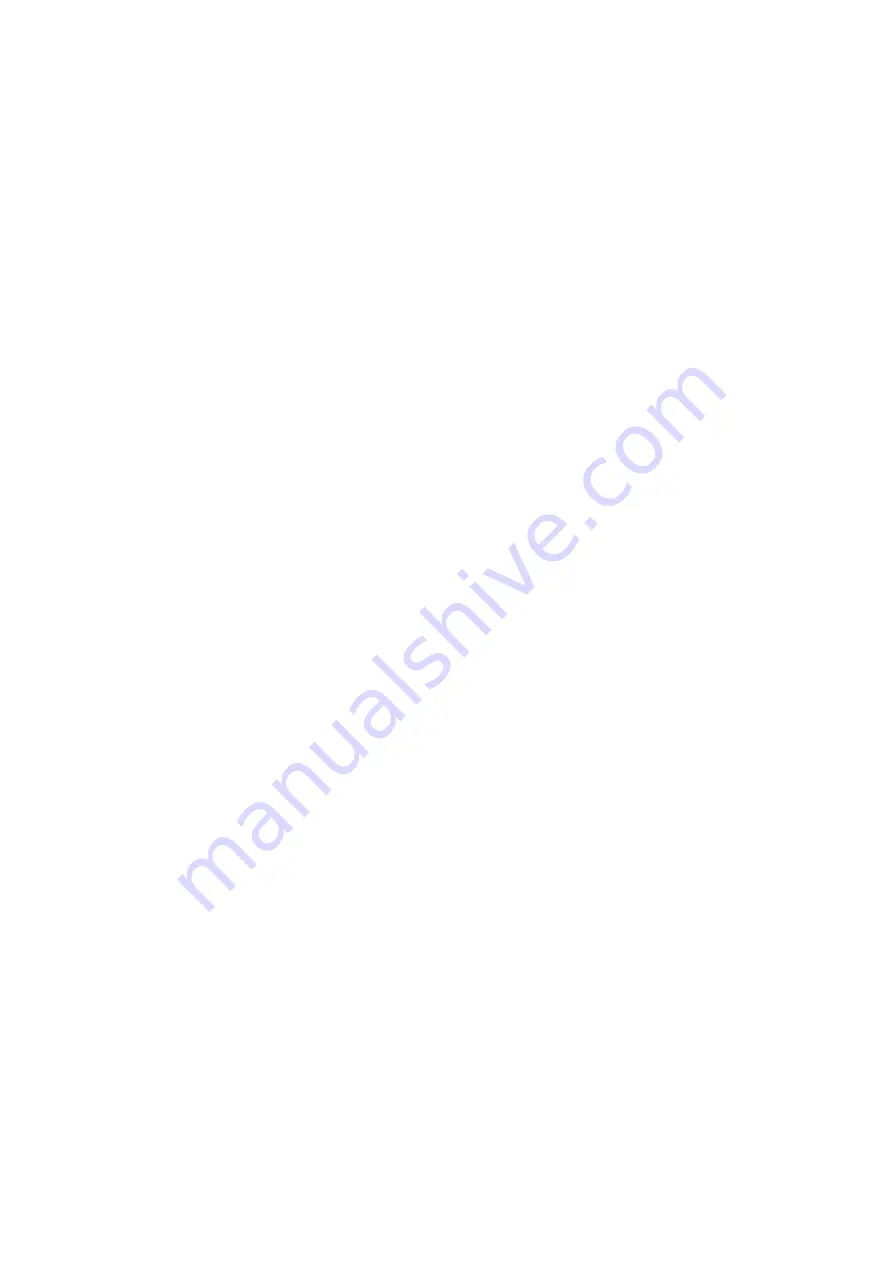
TOROMOCHO PROJECT - WEG MOTORS
TAG´s :
210-PP-001-M
210-PP-003-M 210-PP-101-M
210-PP-002-M
210-PP-004-M
- Inject about half the estimated amount of grease and run the motor at full speed for approximately a minute; switch off
the motor and inject the remaining grease. The injection of all the grease with the motor at rest could cause
penetration of a portion of the lubricant through the internal seal of the bearing case and hence into the motor.
Nipples must be clean prior to introduction of grease to avoid entry of any alien bodies into the bearing.
