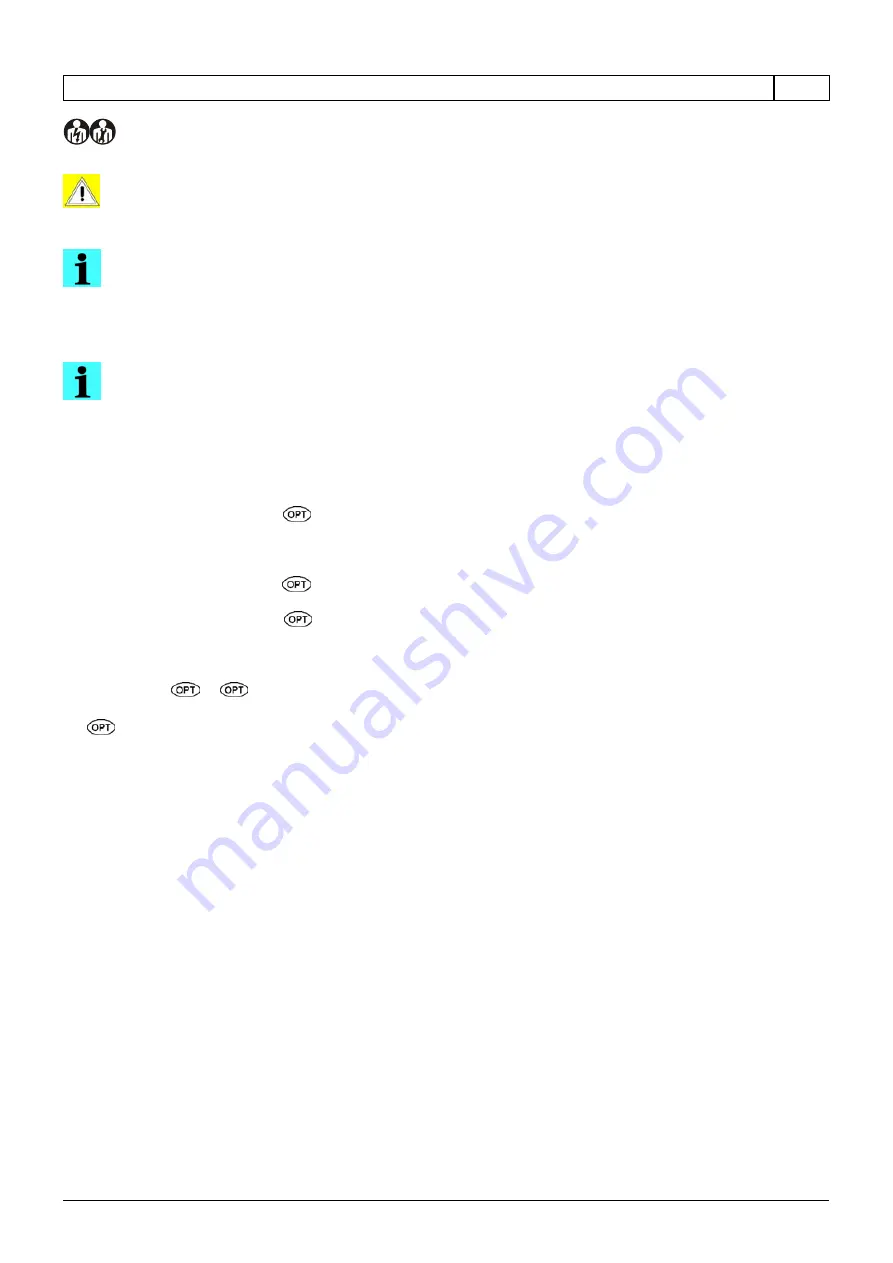
4 - INSTALLATION
EN
Pag.
52/53
- Cap.
4
THIS MANUAL IS PROPERTY OF SCM INDUSTRIA S.P.A - ANY TOTAL OR PARTIAL REPRODUCTION IS STRICTLY FORBIDDEN
4.5
CONNECTION TO THE SUCTION SYSTEM
(ev_4-5_0.0)
DANGER-WARNING:
the connection to the suction system is necessary for the right machine operation and for the
operator's safety. Always work with the suction system in operation.
NOTE-INFORMATION:
Always start the suction system and the operator assembly motor at the same time.
Connect the exhaust pipes to the suction system with hoses of proper diameter.
NOTE-INFORMATION:
we recommend that the suction sleeve is arranged out of the suction hood in order to avoid
clogging caused by chips.
The suction pipe fitting should not hinder the operator during the woodworking process.
Connect the hose to suction hood:
- (A fig. 4.5) diameter 120 mm
(Moulder hood)
- (B fig. 4.5) diameter 100 mm
(Shaping
hood)
- (C fig. 4.5) diameter 60 mm
(Saw protection)
- (D fig. 4.5) diameter 120 mm
(Surfacing planer hood)
- (E fig. 4.5) diameter 120 mm
(Saw suction)
- (F fig. 4.5) diameter 120 mm
(Mortising machine suction)
- (G fig. 4.5) diameter 120 mm
(Thicknessing planer hood)
- (H fig. 4.5) diameter 120 mm
(Tenoning shaper hood)
Clamp it with the proper metallic clip to ensure the contact between suction hood and hose.
(A , D , E , G, H
, F
) the suction system shall ensure a flow equal to 814 m
3
/h at a flow speed at least of
20 m/s - chips dry (1140 m
3
/h --> 28 m/s - chips wet).
( B
)
the suction system shall ensure a flow equal to 565 m
3
/h at a flow speed at least of
20 m/s - chips dry (792 m
3
/h --> 28 m/s - chips wet).
( C )
the suction system shall ensure a flow equal to 204 m
3
/h at a flow speed at least of
20 m/s - chips dry (285 m
3
/h --> 28 m/s - chips wet).
These values ??must be checked before starting work.
If other machines are connected to the central system, perform a test when all the suction systems are running.
Good suction operation reduces the risk of inhalation of dust.
The operator must be informed about the risks caused by exposure to dust (see Par. 3.5.1) and the factors that
influence its exposure.
Certain factors that reduce the emission of dust in the work environment are:
- regular maintenance of the tools, the machine and the extractor system
- correct speed selection (where adjustment is possible);
- type of material machined
- importance of local aspiration on each operating unit (dust collection at source)
- correct adjustment of earmuffs and deflectors
- correct use of personal protection equipment (PPE).