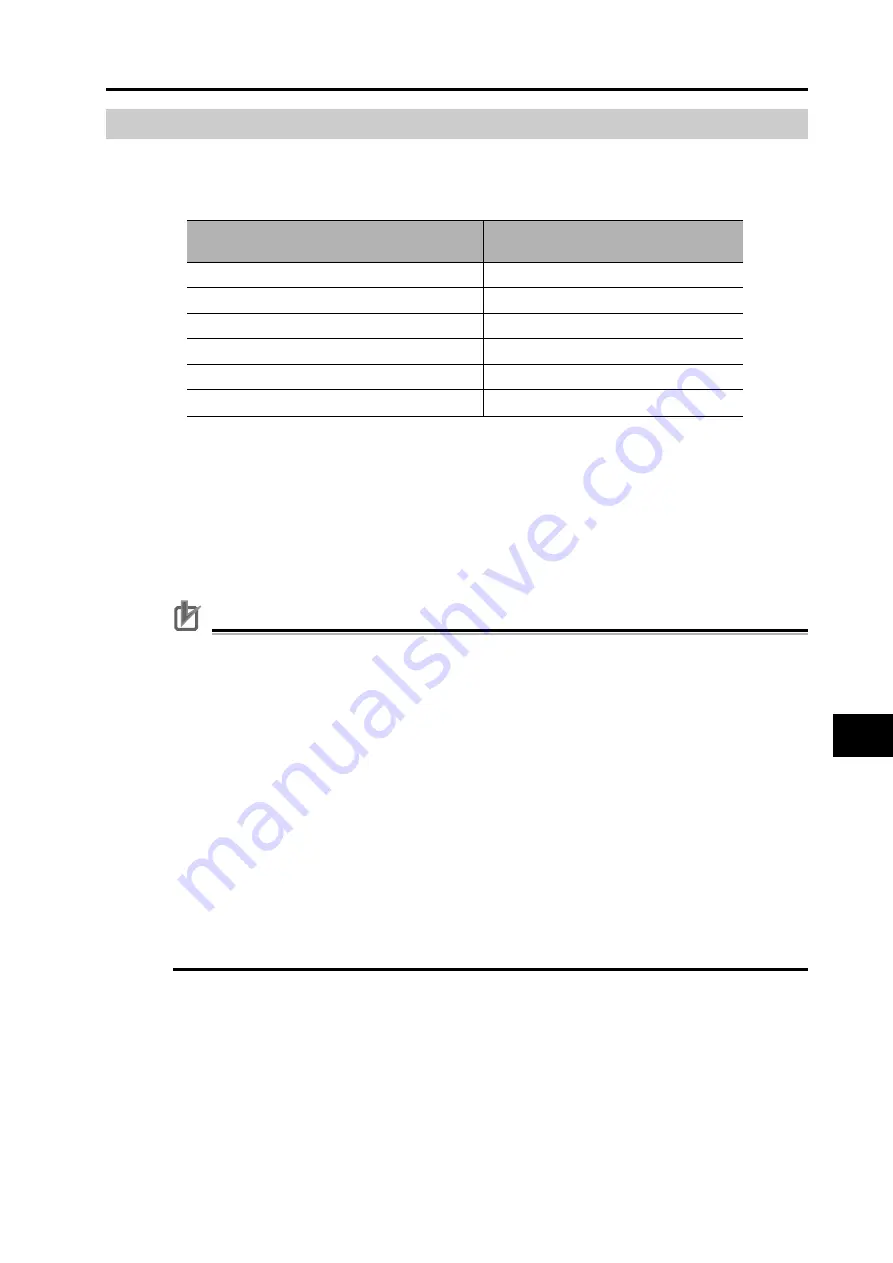
10-8
10-3 Realtime Autotuning
OMNUC G5-Series AC Servo Drives Users Manual (Built-in MECHATROLINK-II communications type)
10
Adj
u
st
me
nt
Func
tions
Setting Machine Rigidity
1. Set the Realtime Autotuning Machine Rigidity Selection (Pn003) according to the
table below.
Start from the lower machine rigidity number and check the operation.
2. Turn the servo ON and operate the machine with a normal pattern.
To increase responsiveness, increase the machine rigidity number, and check the response.
If vibration occurs, enable the adaptive filter and operate. If already enabled, adjust by lowering
the machine rigidity number.
3. If there are no issues with the operation, turn the servo OFF and set REALTIME
AUTOTUNING mode Selection (Pn002) to 0 (disabled).
In this case, the adaptive filter can remain enabled. To disable the adaptive filter, read the
frequency from the adaptive filter table number display, and set to notch filter 1 frequency.
Precautions for Correct Use
Unusual noise or vibration may occur until the load inertia is estimated or the adaptive filter
stabilizes after startup, immediately after the first servo ON, or when the Realtime Autotuning
Machine Rigidity Selection (Pn003) is increased. This is not an error if it disappears right away. If
the unusual noise or vibration, however, continues for 3 or more reciprocating operations, take the
following measures in any order you can.
• Write the parameters used during normal operation to the EEPROM.
• Lower the Realtime Autotuning Machine Rigidity Selection (Pn003).
• Manually set the notch filter.
Once unusual noise or vibration occurs, Inertia Ratio (Pn004), Torque Command Value Offset
(Pn607), Forward Direction Torque Offset (Pn608), and Reverse Direction Torque Offset (Pn609)
may have changed to an extreme value. In this case, also take the measures described above.
Out of the results of realtime autotuning, the Inertia Ratio (Pn004), Torque Command Value Offset
(Pn607), Forward Direction Torque Offset (Pn608) and Reverse Direction Torque Offset (Pn609)
are automatically saved to the EEPROM every 30 minutes. Realtime autotuning uses this saved
data as the default setting when the power supply is turned OFF and turned ON again.
The parameter is automatically set based on the Realtime Autotuning Machine Rigidity Setting
(Pn003) if realtime autotuning is enabled.
Machine configuration and drive method
Realtime Autotuning
Machine Rigidity Selection (Pn003)
Ball screw direct coupling
12 to 24
Ball screw and timing belt
8 to 20
Timing belt
4 to 16
Gears, rack and pinion drives
4 to 16
Machines with low rigidity, etc.
1 to 8
Stacker crane
Perform manual tuning.
Содержание OMNUC G5 R88D-KN series
Страница 22: ......
Страница 164: ......
Страница 228: ......
Страница 274: ......
Страница 342: ......
Страница 392: ......
Страница 432: ......
Страница 450: ......
Страница 451: ...I OMNUC G5 Series AC Servo Drives Users Manual Built in MECHATROLINK II communications type Index ...
Страница 456: ......
Страница 457: ......