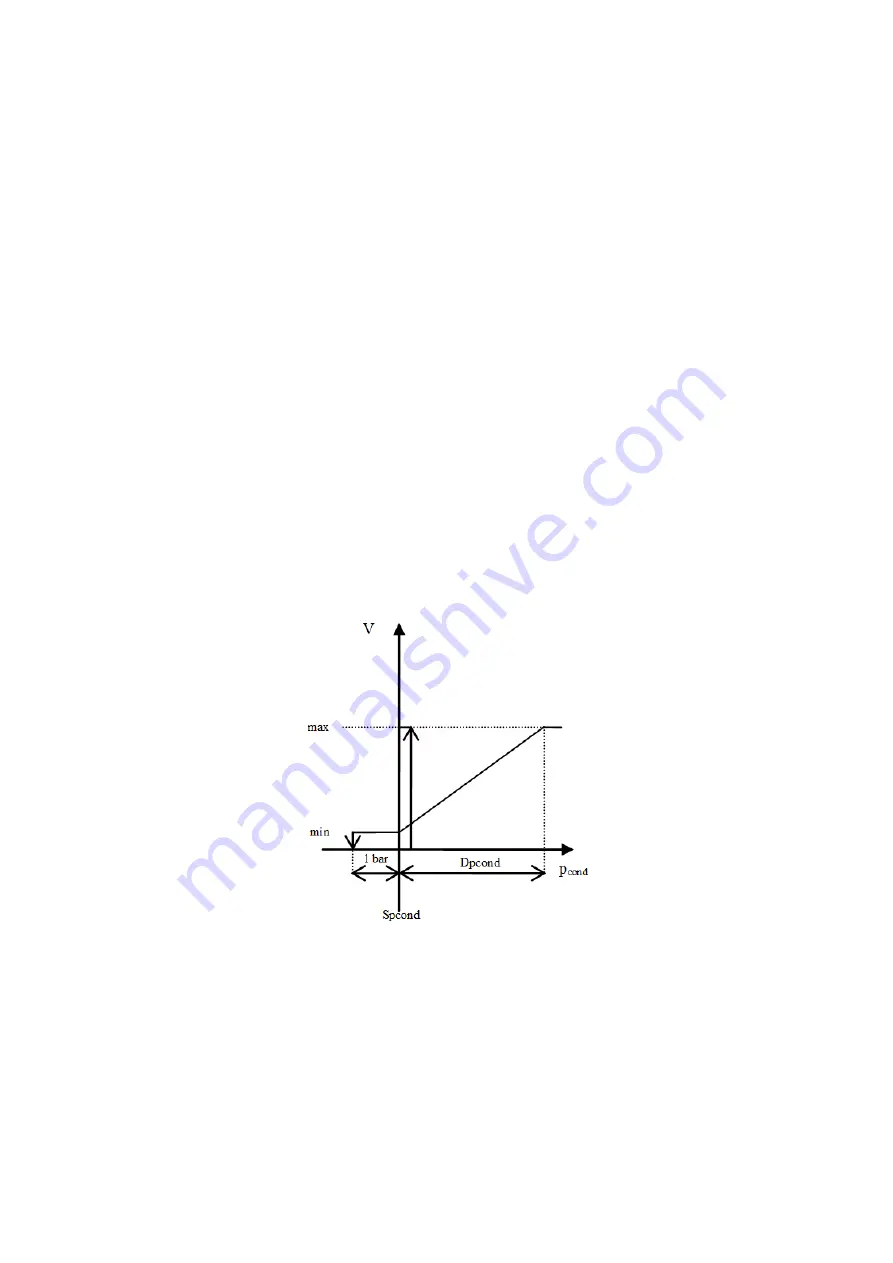
We reserve the right to make changes without prior notice
46
6.6.2 Compressor alternation and power equalisation
Compressor alternation can be enabled to keep a balance in the number of hours of operation.
Alternation is based on the FIFO principle (First In First Out). The first compressor on is also the first off.
Similarly, the first compressor off is the first on.
Units featuring four compressors - connected in pairs - have a power equalisation function which is designed
to start the compressors in the two circuits in an alternating manner, thus balancing power in the two refrigerant
circuits. Compressors get started as follows: one compressor in the first circuit followed by one in the second,
then the second compressor in the first circuit followed by the second compressor in the second circuit.
6.6.3 Condensation control
The controller is designed to manage two monitoring options of the fans fitted in the heat exchanger on the
source side, and to monitor the condensing pressure during operation in cooling mode.
The first option consists in managing the fans in the heat exchanger on the source side according to an
ON/OFF logic: the fans on the source side are started by closing the corresponding digital output as soon as
the condensing pressure exceeds the threshold setpoint stored in the controller.
The second option consists in managing the fans in the heat exchanger on the source side according to a
modulating logic: the 0-10V control signal in the fans (V) is modulated proportionally to the condensing
pressure. As soon as the condensing pressure exceeds the setpoint (Spcond), the controller engages the
digital output and, at the same time, forces the analogue output to its max. for a preset time, otherwise known
as speed-up time. In this way, the signal proportionally follows the pressure variation within the corresponding
differential (Dpcond).
The control signal of the fans may range between the min. and max. setpoints.
If the condensing pressure drops below the setpoint, the analogue output preserves the min. setpoint value.
When the condensing pressure setpoint, reduced by 1 bar, is reached, the controller zeroes the analogue
output and disables the digital output.
Two separate setpoints and differentials can be set for operation with two active compressors or with one
compressor active in each refrigerant circuit. The set-up logic does not change. If the unit features two
refrigerant circuits, the fans in each circuit are controlled independently, however the setpoints and the
differentials are the same for both circuits.
6.6.4 Evaporation control
In units with a heat pump, which operate in heating mode, the controller is designed to manage two monitoring
options of the fans installed in the heat exchanger on the source side, and to monitor the evaporation pressure,
as explained for condensation control.
The first option consists in managing the fans in the heat exchanger on the source side according to an
ON/OFF logic: the fans on the source side are started by closing the corresponding digital output as soon as
the evaporation pressure drops below the threshold setpoint stored in the controller.
The second option consists in managing the fans in the heat exchanger on the source side according to a
modulating logic: the 0-10V control signal in the fans (V) is modulated proportionally to the evaporation
pressure. As soon as the evaporation pressure drops below the setpoint (Spevap), the controller engages the
digital output and, at the same time, forces the analogue output to its max. for a preset time, otherwise known
as speed-up time. In this way, the signal proportionally follows the pressure variation within the corresponding
differential (Dpevap).