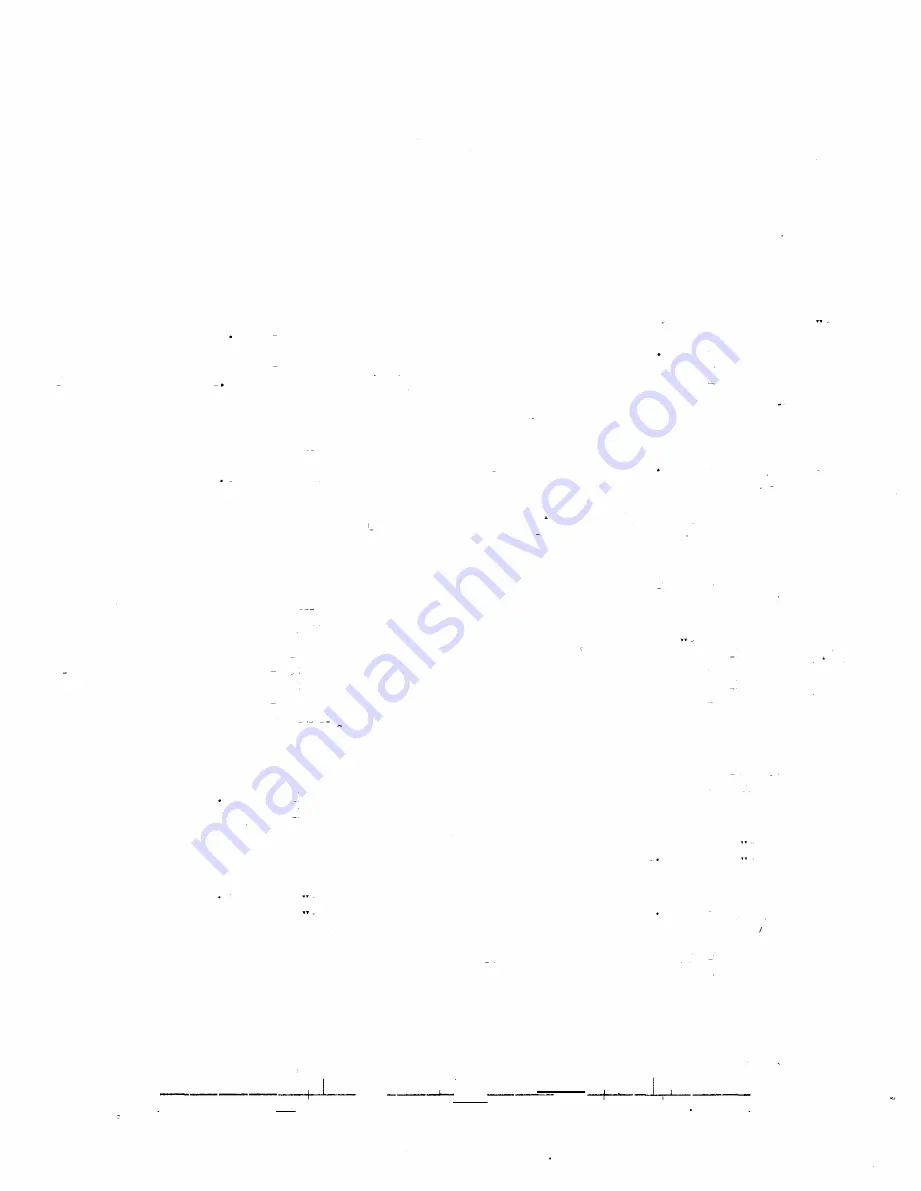
APPENDIX
METRIC CONVERSION CHART
LINEAR
inches
feet
yards
miles
inches
X 25.4
X 0.3048
X 0.9144
X 1.6093
X 2.54
AREA
inches2
X 645.16
inches2
feet2
yards2
acres
X 6.452
X 0.0929
X 0.8361
X 0.4047
miles2
X 2.590
VOLUME
inches3
inches3
inches3
quarts
gallons
feet3
feet3
fluid oz
yards3
:: millimetres
(mm)
=
metres
(rn)
:: metres
(rn)
=
kilometres
(krn)
:: centimetres
(em)
:: millimetres2
(mm
2)
:: centimetres2
(cm2)
:: metres2
(m2)
:: metres2
(m2)
:: hectares
(104 m2)
(ha)
=
kilometres2
(krn 2)
X 16387
:: millimetres3
(mm3)
X 16.387
=
centimetres3
(cm3)
X 0.01639 :: l it r e s (1)
X 0.94635
=
litres
(1)
X 3.7854
:: litres
(1)
X 28.317
:: 1itres
(1)
X 0.02832 :: metres3
(m3)
X 23.57
:: millilitres
(rnl)
X 0.7646
:: rrietr esf
(m3)
MASS
ounces
(av)
pounds
(av)
tons (2000 lb)
tons (2000 Ib)
X 28.35
=
grams
(g)
X 0.4536
:: kilograms
(kg)
X 907.18
:: kilograms
(kg)
X 0.90718::
metric
tons
(t)
FORCE
ounces
- f (av)
pounds
- f (av)
kilograms
- f
X 0.278
X 4.448
X 9.807
ACCELERATION
feet/sec2
inches/sec2
=
newtons
(N)
:: newtons
(N)
=
newtons
(N)
X 0.3048
:: metres/sec2
(m/S2)
X 0.0254
:: metres/sec2
(m/s2)
foot-pounds
calories
Btu
watt-hours
kilowatt
- hr s
ENERGY OR WORK (watt-second
- joule - newton-
metre)
X 1.3558
X 4.187
X 1055
X 3500
X 3.600
.: joules
(j)
:: joules
(j)
.: joules
(j)
=
joules
(j)
:: megajoules
(MJ)
FUEL
ECONOMY AND FUEL CONSUMPTION
miles/gal
X 0.42514 :: kilometres/litre
(krn/T)
Note:
235.2/(mi/gal)
'" litres/100km
235.2/(litres/100
krn )
=
m
i
/g
al
LIGHT
footcandles
X 10.76
:: lumens/metre2
(Im/m2)
PRESSURE
OR STRESS (newton/sq
metre
- pascal)
inches
HG (60 F)
X 3.377
:: kilopascals
(~.pa)
pounds/ sq in
X 6.895
.: kilopascals
(kPa)
inches
H20 (60' F)
X 0.2488
:: kilopascals
(kPa)
bars
X 100
:: kilopascals
(kPa)
