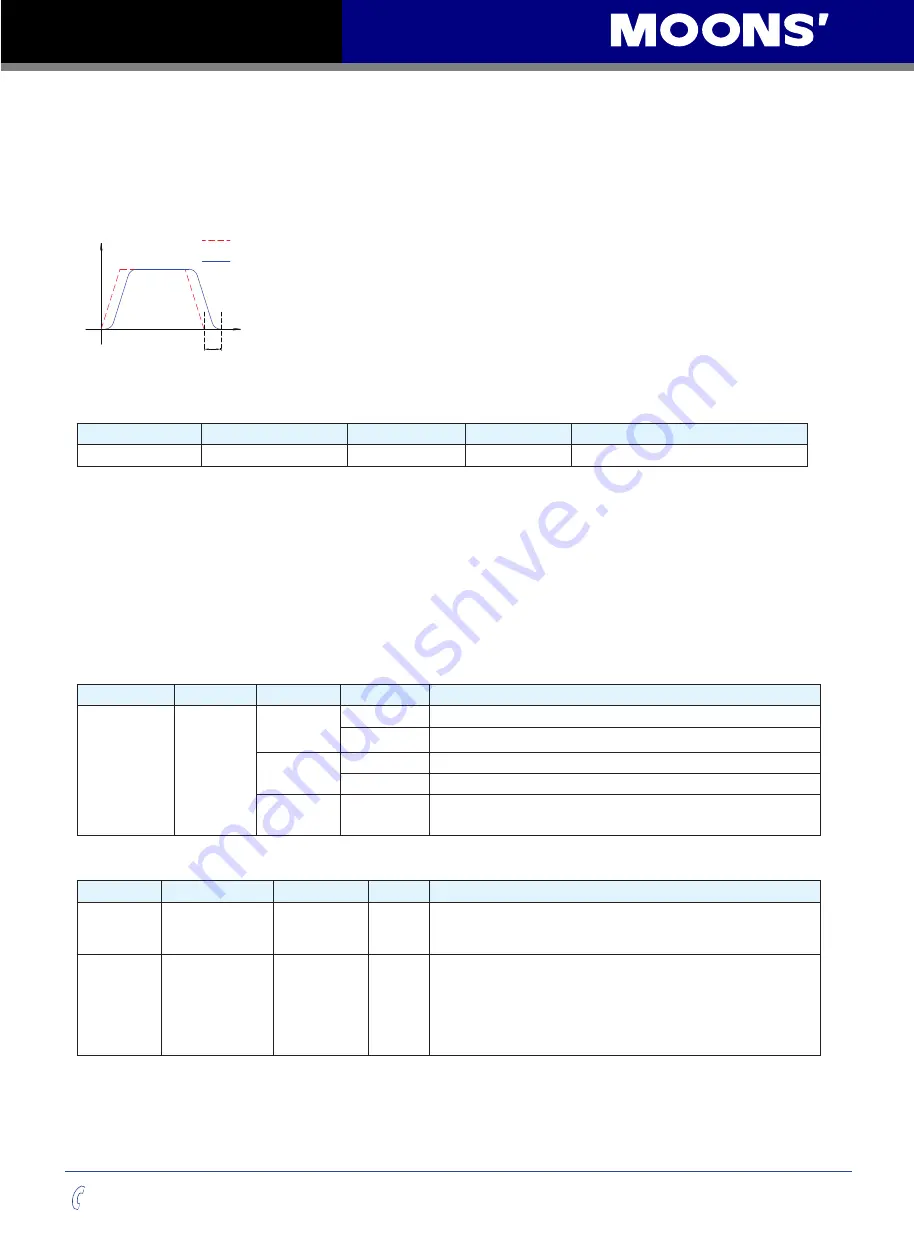
85
Rev. 1.1
2018/04
400-820-9661
M2DC Series Hardware Manual
7.2.6 Jerk Smoothing Filter
Applying this dynamic filter on speed and direction signals can significantly smoothing motor rotary
motion, and reduce wear on mechanical system components.
Jerk smoothing filter effects are as follows
:
Instruction
Time
Target Curve
Actual Curve
T
1) The smaller the value of P-07 (KJ), the stronger the effect will be.
2) Jerk smoothing filter will cause command delay time T, but it will not effect
position accuracy.
Parameter Settings
Parameter
Name
Data Range
Default
P-07 (KJ)
Jerk Filter Frequency
0~5000
5000
Set jerk smoothing filter parameter
NOTE: When set to 0, there will be no filter effect.
7.2.7 In-Position Error Output
In position mode, using the “In-Position Error” output function can help the user the define motor’s in-
position status. When the difference between the drive’s total pulses received and the motor’s actual
rotating pulse count is within the in-position error range, the drive will send out a motor in-position signal.
The forth digit of parameter P-68 (MO) defines Y6 output function; parameter P-46 (PD) defines the in-
position error range. P-47 (PE) defines in-position error time duration. If the in-position error is within the
P-46 (PD) range for more than the time duration of P-47 (PE) setting, the drive will output the motor in-
position signal.
Signal Name
PIN
P-68 (MO)
Condition
Function
Y6
Y6+ (14)
Y6- (13)
5□□□
Closed
Closed means motor is not in position
Open
Open means motor is in position
4□□□
(default)
Closed
Close means motor is in position
Open
Open means motor is not in position
3□□□
General purpose output, function disabled
Parameter Settings
Parameter
Name
Data Range
Default
P-46 (PD)
In-position error
range
0~32000
10
This parameter sets the in-position error range, when in-position
error count is less than the range, drive will indicate the motor is
in position.
P-47 (PE)
In-position
duration count
0~32000
10
If the position error is within the in-position range and lasts
longer than the duration time, the motion is considered to
be complete and the motor is in position. If the time value
is set to 100 the position error must remain in the range for
100 processor cycles before the motion is considered to be
complete. One processor cycle is 250µsec.