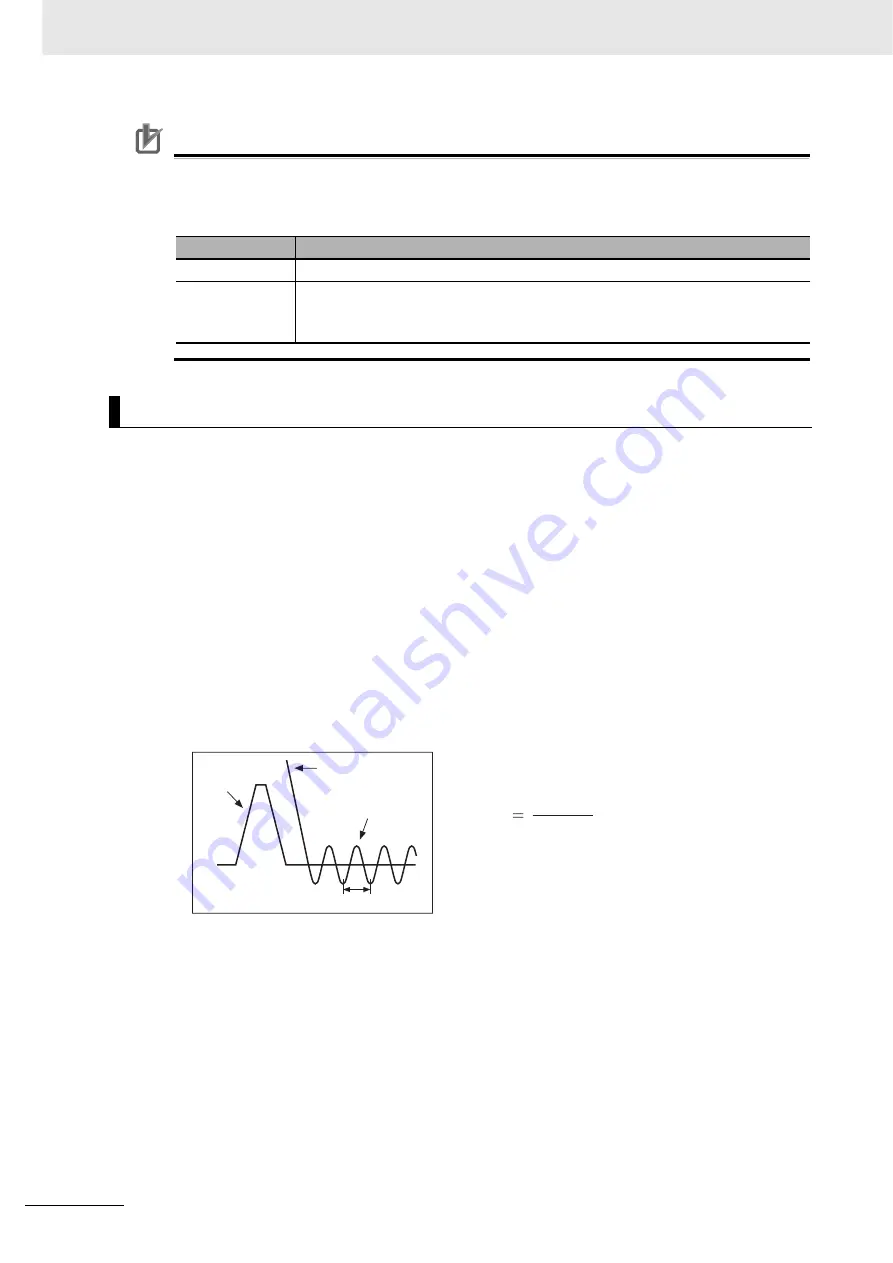
6 Applied Functions
6 - 4
OMNUC G5-series (Pulse-train Input Type) AC Servomotors and Servo Drives User’s Manual
Precautions for Correct Use
Precautions for Correct Use
• Stop operation before changing the parameters or switching with DFSEL.
• Damping control may not function properly or have a poor effect under the following
conditions.
1
Adjust the position loop gain and the speed loop gain.
Adjust Position Loop Gain (Pn100), Speed Loop Gain (Pn101), Speed Loop Integral Time
Constant (Pn102), and Torque Command Filter Time Constant (Pn104).
If no problem occurs in realtime autotuning, you can continue to use the settings.
2
Measure the damping frequency at the tip of the mechanical unit.
Measure the damping frequency by using a measurement device such as a laser displacement
sensor, servo acceleration meter, or acceleration pick-up.
Set the measured damping frequency in one of Damping Frequency 1 to Damping Frequency 4
(1: Pn214, 2: Pn216, 3: Pn218, 4: Pn220) according to the operation.
Also set the Switching Mode using Damping Filter Selection (Pn213).
If the measurement device cannot be used, use CX-Drive tracing function, and read the residual
damping frequency [Hz] from the position error waveform as shown in the following figure.
If vibration persists after setting the frequency, increase or decrease the resonance frequency to
find a proper frequency at which vibration decreases.
Item
Conditions that interfere with the effect of damping control
Control mode
• Speed control mode
Load condition
• If forces other than position commands, such as external forces, cause vibration
• If the damping frequency is outside the range of 1 to 200 Hz
• If the ratio of the resonance frequency to anti-resonance frequency is large
Operating Procedure
• The damping frequency in the figure is calculated
with the following formula:
Since the parameter unit is 0.1 Hz:
(Pn214, Pn216, Pn218, Pn220) = 10 x f
• Application example
If the damping cycle is 100 ms or 20 ms, set 100
or 500 in the parameter so that the damping
frequency becomes 10 Hz or 50 Hz.
Command
speed
Position error
Calculate the
damping frequency.
Damping cycle T
1
T [s]
f [Hz]
Содержание G5 R88D-KE Series
Страница 3: ...2 Page 2 53 For 1 000 r min Servomotors 900 W to 3 kW Current Contents Corrected Contents...
Страница 22: ...Manual Structure 18 OMNUC G5 series Pulse train Input Type AC Servomotors and Servo Drives User s Manual...
Страница 334: ...6 Applied Functions 6 52 OMNUC G5 series Pulse train Input Type AC Servomotors and Servo Drives User s Manual...
Страница 396: ...7 Parameter Details 7 62 OMNUC G5 series Pulse train Input Type AC Servomotors and Servo Drives User s Manual...
Страница 426: ...8 Operation 8 30 OMNUC G5 series Pulse train Input Type AC Servomotors and Servo Drives User s Manual...
Страница 498: ...Appendices A 32 OMNUC G5 series Pulse train Input Type AC Servomotors and Servo Drives User s Manual...
Страница 499: ...Index 1 I OMNUC G5 series Pulse train Input Type AC Servomotors and Servo Drives User s Manual Index...
Страница 504: ......
Страница 505: ......