal wiring
→ Check wiring and connector of emergency
stop input signal.
Malfunction due to noise
→ Check the noise environment.
Control circuit error
→ Contact our sales office.
AL10
Overspeed The motor
rotation speed
exceeded the
maximum
rotation speed
of the motor.
The alarm
occurs when the
control circuit
power is turned
ON:
Control circuit error
→ Contact our sales office.
The alarm
occurs due to
high-speed
actuator rotation
when a rotation
command is
input:
Overshoot due to inappropriate gain
adjustment
→ Adjust [AJ00: Position loop gain], [AJ01:
Speed loop gain] and [AJ02: Speed loop
integral compensation] to match the load
condition.
Excessive command pulse frequency
→ Lower the command output pulse frequency
on the host device. Set a frequency not
exceeding the maximum rotation speed of the
actuator (r/min).
Inappropriate electronic gear setting
→ The command frequency is too large for
[SP44, 45, 46, 47: Electronic gear setting] or
[SP67: Output shaft divide function setting].
Set appropriate electronic gear. Alternatively,
modify the command frequency.
Summary of Contents for H A - 800A
Page 60: ...2 6 Wiring the host device 2 21 4 2 2 1 9 8 7 6 9 8 Installation wiring...
Page 86: ...3 6 Normal operation 3 25 4 3 3 1 9 8 7 6 9 8 Startup...
Page 152: ...5 8 Connection example in control mode 5 35 1 2 3 4 5 6 7 8 9 10 11 Appe I O signals...
Page 166: ...6 1 Operating display panel 6 13 11 10 9 4 7 6 5 4 3 2 1 Panel display and operation...
Page 206: ...8 2 Function extension parameter 8 17 1 2 3 4 5 6 7 8 9 10 11 Appe System parameter mode...
Page 222: ...9 2 Details of test mode 9 15 1 2 3 4 5 6 7 8 9 Test mode...
Page 270: ...11 2 Warnings and remedial actions 11 17 1 2 3 4 5 6 7 8 9 10 11 Appe Troubleshooting...
Page 271: ...1 16 Chapter 12 Option Options you can purchase as necessary are explained 12 1 Option 12 1...
Page 276: ...12 1 Option 12 5 1 2 3 4 5 6 7 8 12 Option...