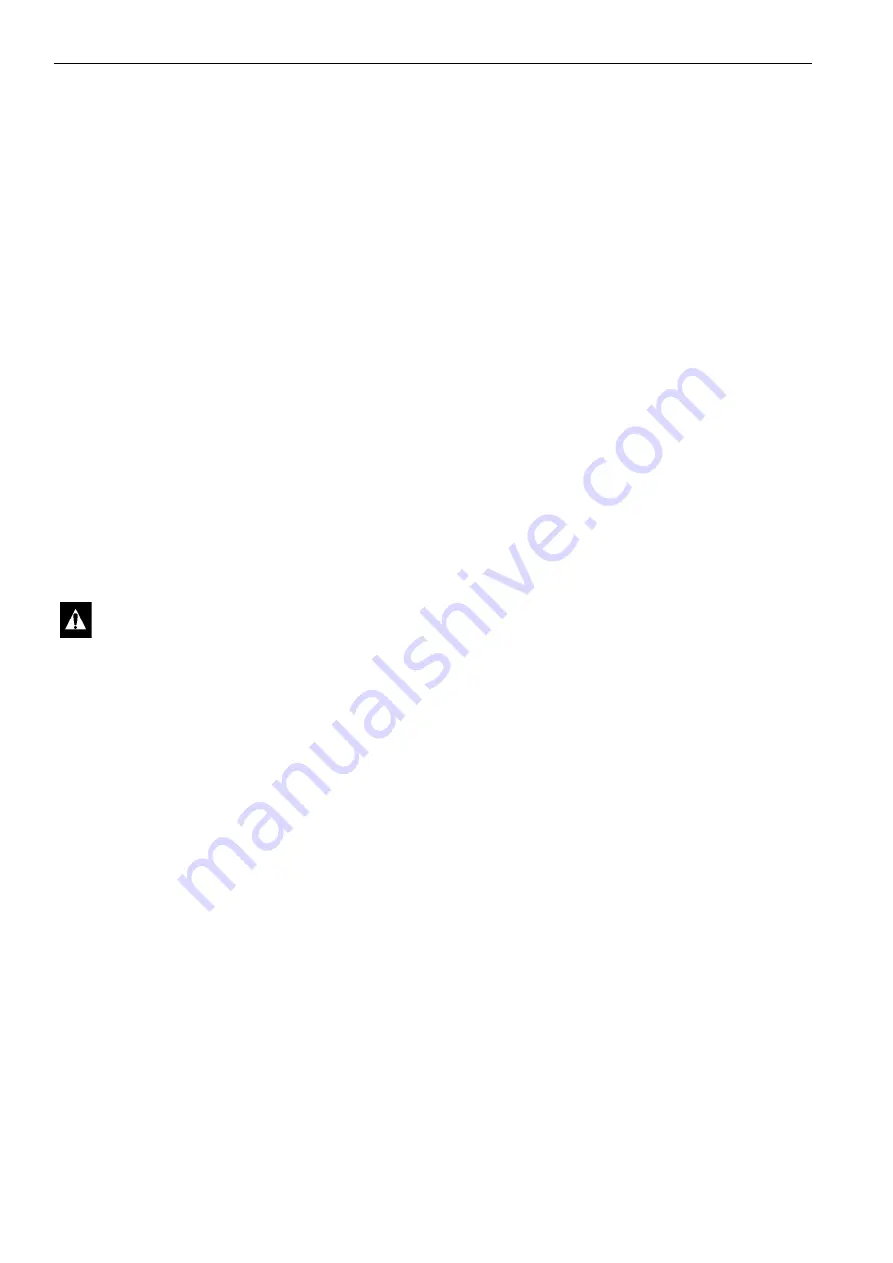
Refrigeration Maintenance and Service Operations
118
•
MOISTURE. Moisture in a system will cause metal corrosion and metal plating. It can freeze in the
expansion valve and cause intermittent operational problems. It reacts in the oil to begin acid buildup.
•
DIRT, DUST, METAL PARTICLES, OTHER FOREIGN MATERIALS. Particles of any kind left to
float through the system will cause severe damage to all close tolerance items. Do not leave a system
open to the infiltration of dirt. If you must open a system for any reason, seal off the open areas as
soon as possible and DO NOT work in a dirty environment.
