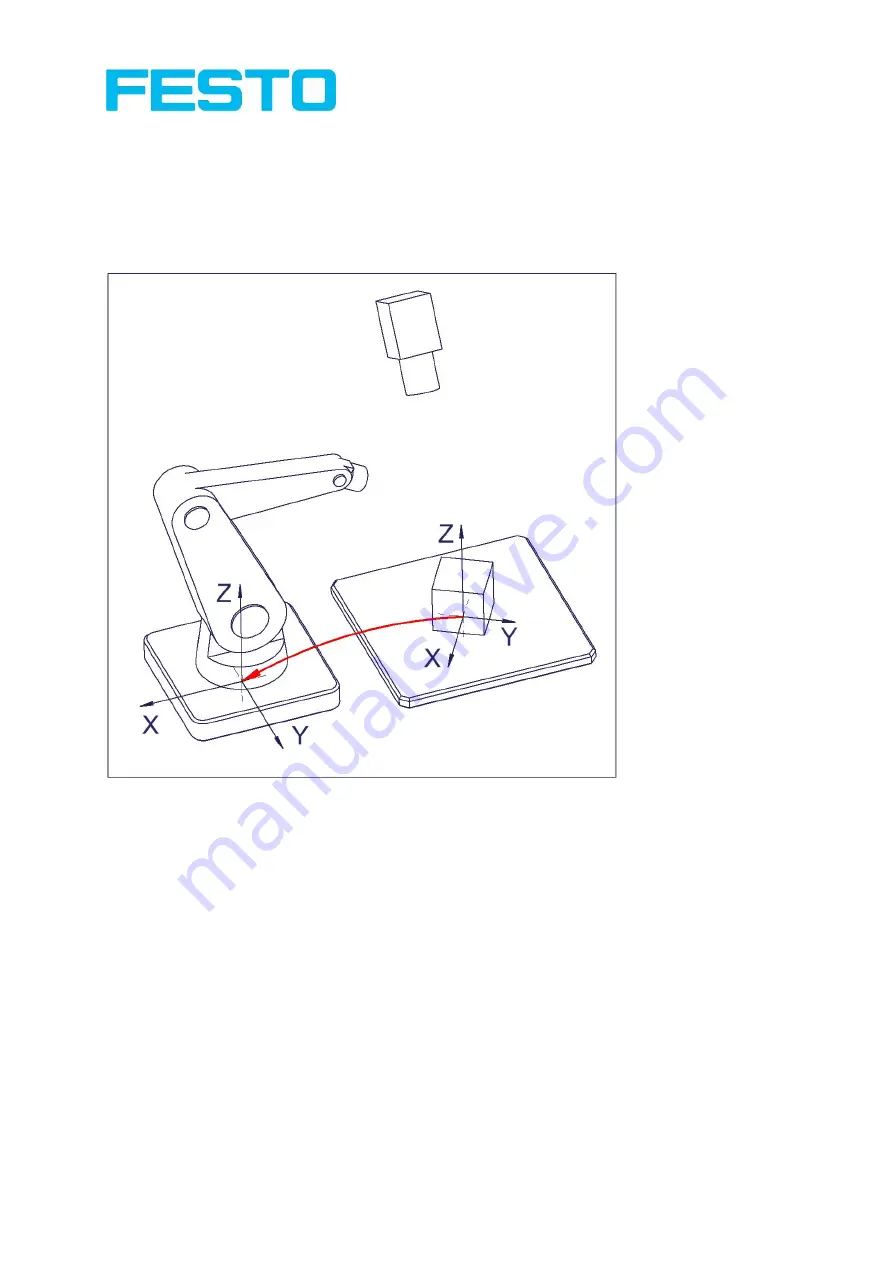
Page 68
Vision Sensor SBSI/SBSC-EN, 8062650 - 1607b - 13/09/2016
Vision Sensor Manual
Motivation / Benefit
After calibration of the sensor via point pair list the position of the part to pick is available directly in the
absolute coordinate system of the robot!
All errors like scaling, perspective and lens distortion are corrected. In robotics pick and place
applications now the robot can pick the part with the sensor provided robot coordinate values.
Fig. 55: Position of part to pick directly in robot coordinate system!
Sequence calibration via point pair list
Previously the focus and the shutter of the sensor, and the desired unit must be selected.
1. Select calibration model (-with/without correction of lens distortion), and - if necessary - set z-offset..
2. Select line 1 in list box "point pair list".
3. Place calibration part (preferably flat, symmetric, e.g. similar plain washer) at exactly known world
coordinate (e.g. with robot).
4. Place graphically the corresponding crosshair in the image (no. "n" corresponding to line "n" in point pair
list) exactly in the center of the calibration object. (if necessary zoom image)
Alternatively: use "Snap- Function", that means: right click somewhere inside the calibration part. This way
the center of gravity of the calibration part is automatically determined.
Preferably use point symmetric calibration parts, as then the center of gravity is independent from
Summary of Contents for SBSC-EN
Page 1: ......