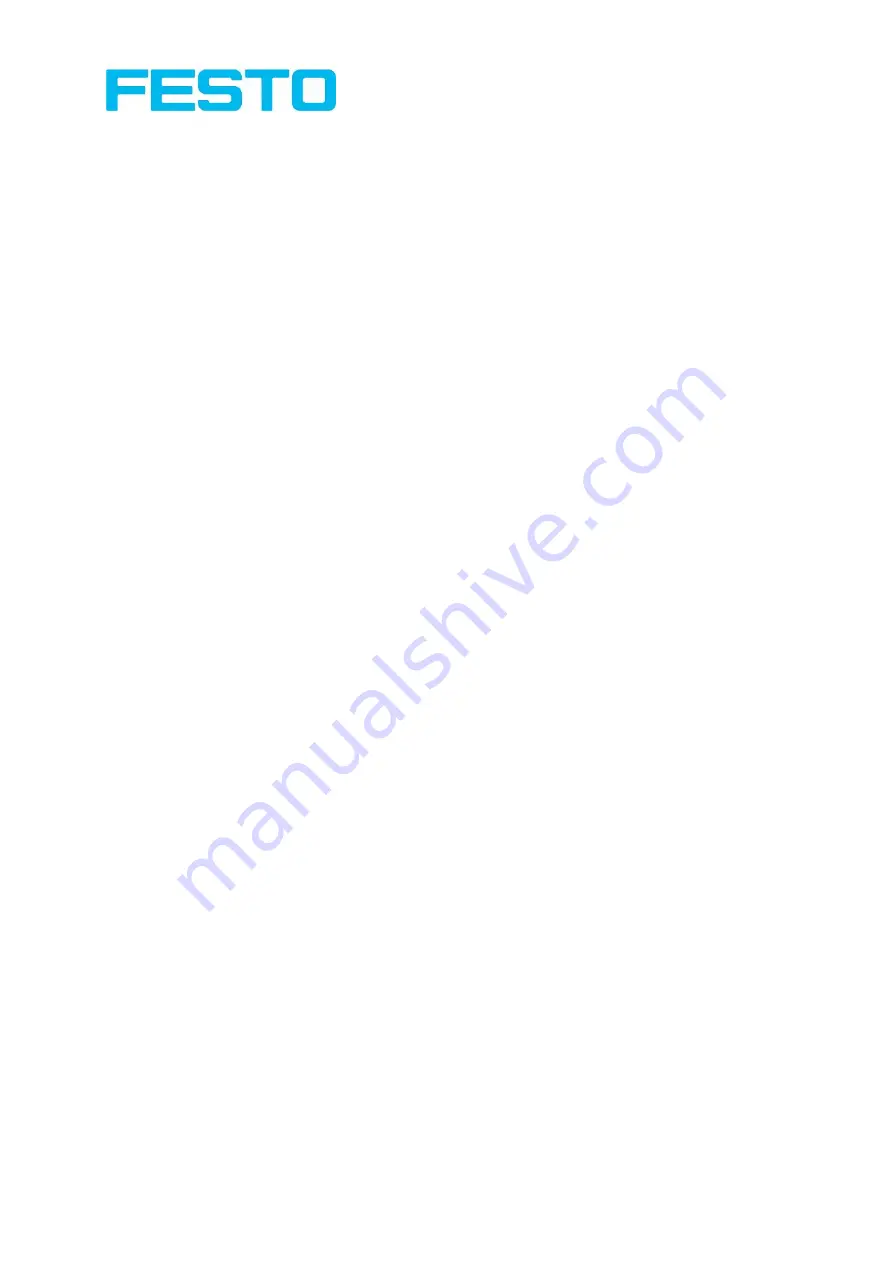
Page 74
Vision Sensor SBSI/SBSC-EN, 8062650 - 1607b - 13/09/2016
Vision Sensor Manual
Fig. 60: Delta "D" / Z- Offset = negative! In case of: Z-to top, and calibration plane higher than
measurement plane!
4.6.1.6.2.2 Calibration via interface commands
There are specific interface commands for automated creation of a point pair list, e.g. for recalibration
with drift in production process or should the mounting of sensor or robot change.
In this case the calibraiton process can automatically be executed e.g. from the robot controller.
Example:
In this example the used calibration object is a circular thin steel plate, which is detected by a
BLOB detector. This detector determines the centre of gravity of the round calibration part.
PLEASE NOTE :- For the correct function of the commands on the sensor the interface to the robot
controller (e.g. Ethernet) must be activated and the first two output values in the data string must be the
x- and y- value.
Sequence for automated (re-) calibration with interface commands via Point pair list.
Scenario:
1. Separate Job to detect calibration part (here"Job 1")
A Contour detector determines the centre of gravity of a circular calibration part.
The first and the second value transmit via the Ethernet data output are the x- and y- value of the centre
point of the round part.
Screenshot....?
2. Job which should be calibrated (here "Job2")
Currently the sensor is running Job 2. Job/Calibration/Point pair list is set in the HMI, and the sensor was
started in this job.
Sequence / flow chart
Summary of Contents for SBSC-EN
Page 1: ......