For lubricating, use only a manual grease gun.
BEARING LUBRICATION STEPS
1. Clean the area around the grease nipples with clean cotton fabric.
2. With the motor running, add grease with a manual grease gun until the quantity of grease recommended in Tables
9 or 10 has been applied.
3. Allow the motor to run long enough to eject all excess of grease.
4.2.4 - REPLACEMENT OF BEARINGS
The opening of a motor to replace a bearing should only be carried out by qualified personnel.
Damage to the core after the removal of the bearing cover is avoided by filling the gap between the rotor and the stator
with stiff paper of a proper thickness.
Providing suitable tooling is employed, disassembly of a bearing is not difficult (Bearing Extractor).
The extractor grips should be applied to the sidewall of the inner ring to the stripped, or to an adjacent part.
Fig. 4.2 - Bearing Extractor
Type
Polyrex
R
EM
To ensure perfect functioning and no injury to the bearing parts, it is essential that the assembly be undertaken under
conditions of complete cleanliness and by competent personnel. New bearings should not be removed from their
packages until the moment of assembly.
Prior to fitting a new bearing, ascertain that the shaft has no rough edges or signs of hammering.
During assembly bearings cannot be subjected to direct blows. The aid used to press or strike the bearing should be
applied to the inner ring.
Protect all machined parts against oxidation by applying a coating of vaseline or oil immediately after cleaning.
STRIPPING OF WINDINGS
- This step requires great care to avoid knocking and/or denting of enclosure joints and,
when removing the sealing compound from the terminal box, damage or cracking of the frame.
IMPREGNATION
- Protect all frame threads by using appropriate bolts, and terminal box support fitting with a non-
adhesive varnish (ISO 287 - ISOLASIL). Protective varnish on machined parts should be removed soon after
treating with impregnation varnish. This operation should be carried out manually without using tools.
ASSEMBLY
- Inspect all parts for defects, such as cracks, joint incrustations, damaged threads and other potential
problems. Assemble using a rubber headed mallet and a bronze bushing after ascertaining that all parts are perfect by
fitted. Bolts should be positioned with corresponding spring washers and evenly tightened.
TESTING
- Rotate the shaft by hand while examining for any drag problems on covers or fastening rings.
MOUNTING THE TERMINAL BOX
- Prior to fitting the terminal box all cable outled on the frame should be sealed with
a self estinguishible sponge compound (1st layer) and on Explosion Proof Motors an Epoxy resin (ISO 340) mixed with
ground quartz (2
nd
layer).Drying time for this mixture is two hours during which the frame should not be handled and
cable outlets should be upwards. When dry, see that the outlets and areas around the cables are perfectly sealed.
Mount the terminal box and paint the motor.
4.3- MISCELLANEOUS RECOMMENDATIONS
- Any damaged parts (cracks, pittings in machined surfaces, defective threads) must be replaced and under no
circumstances should attempt be made to recover them.
- Upon reassembling explosion proof motors IP(W) 55, the replacement of all seals is mandatory.
5 - ABNORMAL SITUATIONS DURING OPERATION
ANALYSIS OF SOME ABNORMAL SITUATIONS AND POSSIBLE CAUSES
ON ELECTRIC MOTORS:
MOTOR DOES NOT START
- Lack of voltage on motor terminals
- Low feeding voltage
- Wrong connection
- Incorrect numbering of leads
Содержание Warman 650 M200-MCR-G
Страница 1: ......
Страница 3: ......
Страница 4: ......
Страница 5: ......
Страница 6: ......
Страница 8: ......
Страница 9: ......
Страница 10: ......
Страница 11: ......
Страница 97: ...SUPLEMENTO M9 DEL MANUAL EMITIDO JUNIO DE 1998 7 Copyright WARMAN INTERNATIONAL LTD ...
Страница 125: ......
Страница 126: ......
Страница 127: ......
Страница 128: ......
Страница 129: ......
Страница 130: ......
Страница 131: ......
Страница 132: ......
Страница 133: ......
Страница 243: ......
Страница 244: ......
Страница 257: ...Operating Instructions DOUBLE FILTER type series 4 225 last updated 2007 07 rev FRE 01 B 5922 EN 04 10 1 16 ...
Страница 274: ......