•
ACID. Air and moisture cause a chemical breakdown of the oil and/or the refrigerant itself. The acid
will accelerate the deterioration of the softer metals (i.e., copper) and cause metal plating as the softer
material begins to cover the inside of the system. If this condition is not stopped, it can result in the
total destruction of your equipment.
Compressor Oil Color Code
BLACK OIL — indicates carbonization caused by air in the system.
BROWN OIL — indicates copper plating caused by moisture in the system.
GRAY OR METALLIC OIL — indicates bearing wear or piston scoring.
NOTE: If the compressor oil is discolored, perform a compressor oil acid test (oil test kit P/N 203-457).
If the compressor oil shows an acid condition, change the oil, the in-line oil filter, the filter drier and
perform a refrigeration system cleanup.
Refrigeration System Preparation and Hookup
1. Recover all refrigerant from the system and reduce the unit pressure to the proper level (US Federal
Law requires a -17 to -34 kPa, -0.17 to -0.34 bar, 5 to 10 in.vacuum that is dependent upon the
recovery equipment used).
2. Break vacuum with refrigerant and equalize system pressure to 0 kPa, 0 bar, 0 psig. Replace the liquid
line filter drier.
3. Confirm that the Evacuation Station functions properly and determine “Blank Off” Pressure. The
Blank Off Pressure of the Vacuum Pump is the deepest vacuum that the vacuum pump can attain
when isolated from the rest of the system.
If a vacuum pump (isolated from a system) is started and the Micron Meter responds quickly by going
to a deep vacuum, the operator can be confident that the pump and oil are in good condition. If the
vacuum pump fails to reach a deep vacuum within 5 minutes, the operator should suspect the
condition of the oil or the pump. It is recommended that the pump oil be changed first to see if the rate
of reaching a deep vacuum is improved.
4. Connect the Evacuation Station and refrigerant tank with gauge manifold (optional) to the unit.
Connect evacuation hoses to the compressor suction and discharge service lines and the receiver tank
outlet valve.
5. Mid-seat the receiver tank outlet valve.
6. Replace valve stem cap on the receiver tank outlet valve.
CAUTION: Do not attempt to evacuate a refrigeration system until it is certain that the system is
leak free. A system with less than a full charge of refrigerant should be thoroughly leak tested.
Any leaks found must be repaired.
Содержание Thermo King CRR DF MPC2000
Страница 5: ...4 ...
Страница 11: ...List of Figures 10 ...
Страница 13: ...Introduction 12 ...
Страница 19: ...Safety Precautions 18 ...
Страница 21: ...Service Guide 20 ...
Страница 47: ...Unit Description 46 ...
Страница 97: ...Microprocessor Controller 96 ...
Страница 101: ...Electrical Maintenance 100 ...
Страница 141: ...Structural Accessory Maintenance 140 ...
Страница 147: ...Refrigeration System Diagnosis 146 ...
Страница 149: ...Electrical Refrigeration and Controller Menu Flow Diagrams 148 This page intentionally left blank ...
Страница 150: ...149 CRR DF MPC2000 Controller Diagram ...
Страница 151: ...150 CRR DF MPC2000 Main Relay Board Electrical Diagram ...
Страница 152: ...151 CRR DF MPC2000 Unit Wiring Schematic Low Speed Winding ...
Страница 153: ...152 CRR DF MP3000A Controller Diagram ...
Страница 154: ...153 CRR DF MP3000A Main Relay Board Electrical Diagram ...
Страница 155: ...154 CRR DF MP3000A Unit Wiring Schematic Low Speed Winding ...
Страница 157: ...156 CRR DF Refrigeration System Components Page 2 of 2 ...
Страница 159: ...158 CRR DF Off Cycle Standby Flow and Pressure Diagram Page 2 of 2 CRR DF Off Cycle Standby Flow and Pressure Diagram ...
Страница 161: ...160 CRR DF Full Cool Flow and Pressure Diagram Page 2 of 2 ...
Страница 163: ...162 CRR DR Evacuation Station and Unit Connections Page 2 of 2 ...