pounds/sq
ft
X 47.88
:: pascals
(Pa)
POWER
horsepower
ft-lbf/min
TORQUE
pound-inches
pound-feet
VELOCITY
miles/hour
feet/ sec
kilometres/hr
miles/hour
X 0.746
:: kilowatts
(kW)
X 0.0226
:: watts
(W)
X 0.11299::
newton-metres
(N.m)
X 1.3558
:: newton-metres
(N·m)
X 1.6093
:: kilometres/hour
(krnz'h)
X 0.3048
:: metres/sec
(m/s)
X 0.27778::
metres/sec
(m/s)
X 0.4470
:: metres/sec
(m/s)
TEMPERATURE
32
98.6
212
F
-40
0
1
40
8U
120
160
:o~
240
280
320
"F
!
I
I
I
~I
I
I
I
!
I
I
I
!
I
I
1
!
I
!
i
I
I
I
I
I
I
)
I
1
I
I
I
'
I
"C
-40
-20
a
20
40
60
80
100
120
140
160
"c
Celsius::
0.556 ('
F
-32)
C
F ::
(1.8
C
C)
+32
Summary of Contents for 4906B 4HP 1969
Page 5: ......
Page 87: ...3 46 POWERHEAD Exploded drawing of a 7 5 hp powerhead 1956 58 with principle parts identified...
Page 88: ...CYLINDER BLOCK 3 47 HEAD GASKET RING...
Page 90: ...CYLINDER BLOCK 3 49 THERMOSTAT EXHAUST COVER The...
Page 137: ...4 46 FUEL LEVER AND LOW SPEED...
Page 153: ...4 62 FUEL Exploded view of a pressure tyoe fuel tank with major parts identified...
Page 157: ...4 66 fUEL...
Page 412: ...A 16 APPENDIX Wire Identification 33 hp with Generator 1965 67...
Page 413: ...APPENDIX A 17 o C...
Page 414: ...Wire Identification 33 hp with Generator 1969 70...
Page 415: ...APPENDIX A 19 Wire Identification 35 hp 1957 59...
Page 416: ...A 20 APPENDIX Wire Identification 40 hp Standard Shift with Generator 1960 66...
Page 417: ...APPENDIX A 21 UJ cc b Wire Identification 40 hp Standard Shift with Generator 1967 68...
Page 419: ...APPENDIX Wire Identification 40 hp Electric Shift with Generator 1961 66 A 23...
Page 420: ...A 24 APPENDIX C 00 Wire Identification 40 hp Electric Shift with Generator 1967 68...
Page 421: ...Wire Identification 40 hp Electric Shift with Generator 1969 70...
Page 422: ...NOTES NUMBERS...