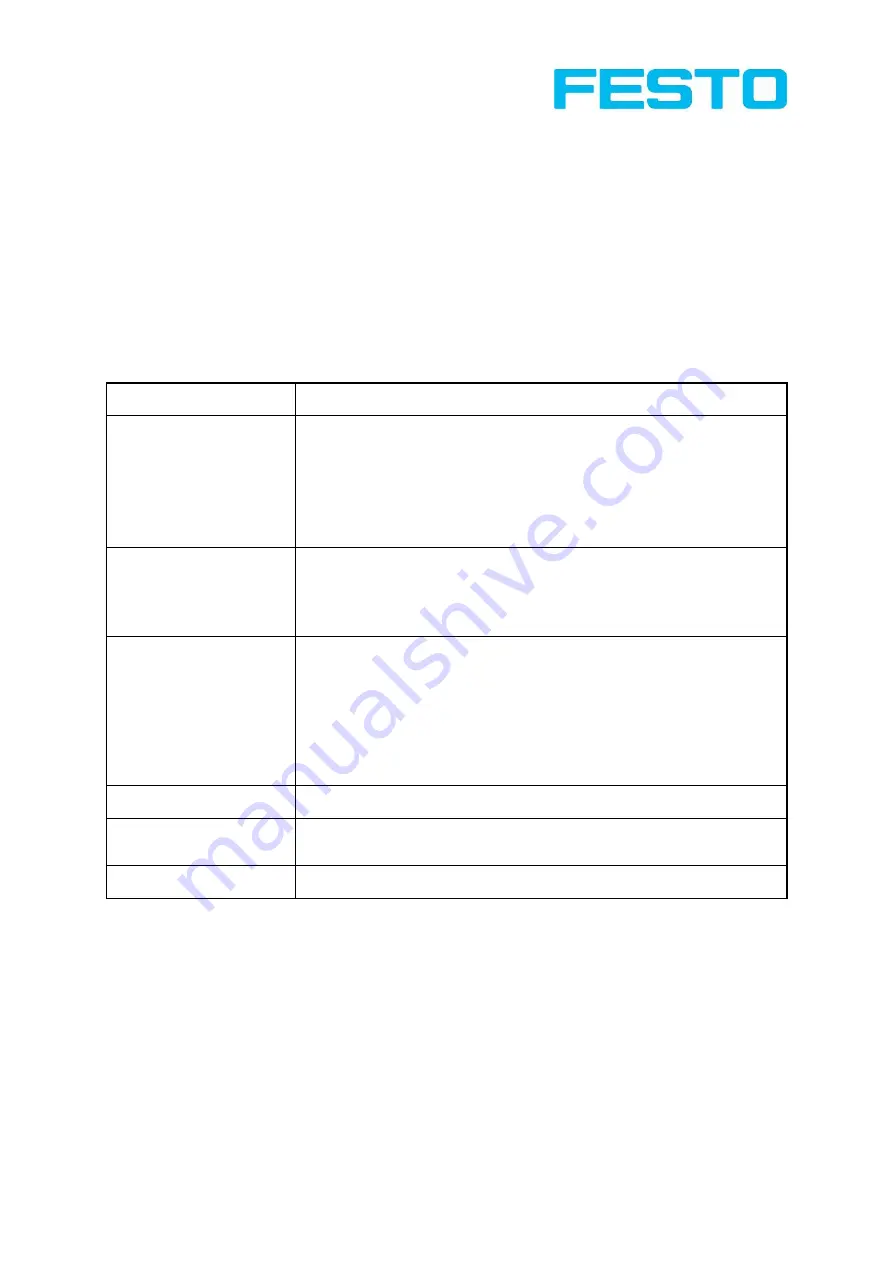
Vision Sensor SBSI/SBSC-EN, 8062650 - 1607b - 13/09/2016
Page 69
Vision Sensor Manual
orientation. With calibration parts which are not point symmetric please take care for always same
orientation. (not available with color sensors)
Result: Values of image coordinates in pixel "Image X" and "Image Y" are automatically set in line "n".
5. Now type in the corresponding, known world coordinates in the field "World X" and "World Y" ( with
e.g. robot: the values displayed in the robot controller).
6. Repeat steps 2-5 as long as the desired number of point pairs is achieved. If more lines are necessary
press "+", to delete lines press "-". (min. 6 points, recommended >10 points)
Automated calibration, see also:
Calibration via interface commands (Page 74)
Parameter Point pair list
Method
Functions
- Image X
- Image Y
Values in point list
Coordinate values in pixels (px) in the image, via exact graphical positioning
of the crosshair to the center point of the calibration part which is placed
exactly in world coordinates.
Or: use "Snap- Function", that means: right click somewhere inside the
calibration part. This way the center of gravity of the calibration part is
automatically determined (recommended).
- World X
- World Y
Values in point list
Coordinate values in selected unit (e.g. mm), by direct numerical input of
the values in the point pair list.
In case of e.g. Robotics Pick&Place this values can be taken from the robot
controller when placing the calibration part in the field of view.
Calibration parameter
Calibration model:
With or without correction of lens distortion.
Z- Offset:
(if offset is given)
Offset between calibration plane and measurement plane
Different read only parameters
of the regression calculation and error values. See also:
Calibration parameter (Page 70)
"+" / "-"
Add or delete one line / point. Delete affects the highlighted line.
Test point
A test point can be set in the image, whose world coordinate values for
test and control purposes are displayed in the Test point window.
">" / "<"
Go to next / previous step
Note:
The sensor can be mounted in any alignment / pose referred to the measurement plane. Anyway a close
to perpendicular alignment should be preferred, as this causes less distortion and this way less error
correction is needed.
The accuracy of the calibration first depends on the quality / accuracy of the point position and secondly on
the sufficient number of points. If the calibration is not accurate (yellow points) this can be improved by
better precision of position input of the single points.
This kind of calibration is suitable for standard lenses, integrated or C-mount. It´s not suitable for
telecentric lenses.
Summary of Contents for SBSC-EN
Page 1: ......